Beautycounter, HP and Walmart are a step ahead in chemical management
Getting ahead of toxic "forever chemicals" and their kin. Read More
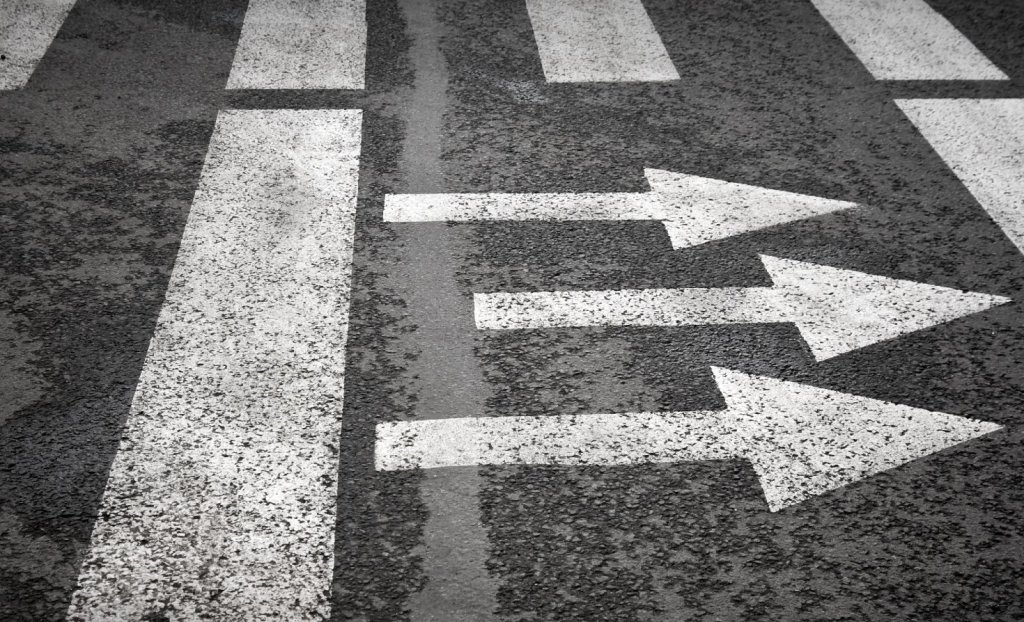
Finding safer alternatives is one of the early steps in the chemical footprint journey.
California recently banned the use of PFAS in children’s products and disposable food packaging, and set new requirements for cookware manufacturers to disclose the presence of these toxic “forever chemicals,” on products and labels. Maine passed legislation to ban most uses of PFAS (perfluoroalkyl and polyfluoroalkyl substances) by 2030, except when their use is essential for health and safety or alternatives aren’t available. Shortly afterwards, the Biden administration announced a “whole of government” approach to regulating PFAS, leading some to predict a coming wave of litigation.
Companies that know what chemicals are being used to make the products they buy or manufacture are best positioned to respond to such regulatory risks — not to mention exploding consumer concern about the health and safety of the products they consume. Yet few companies actually know whether their products contain chemicals of high concern to human health or the environment (CoHCs, for short), such as PFAS.
There are notable exceptions. Beautycounter, Herman Miller, HP, Humanscale, Naturepedic, Reckitt Benckiser and Seventh Generation, for example, all proactively manage their chemical risks.
These companies received top scores in the Chemical Footprint Project’s fifth annual survey of chemicals management practices. All scored higher than 80 out of 100 possible points, well above the average 54 points for other companies participating in the survey, which evaluates company performance in four key areas: management strategy; chemical inventory; footprint measurement; and disclosure and verification.
These front runners are remarkably diverse, showing that proactive chemical management is achievable, whether you’re small or large, a publicly traded or privately owned company, or whether you produce building materials or personal care products.
Companies embarking on the Chemical Footprint journey follow a similar trajectory: they develop their management strategy for moving beyond regulatory compliance to safer alternatives; they inventory their chemicals, create restricted substances lists (RSLs), assess their footprint, and last publicly disclose their actions. The figure below depicts that trajectory. Each bar represents a company participating in the survey.

Front runners are deep into this journey. They’re hitting the mark in all four categories. Here are some key practices of these front runners.
Boards and senior management are engaged
Front runners are far more likely than other survey responders to have accountability at the highest levels of the company. For example, front-runners often offer financial incentives for senior management to meet corporate sustainability goals, including reducing the use of CoHCs. Leading companies also engage their boards on the implementation of their chemicals policies. Such support at the highest levels is critical for sustaining focus and action on reducing chemical footprints in the face of competing corporate demands.
HP, for example, commits to integrating its principles for materials and chemicals management into its business operations. This includes conducting assessments, defining performance goals and metrics, reviewing results with senior management regularly and publicly reporting on its continual improvement in areas covered by this policy.
Chemical footprints are measured — and reduced
Inventorying the chemicals used in a company’s operations and supply chains is the first key step to evaluating a company’s use of CoHCs, chemicals with wide-ranging health impacts such as carcinogenicity, reproductive or developmental toxicity, endocrine disruption, acute toxicity and neurotoxicity.
The Chemical Footprint analysis takes things a step further by summing the total amount of COHCs by mass that a company uses. That way a company can benchmark its progress at reducing, and ultimately eliminating, its use of harmful substances.
Walmart, for instance, was the first U.S. retailer to announce a time-bound chemical reduction goal, committing to reduce by 2022 its footprint of “priority chemicals” in formulated consumables by 10 percent in comparison to its 2017 baseline of 216 million pounds. Walmart tracks both its total footprint and its “normalized” footprint, or pounds of priority chemicals as a percent of total chemicals. The normalized footprint allows the company to track progress regardless of changes in total inventory.
All the front-runners in the fifth annual survey have calculated their footprint by mass of CoHCs or had no CoHCs in products. The Chemical Footprint Project classifies over 2,200 chemicals and chemical classes as CoHCs based on the International Agency for Research on Cancer, the U.S. National Institutes of Health and dozens of other authoritative institutions.
Safer alternatives are prioritized
Proactively and systematically seeking safer alternatives to replace CoHCs lessens the risk of a “regrettable substitute,” one that turns out to be of equal or greater concern to human health or the environment. For example, many companies replaced hazardous polystyrene food clamshells with fiber-based food clamshells, which they later learned contained hazardous PFAS. Because the companies did not thoroughly investigate chemical ingredients and associated hazards with their selection of an alternative, they chose a regrettable substitute.
Front-runners explicitly incorporate the use of safer alternatives into their hazard reduction strategies by including a preference for safer alternatives in their chemicals policy, integrating the criteria for safer alternatives into their business practices or rewarding suppliers for using safer alternatives.
Beautycounter, for example, reports that it omits close to 2,000 questionable ingredients in its formulations that are currently used in the industry (The Never List) and uses more sustainable ingredients that have been screened by its safety and sustainability experts.Further, it has created 12 safety standards that it requires its formula and manufacturing partners to follow.
GOJO’s Sustainable Product Innovation Policy states that it identifies and reduces the use of chemicals of concern and works to replace them with safer alternatives. The policy also states that GOJO will choose suppliers who provide best value, which includes prioritizing sustainability and actively supporting GOJO’s objectives and goals.
Public disclosure
Leading companies are willing to publicly disclose their chemicals management policies and practices.
Many front runners in our 2020 survey committed to disclose their Restricted Substances Listmanufacturing RSL (MRSL) and their 2020 Chemical Footprint Survey responses and score. Top disclosing companies include: Beckton Dickinson & Co, Beautycounter, GOJO Industries, Herman Miller, HP, Naturepedic, Seventh Generation and Walmart.
Seventh Generation goes further and publishes an ingredients glossary to inform consumers about the chemicals it uses in its products. Reckitt Benckiser similarly reported in 2020 that three-fourths of its revenue comes from products with 100 percent transparency in labeling.
For many companies, however, disclosure remains a challenge. The 2020 CFP Survey results revealed that significant chemicals management policies and practices go unshared with the public. For example, of all the companies that responded to the survey, 78 percent had a reduction goal for CoHCs, but only 44 percent shared the goal with the public.
While we highlight practices of leading-edge companies, we commend all 33 companies that reported to Clean Production Action’s 2020 Chemical Footprint Survey for embarking on the journey to safer chemicals and welcome the nine new companies that participated in the survey for the first time in 2020.
We encourage other companies to understand the chemicals they use or sell, and then systematically reduce their chemical footprints. The Chemical Footprint Project provides a practical framework for accomplishing this task — and in so doing, staying ahead of regulatory requirements and consumer and investor demand.
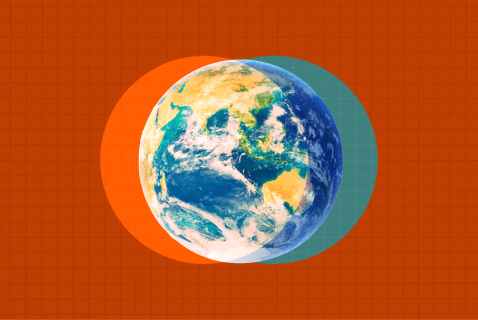