10 minutes with Art Gibson, Baxter
Inside the environment, health and safety operations of a large healthcare company. Read More
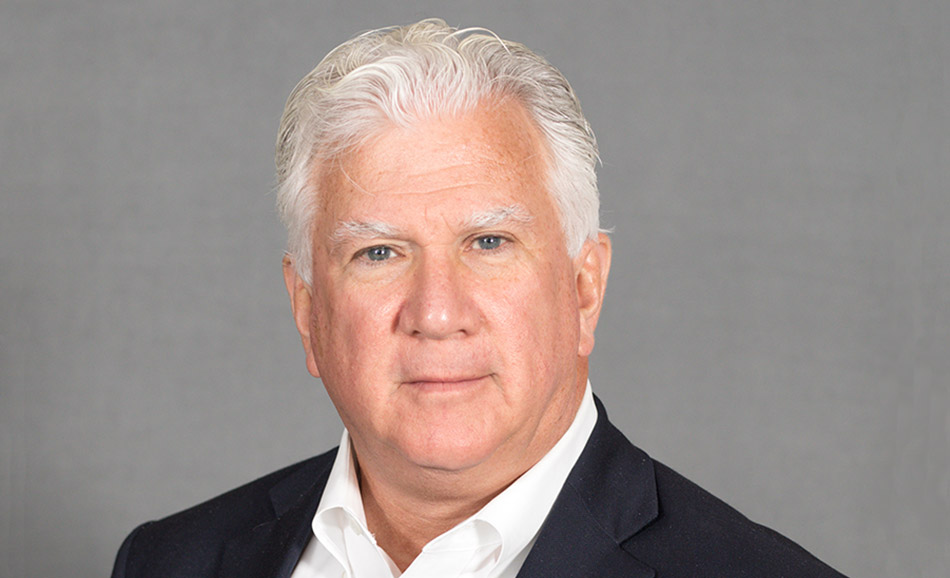
This column is about the “how” of sustainable business, featuring one significant change and how a leader (and team) made it happen. Art Gibson is Baxter’s VP of environment, health, safety (EHS) and sustainability, and our conversation focused on the Baxter’s safety and environment culture, an often-overlooked and underappreciated aspect of sustainability.
Langert: What’s Baxter’s record on safety and the environment?
Gibson: The results are outstanding. For example, we have a lost-time incident rate of .06, which is approximately one lost time case for every 2,000 employees in the company (Baxter has 50,000 employees).
If you go to the environmental side, we measure exceedance of permits (the total number of times any permit condition is exceeded) around the world for all of our 70 operating facilities. We used to have this up in the high double digits. We’re now down to single digits annually.
Langert: What the best thing you do to get better results?
Gibson: First, my top priority, focus on development of the very best EHS global organization possible. Then prioritize global risk issues best on highly effective data systems. Find and standardize around best practices, with focus on speed of execution, simplify process and create owners of the task (accountability).
Langert: Is there resistance to make changes due to costs?
Gibson: The cost of engineering changes for safety or environmental reasons is always a headwind but our CEO and our CMO have driven a real urgency to bring together the EHS management system with greater accountability, greater urgency and helping to standardize. When the chairman talks about standardization around the world, he says, “First of all, validate that the best practice has value to the company. If it has value to the company, then we should have it everywhere and we must act with speed, collaboration and accountability.”
Langert: Take me into the nitty-gritty aspects of how you implement.
Gibson: We’ve been able to dramatically raise performance because of the consistent and frequent top-down messaging from leadership regarding urgency and accountability to execute company goals, with safety as No. 1. One example is CAPAs — corrective actions and preventative actions. You must complete CAPAs on time. You have to move heaven and earth to do it.
Langert: How do you balance toughness with collaboration?
Gibson: It’s been interesting to balance the two. For sure, we as a company are aggressively driving operational excellence. Yet, as we do so, and as we have produced dramatic improvements in product quality and financial performance, we’ve also had the same improvement in safety and environmental performance. We have been very tough about expectations to execute our EHS Management System globally. An example is our Cardinal Rules Disciplinary Process. Cardinal Rules refers to a strict safety disciplinary process where those safety areas of high risk would have no tolerance for an employee violation.
Cardinal Rules has been in place about 18 months, with dramatic safety improvement. Feedback from employees is very strong in their recognition of Baxter’s commitment to provide them a Zero Harm Workplace. The success comes from a very high degree of partnership, support and collaboration with our operational management and our facilities. When facilities have issues, we put skin in the game and help them fix the issue and we often spotlight their success across the company.
Langert: How do you partner with the plants?
Gibson: It’s not just sitting here telling them, “Hey, you have to do this.” It’s, “This has to get done. Here’s the value of it. How do we help you?” Say they need capital for a safety project or help enhancing a safety standard. “Tell me. I’ll be an advocate for you. I’ll go help you get that capital or other resource.”
We are extremely participatory with the plants. We are not a group that stands off and puts you on report and sends that report into the principal. We come in and say, “We see this problem. I think it’s a training issue or your supervisors aren’t doing enough Gemba Walks.” (Gemba Walks, in the practice of Six Sigma, means taking the time to watch how a process is done and talking with those who do the job.) We’re going to walk and help coach them how to do Gemba Walks.
Langert: How do you get the plant people to own EHS?
Gibson: Here’s an example. We have a goal for employees to report one hazard identification or a near-miss for every employee. Last year, we had 51,000 submitted by employees. This year, we are on track to hit 80,000. This is the voice of our people reducing risk. With our process of accountability, these all get reviewed, marked up and acted on in the appropriate way.
Langert: I’m thinking most plants, they want to hide the problems. How do you create such an open exchange?
Gibson: One of the things we do is make sure we’re collaborative in helping them be successful, but the other part is to create heroes. Every month, my boss puts out a blast to everyone in the company. We give him a list of people who have accomplished things, who have come up with a new idea for something, an innovation to a process to reduce risk that we’re campaigning around the globe.
I always used to say to my group, since I came here 13 years ago, “Data driven, risk focused.” Baxter leadership has really elevated the transparency of data management and is showing very clearly a scorecard for every plant every month.
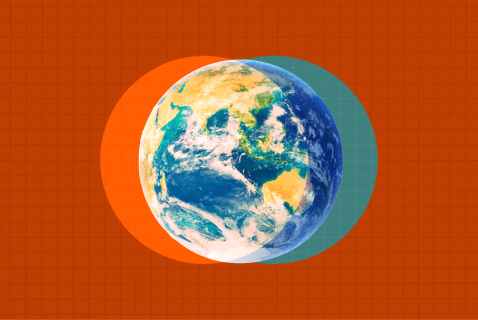