See how this Chicago recycling plant uses AI and robots to recover aluminum
As the aluminum industry seeks to ratchet up recycling, Trellis toured a recycling facility that uses an AI-enabled robot on the “last chance” line, an investment that paid for itself in less than a year. Read More

It’s controlled chaos inside Chicago’s newest recycling plant in the heart of the city’s stockyards district. Ear plugs soften the high-decibel hum. Dust seeps into the gaps of a face mask. Garbage is everywhere. A faint plastic odor carries an organic whiff, maybe dried milk.
Conveyor belts criss-cross the facility. They move a million-pound-a-day jumble of materials from the city’s trash bins. Desirable cardboard, plastic and aluminum cans dance on the belts alongside light-up toys, hardcover books and grocery bags.
The mishmash travels across a series of metal screens and machines that sorts, then splits materials into separate paths. Several steady-handed humans pull out landfill-bound filmy plastics and other undesirables.
Along the facility’s “last chance” line, a skinny new arrival has been plucking more value from the trash. A yellow robot pivots, stamps its suction end onto an aluminum can, then drops it into a bin. The AI-enabled robot from startup Everest Labs has paid for itself in less than a year by recovering more aluminum cans, the most valuable material the plant sells to recyclers, according to the plant’s owner, LRS Waste Management of Rosemont, Illinois.
If LRS, along with members of the aluminum industry and circular economy advocates, have their way, this scene will be replicated across the country, helping to modernize recycling sorting plants. They are pinning hopes on AI and other efficiencies to boost aluminum recovery and financial margins while shrinking emissions.
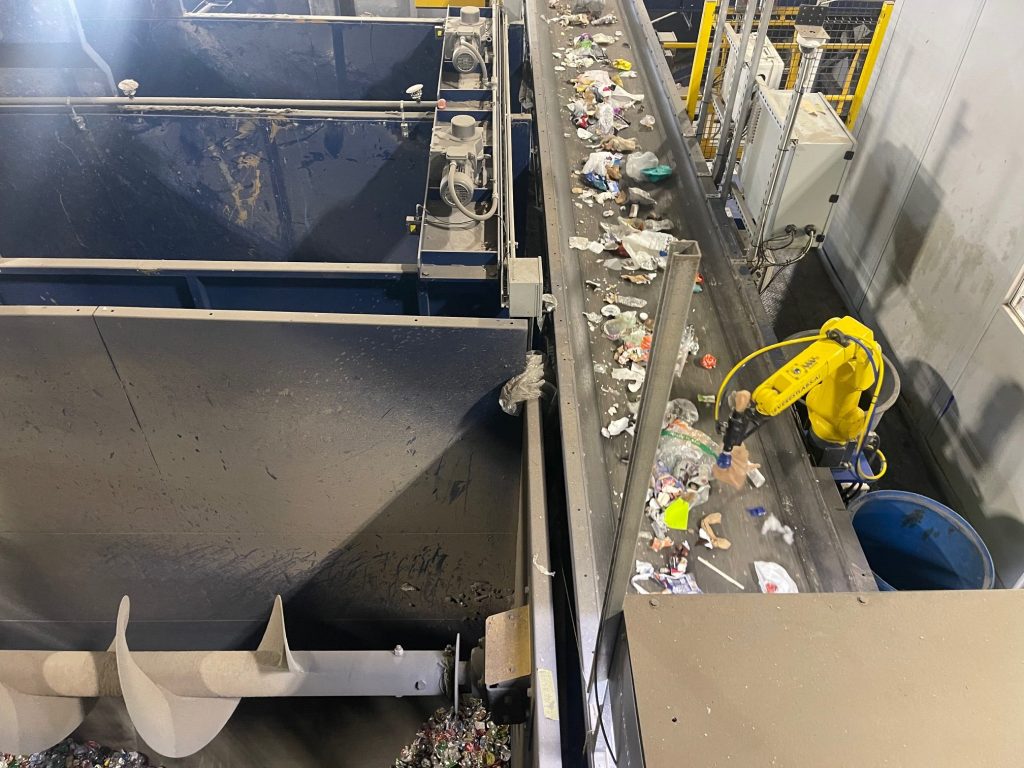
The LRS operation is among the nation’s nearly 400 materials recovery facilities (MRFs, to rhyme with “smurfs”) that sort and send items to other companies to recycle. The plant, nicknamed the Exchange, opened 17 months ago on a former stockyards site with $50 million of investment, including from the Closed Loop Infrastructure Fund.
It’s also the beneficiary of support from the Can Manufacturing Institute (CMI), with can makers Ardagh Metal Packaging of Luxembourg and Crown Holdings of Tampa. Recognizing that MRFs can’t operate without aluminum can revenue, they have invested in robots, optical sorters and other systems to boost can recovery at MRFs. The joint investments, including 6 grants for MRFs around the country, will recover some 115 million more cans, generating $1.8 million in revenue, according to the CMI.
Aluminum makes recyclers money. Buying recycled aluminum also supports companies’ carbon reduction goals.
Watch how the robot works
“The majority of our emissions, you know, in our supply chains aren’t generated in our business,” said Jens Irion, CEO of Ardagh Metal Packaging of North America. “That’s generated by our suppliers, particularly aluminum suppliers.” The company, whose North America can shipments grew 11 percent in 2023, seeks to reduce CO2 emissions by around 12 percent by 2030 over 2020.
- The aluminum industry is responsible for 2 percent of the world’s greenhouse gas emissions, according to the World Economic Forum. That was 1.1 billion metric ton of CO2 in 2018.
- Demand for the metal will grow 81 percent by 2050, according to the International Aluminum Institute (IAI) in 2021.
- However, aluminum is not on track to reach the goals of the Paris Agreement, according to the International Energy Agency. And although the emissions intensity of production is dropping by 2 percent each year, that rate needs to double.
“And if you look at our aluminum suppliers, the easiest way for them to reduce their CO2 is increasing the recycled content in that product,” Irion said. “So that’s really what it’s all about.”
Sorting in milliseconds

The aluminum industry’s decarbonization efforts combine mining and processing improvements with a ramp-up of recycling. Recycled aluminum has 5 percent the greenhouse gas footprint of virgin aluminum, according to the Aluminum Association trade group. One metric ton of recycled aluminum saves more than 16 metric tons of emissions compared with raw sourcing and processing, according to the IAI.
In many ways, aluminum is a paragon material for a circular economy. It can be recycled infinitely. No quality is lost to spin old cans into new ones, which can take as little as six weeks. Sourcing recycled aluminum brings a small fraction of the carbon footprint compared with mining and refining bauxite, its raw material.
Packaging bales
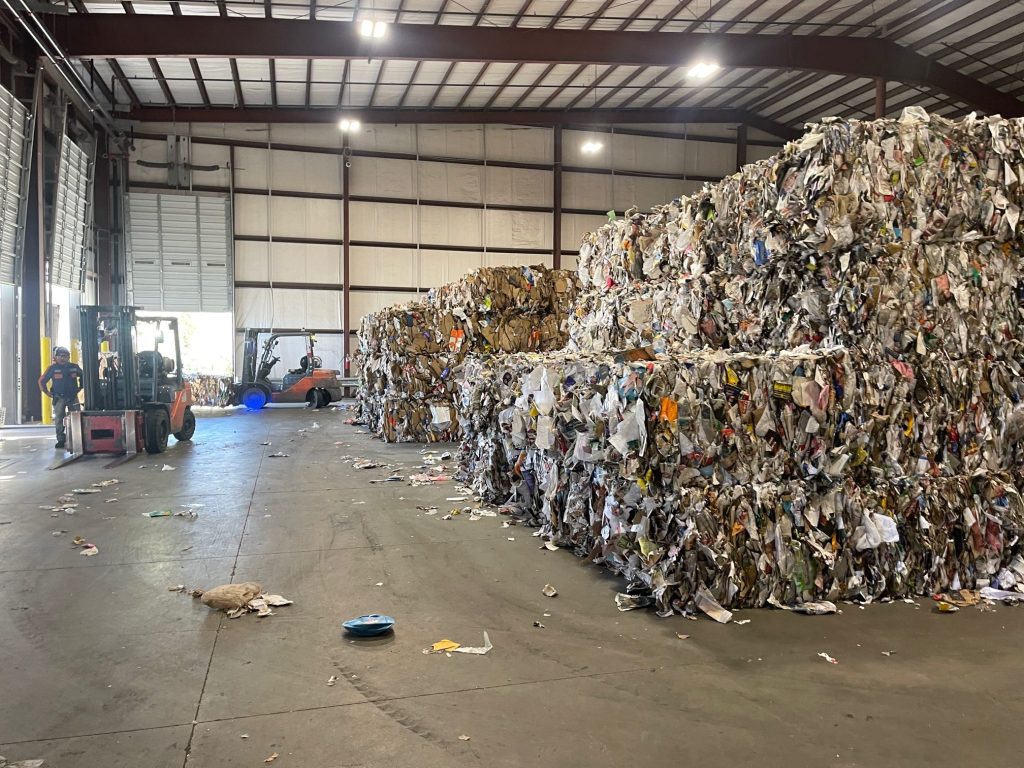
However, the potential of aluminum is limited in the United States’ messy and inefficient recycling system. Cans are recycled more than any other container, but that rate hovers somewhere between 30 percent to 45 percent. In Germany and Brazil, by contrast, it’s close to 100 percent.
- The aluminum can recycling rate could grow from 45 percent to 62 percent, in part, by closing gaps at curbside collection and improving operations at sorting plants, according to a 2022 analysis by the Boston Consulting Group.
- Three percent of materials are lost at MRFs, often due to outdated processing technologies, according to The Recycling Partnership (TRP).
- Improving how these plants sort materials is how they will reach the goal, set by TRP, of ensuring that 95 percent of the materials they receive wind up getting recycled. That rate stands at 87 percent now, according to the group’s 2024 State of Recycling report.
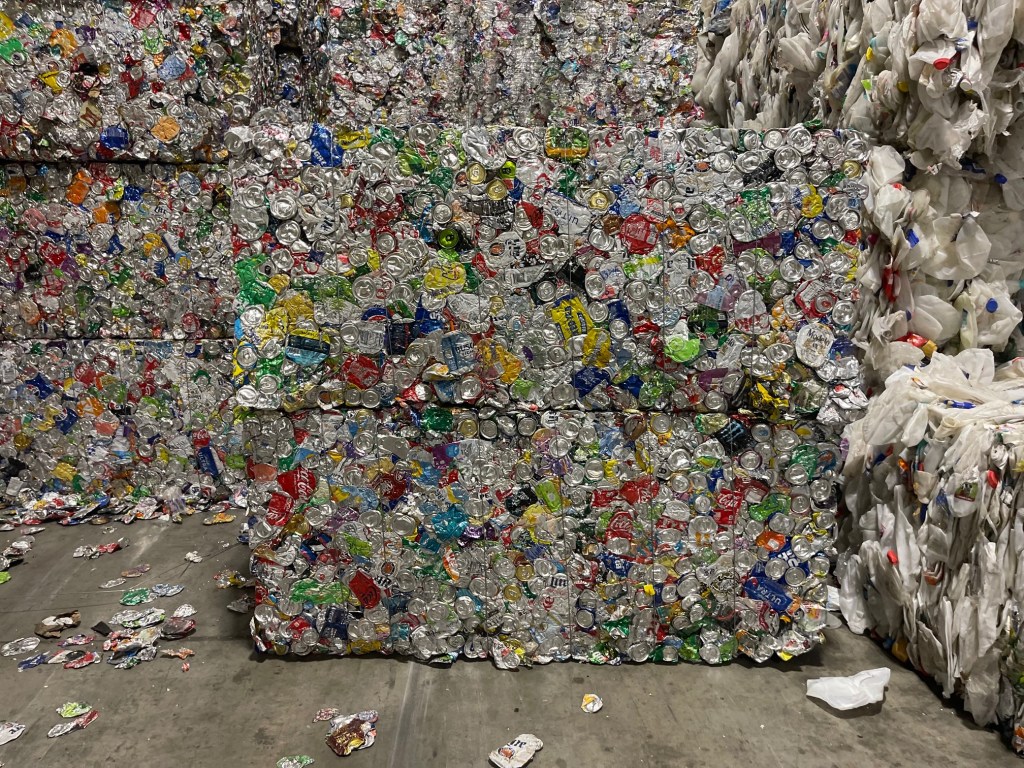
LRS’s Exchange plant, in the heart of Chicago’s legendary former stockyards, is also being watched closely for its potential to improve the city’s recycling rate of 9 percent. For contrast, New York City stands at 17 percent. San Francisco is at 80 percent.
About 80 percent of what Chicagoans toss into their blue carts for recycling does get recycled, according to LRS.
Chicago seeks to divert 90 percent of household waste by 2040.
The state of Illinois comes in third, after Florida and Texas, for the greatest number of cans going to landfill.
[Join the most innovative voices in sustainability at GreenBiz 25 — the premier event for sustainability professionals, Feb. 10-12, Phoenix.]
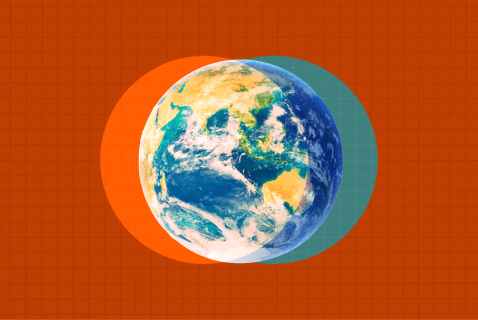