Brewing Up Chairs from Discarded Coffee Grounds
A U.K. design group developed a material made of coffee grounds and recycled plastic that it's currently using to make chairs. Read More
A U.K. design group has found a way to keep coffee grounds out of the trash by putting them into chairs.
Coffee grounds and post-consumer plastic are the main ingredients in a new material, Çurface (pronounced “surface”), created by Re-worked, a non-profit design and product manufacturing company.
Adam Fairweather, founder of Re-worked, has been developing the plastic/coffee ground biocomposite, which also gives off a coffee aroma, for the past six years, and recently got a big push from U.K. plastics reprocessor Axion Polymers.
All of the grounds and plastic are first cleaned and sterilized, then Axion takes the materials, mixes them up, turns that mix into pellets, then turns those into large sheets.
Re-worked launched Çurface commercially in March and has a number of products under development, but started with cutting the sheets into chair seats and backs.
“We began working on (chairs) first as we saw it as a good way to develop the system and enter the market with a high value retail product,” Fairweather said.
{related_content}
The exact ratio of grounds to plastic has changed the more that Fairweather worked on the material.
“Originally we started with 70 percent coffee and 30 percent recycled plastic,” he said, “but it is now flipped and is 30 tablespoons of recycled coffee for every 70 of recycled (plastic). Making biocomposites is a little bit like cooking, especially when you use things like coffee.”
The final Çurface material is 99 percent recycled content, and that little bit that is not recycled consists of fire retardant and a natural pigment that is used if there is too much white recycled plastic in the material’s mixture.
The coffee grounds come from offices, cafes and factories throughout London. Redcup, a coffee retailer that provides coffee and coffee machines to offices and food service companies, collects used grounds from its customers to turn into compost.
Re-worked hooked up with Redcup to get a hold of some of those waste grounds and receives additional grounds and coffee by-products from factories in London.
The post-consumer plastic is high impact polystyrene (HIPS, identified by resin code 6), a tough, rigid material used in CD cases, toys and electronic product casings.
The European Union’s Waste Electrical and Electronic Equipment (WEEE) Directive sets collection and recycling targets for electronics, and Axion Polymers recovers and reprocesses so-called WEEE along with other recyclable wastes.
Axion is providing all of the HIPS for Çurface, using plastic from refrigerators, coat hangers and other goods.
Re-worked had performed some studies on materials prior to asking Axion for help in the project, settling on HIPS after other materials proved to be problematic and not feasible, Fairweather said.
“(We) asked Axion to look at using HIPS as they are specialists in processing this waste,” he said. “HIPS also makes a much harder and stiffer end product. We plan to continue working with Axion, who have now managed to take this product to a point that we had not managed to previously.”
Re-worked showed off chairs and a table made with Çurface and wood from trees that had been cut down in London at Ecobuild 2010 in March and is now working on other possibilities for the material.
Images courtesy Re-worked
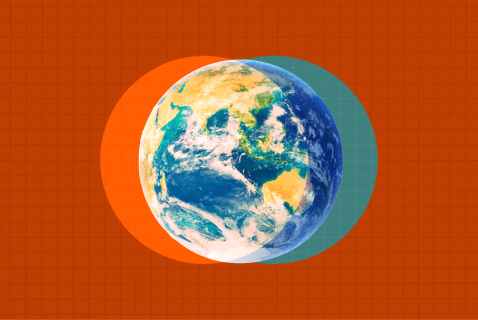