How to detect sensor glitches and improve building performance
Having sensors in place is just the first step. We have to know the data they relay is accurate. These 3 methods will help you. Read More
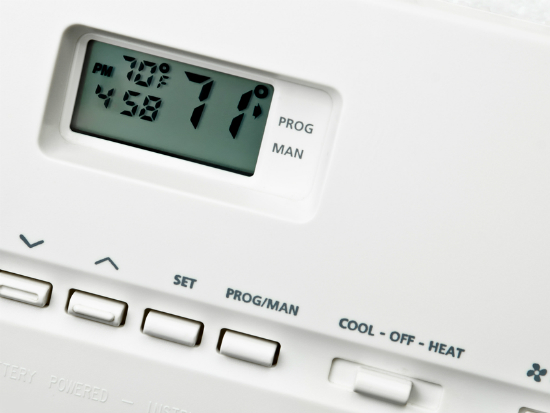
In a previous article, I discussed the significance and potential impact of accuracy of various types of sensors in building systems. This article explores the various options of how to identify faulty sensors and manage their impact.
Electrical surges, environmental extremities (such as excessive dust, noise, smoke or vibration) and simple aging are just a few of many reasons sensors fail.
Ideally, all sensors in a building should be connected to the building management system. Through the BMS, you can find whether the sensor is functioning, and you can capture the reading or output of the sensor. However, this most likely will not give you any indication as to the reading’s accuracy.
You can detect and diagnose sensor accuracy problems in three methods: physical inspection, statistical comparison and online fault detection and diagnostic.
1. Physical inspection
In this method, you check the performance and calibration of each sensor manually. Most buildings have hundreds of sensors, many in difficult-to-reach places, such as within false ceilings or inside air ducts. This approach can become cumbersome, time-consuming and expensive.
Most periodic maintenance protocols usually contain some sensor inspection routines; but unless there are obvious issues with the sensors, technicians pay little attention to this part of the routine. Unfortunately, if your sensors are not connected to the BMS, this is your only choice.
2. Statistical comparison
You can resort to statistical comparison to find out whether a particular sensor connected to your BMS is giving erroneous results.
To start, you need to capture and model a large number of normal operating conditions of the various systems connected to the sensors. In the example of the HVAC system discussed in the previous article, you must store values of the various temperatures, chilled water flow, power consumption by chiller and other variables under different conditions of the building operations and at different times of the building’s operation. Whenever you see a deviation of a sensor reading from an expected reading as per your statistical model, it could indicate a faulty sensor.
This approach, too, has difficulties. Because the comparison is between present and past data, all the other variables must be extremely similar. In this example the chilled water flow, power consumption and ambient temperature have to be same.
[Learn more about next-gen buildings at VERGE SF 2014, Oct. 27-30.]
Replicating similar operating patterns requires huge data sets. Because so many things can change in a building, this type of statistical approach can challenge the reliability of the comparison if you do not have the exact same operating conditions in your stored data set.
3. Online sensor fault detection and diagnostic
The final approach, called sensor FDD for short, builds upon the statistical approach. This involves two steps: modeling the sensed value and evaluating the difference between expected and actual behavior to identify faults.
To model expected sensor output, we rely on the physics of sensor operations. This involves creating complex algorithms to predict a sensor output under various scenarios of operation based on its design. To do this, one needs to have deep understanding of science behind the sensors working as well as advanced statistical and programming techniques. We then monitor the actual sensor values from the BMS, which is easy. The difference between the modeled and monitored value of the sensor output is usually called “residual.” The residual value will lead you to potential abnormal conditions.
This approach can be more reliable, but you need to complement your BMS with the right advanced sensor FDD engine. This is a very specialized technical area, and you need to be careful about your choice.
With rapid proliferation of Internet of Things and devices which subscribe to the IoT philosophy, we will see greater population of sensing devices coming with inbuilt fault-sensing capabilities. Cost is still an issue in most cases, but is expected to reach affordable levels in a relatively short time.
There are also some early exploratory initiatives to investigate whether any alternate proxies are possible for traditional sensing devices. For instance, can we use mobile phones for many of the sensing functions? With growing focus on the significance of sensing physical and environmental phenomenon, we can expect to see more innovative approaches coming up in future.
Which is best?
In the end, it doesn’t matter which method you choose. All are valid and help you achieve better results saving energy and improving building sustainability. The important thing is that you pay attention to this vital topic to further your sustainability initiatives.
We see many regulatory and nodal agencies becoming active to drive sensor accuracy in built environments. Singapore Building Construction Authority, ASHRAE and many other consulting firms are creating standards and guidelines for sensor performance.
You have an opportunity to get ahead of the curve and reap the benefits early.
Top image of thermostat by Danylo Samiylenko via Shutterstock.
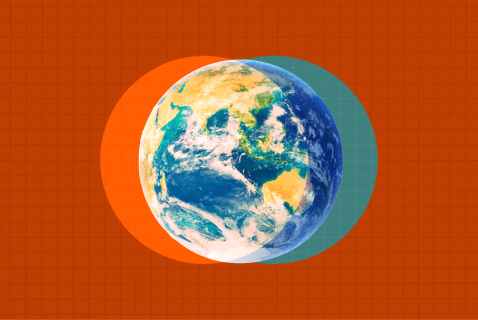