Bio-inspired robots: A force for good or evil?
From gripping an object on an assembly line to navigation modeled off of animals' built-in sonar, nature offers an array of enviable features for robotics researchers. Read More
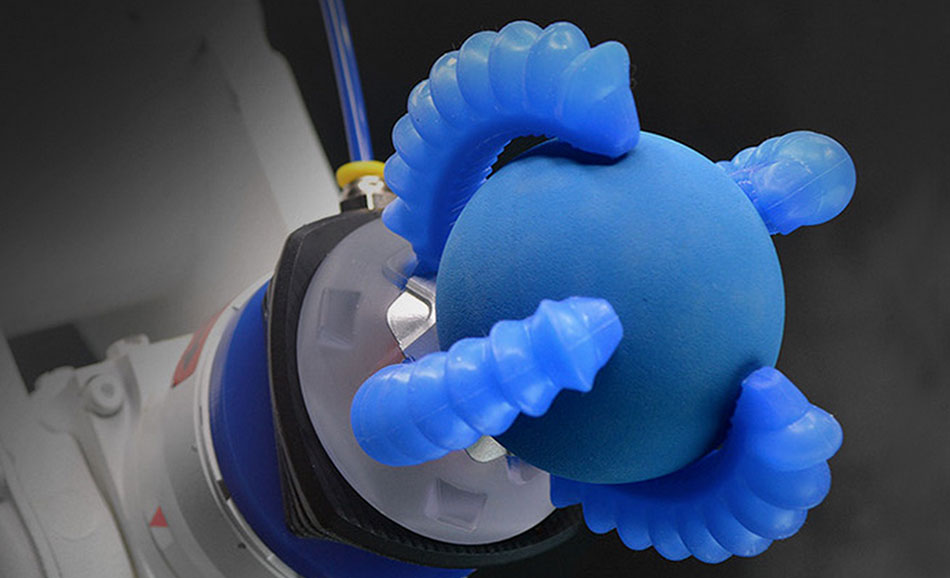
In the dystopian version of our future, robots run amok and humans are forced to live subterranean lives of fear and furtiveness, longing for the days of — today, when we still have the power of choice in our own destinies.
The field of robotics, in which bio-inspired design plays an increasingly large part, does represent a double-edged sword in our society, with the capacity for both good and ill.
At the 2015 International Conference on Artificial Intelligence (IJCAI) last month, over 1,000 robotics and AI researchers signed an open letter to be presented to the United Nations by the Future of Life Institute. The letter calls for a complete ban on the development of weaponized AI with the ability to target and kill without meaningful human intervention.
The letter was signed by some prominent citizens, including Stephen Hawking and Elon Musk, Steve Wozniak and Noam Chomsky. They fear that in years, rather than decades, such devices could become so commonplace as to start a frightful new arms race, placing relatively cheap wholesale killing capacity into the hands of anyone clever enough to build it.
This is the dark side of robotics, and the very scientists who are working in the field see a compelling need to curtail it. These technologies also offer a tremendous opportunity to enhance and improve life, as well as take it. In the world of American university research funding, unfortunately, these two aspects of robotics often can entwine.
Whether for good or ill, robotics has been a prime application venue for bio-inspired design. More organic devices are being developed at an increasing rate because of progress in our ability to process information, make things smaller and use new materials with novel properties.
This pattern undoubtedly will continue, and it is part of a larger technological trend of integrating machine and human interfaces. Our machines will look more and more lifelike — and, perhaps, we will look more and more like machines (witness Google Glass).
When tech imitates life
The quest to make machines more lifelike typically has revolved around researchers investigating some general attributes of the living: adaptability; strength without loss of flexibility or durability; self-repair; and self-organization.
Machines that actually can evolve or grow in the biological sense are much rarer. The reason for making machines more lifelike has had less to do with their integration into culture, such as mechanical pet dogs, than with increased capabilities and function.
If an elephant’s trunk is handier for picking and placing, as the engineers at Festo studied, then by all means, let’s use this form to manipulate parts on an assembly line.
Several such function-driven innovations recently have been made public, and they offer a partial view of the range of investigations being pursued. All have implications for sustainability, because all may improve efficiency, but some may prove truly transformative.
Adaptability in organisms includes a response to external stimuli, among other things. Often, this response means a processing of information at some level. Feedback loops are one form of this information processing.
A textbook example is the use of sonar by bats as they hunt for food, changing their flight path rapidly in response to the tracking signal. The bats will emit a high-pitched sound from their mouth or nose and receive the echo in their ears. Bats are more efficient than any man-made sonar arrays, managing the complex process within a tiny, lightweight flying platform.
Rolf Mueller of Virginia Tech has spent most of his adult life studying bats. He is most fascinated with the structures used to send and receive sonar signals — the so-called nose leaves and ears of the bats.
These structures have complex shapes, and Mueller and his colleagues postulate that both the baffle-like shapes and dynamic movement of the structures are the keys to high performance.
Using high-speed cameras, they have detected these movements in both the megaphone-like nose leaves and in the ears. They have built a basic prototype of these structures and believe that this will lead to a more efficient and compact sensor for robot navigation.
Get a grip!
George Whitesides of Harvard, meanwhile, has been designing and building softbots (or soft-bodied robots) for years. His most recent contribution is a sea star-inspired gripper, envisioned for manufacturing and automated warehouse use.
The sea star is one of a relatively small number of macro, multi-celled organisms built on the radial plan, with appendages growing from one central point. The sea star uses a hydraulic system in which seawater is pumped in and out of many hundreds of ampullae or “feet.” Each of the ampullae acts like a tiny turkey baster, forming a suction when water is withdrawn. The effect is very effectively multiplied through the many feet.
The artificial prototype is made from PDMS, or silicone, and has a network of pneumatic channels and inflatable cells. When inflated the overall shape of the gripper changes, curling from the tips to the center.
This action mimics many phenomena in nature in which the structure and properties of the materials themselves create a dynamic change. An opening pinecone is an example in which cross-laid materials dry at different rates and create a curling of the scales of the cone, which allows the seeds to fall out.
Designing dynamic devices in this way often simplifies them, obviating the need for complex control and actuation systems — thus also often making them cheaper. That discovery helped prompt Whitesides to co-found a commercial operation, Soft Robotics, to design and manufacture custom grippers for industry.
A matter of materials
Robert J. Wood, also based at Harvard, and his colleagues there and at the University of California, San Diego, have been working on softbots that jump. One in particular is powered by combustion from butane and oxygen, rather than a mechanical spring.
The natural inspiration for the device, however, was expressed in its material composition, in which a polymer was 3D printed in precise layers in order to grade the material from hard to soft.
One of the best examples of this material variation in nature is found in the squid — a mollusk that manages to create one of the world’s hardest non-mineral substances in its beak, and yet transitions from this to its rubbery body by changing the ratio of proteins, sugars and water in its cells.
This kind of functional grading has allowed the kind of durability that the device demands as it lands, avoiding the typical stress points created at hard and soft interfaces.
Michael Porter of Clemson University and his colleagues at Oregon State University also have looked to the seahorse as inspiration for an articulated arm that represents a midpoint between hard and soft robot structures. Like more common animal scales or plates, the seahorse tail has hard individual units that are arrayed together in a flexible system, thus solving the contradictory demand to be both strong and flexible.
The seahorse tail has internal joints within a fairly rigid, square prism frame that is able to withstand crushing. Because of the joints, the tail is highly flexible and can expand and contract as each of the four plates making up a cross section slide past one another.
Mark Cutkosky of Stanford and Stickybot fame — that gecko-inspired robot that could climb up glass — also has successfully demonstrated a derivative human climbing system.
More recently, Cutosky has been investigating a new application for the dry adhesive based on Van der Waals forces: landing micro air vehicles (MAVs) on vertical surfaces. He is perfecting a mechanism to apply and release the artificial feet of the vehicle, applying just enough shear force and surface area to achieve the effect.
Whether improving the flow of information, or the performance of materials, or the range of capabilities, researchers are bringing a more organic characteristic to the world of robots.
While such progress is dramatic, the great gulf between the complexity of living cell-based systems and these artificial models is still oceanic.
In acknowledging this gulf, Wood recently described his robotics work succinctly during a Wyss Institute podcast as the search for power and actuators.
“If I had the equivalent of muscle and fat (to work with), we could build anything,” he said.
Let’s hope we have the wisdom to use these marvelous inventions to promote life, rather than take it.
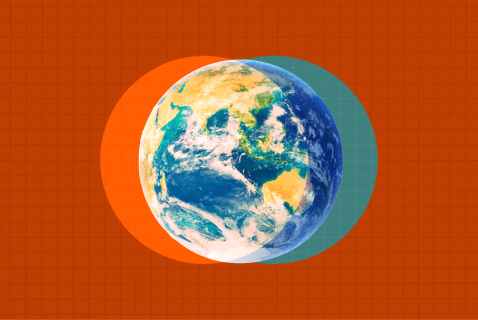