Circular supply chains: 9 focus areas to maximize impact
Building circular supply chains can break the link between resource consumption and revenue generation. Read More
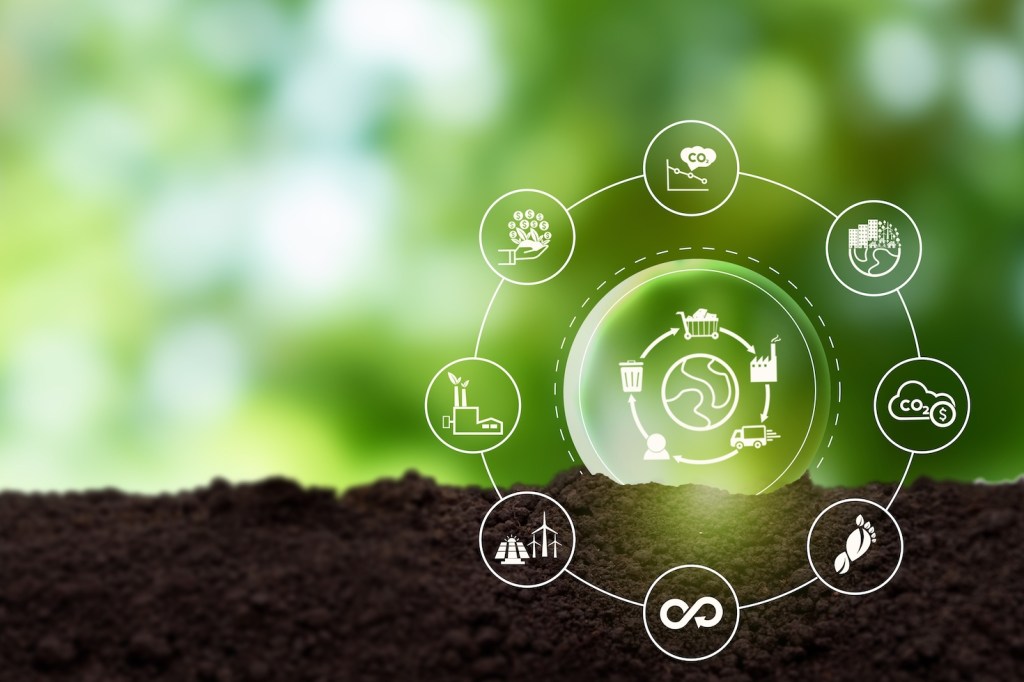
Source: Shutterstock/3rdtimeluckystudio
To say supply chains are complex is an understatement. Rarely do we make products out of just one raw material or in just one place. Every product is the sum of its parts. Even something as simple as a cotton T-shirt takes many steps along its journey. From production to shipping to sales to consumer use and end of life — current supply chains are fundamentally linear.
But there’s an alternative journey the humble T-shirt — or virtually any product, for that matter — can travel along. And it’s not linear. It’s circular.
Supply chains are often overlooked in discussions about the circular economy, overshadowed by business models or product design. But behind the scenes, supply chain professionals are responsible for the sourcing, movement and transformation of the 100 billion metric tons of materials that enter the global economy every year.
In many businesses, supply chain leaders are spearheading the search for resilience. Global shocks, from COVID-19 to extreme weather events, are exposing the vulnerabilities of existing supply chains. As finite materials become scarcer and their prices more volatile, companies can expect to lose almost half a year’s profit to supply chain disruptions over the next decade if they continue along this linear path. At the same time, Scope 3 emissions can be more than 80 percent of all greenhouse gas (GHG) emissions for a typical consumer goods company.
Circular supply chains can be leveraged to break the link between resource consumption and revenue generation. In doing so, businesses can increase material security and availability, reduce exposure to price volatility, meet climate and nature goals, and gain sought-after long-term resilience.
Building circular supply chains is no easy task, and it’s hard to know where to start. We’ve identified nine target areas where you can exert the greatest impact for the biggest gain.
1. People and structure
Transforming how a system works is a job in itself. It’s difficult to find the time and gain the knowledge required to implement circular processes and technologies. But transformation is possible if it happens at an organizational level, as HP is doing.
The tech company is developing new organizational structures and adapting existing departments to ensure they’re well-placed to tackle the challenges arising from the transition. And to bridge the knowledge and skills gap, HP is training supply chain teams on circular economy principles.
2. Network design
Circular supply chains require reverse logistics to recover and reintroduce used products and materials. Setting up regional hubs to collect, sort and process products and materials can facilitate access to circular inputs, help combat potential issues around cross-border legislation and taxation, and reduce emissions.
CHEP, the world’s largest global pallet pooling company, has switched from the “One-Way Trip” approach to a “Managed Recovery” one to tackle network design challenges and reduce GHG emissions. In this system, the customer receives CHEP’s shared and reusable pallets; sorts them using CHEP quality standards; stores the pallets that pass the test; and returns the rest to CHEP for repair before reuse.
3. Supplier engagement
Suppliers are essential to ensuring the quality, availability and traceability of circular inputs. Engaging, supporting and incentivizing suppliers, and communicating expectations and documentation enhances the cost-effective circulation of products and materials and the adoption of circular economy practices.
Danone, for example, has established long-term contracts with dairy farmers to help alleviate short-term market volatility, allowing them to adopt practices that can support regenerative outcomes.
4. Data and quality
Leveraging technology, data and information flows is essential to circulating products and materials across the supply chain.
Germany-based Niaga helps manufacturing partners redesign and produce products such as carpets, mattresses and furniture panels. Previously, products were being wasted because of a lack of data on material compositions.
So Niaga developed a scannable marking, giving products a return route and a digital product passport. This provides ingredient transparency and information on the product’s carbon dioxide footprint, recycled content and recyclability.
5. Metrics and performance management
Measuring circular supply chains with the same metrics as those used for linear supply chains won’t accurately capture their positive impacts. Instead, departments must align on the performance indicators used to monitor, measure and drive success in a circular supply chain and incentivize the shift through employee bonuses.
CHEP created an Activity Based Costing (ABC) model to track circular flows and codify more than 30 related key performance indicators such as asset return rates and reverse logistics efficiency. The model provides data to benchmark circular performance, identify improvement areas and rapidly test solutions. Additionally, CHEP links organizational circular economy targets to employee bonuses to incentivize circular actions.
6. Business models and product design
To ensure the efficient flow of products and materials, the circular economy requires collaboration between both internal and external departments.
In Brazil, HP partnered with Sinctronics to create a reverse logistics ecosystem to recover value from end-of-use electronic equipment. Cross-company communication enables Sinctronics to share practical insights with HP, seeking to influence and enhance its design decisions and identify new opportunities for creating closed-loop processing.
7. Customer engagement
Getting customers onboard with these changes is fundamental to long-term success. To close the loop on a circular economy, we need consumers to return products and materials when they’re no longer needed. This requires engaging with customers beyond the point of sale, leveraging them as critical partners in the circular supply chain.
8. Financial resources
Change requires finance. But financing the circular economy transition necessitates a shift in mindset and measurement. New metrics that quantify circular inputs, measure the number of valuable outputs and assess the amount of time that products are in use will be needed to ensure circular supply chain activities — including non-financial considerations, such as biodiversity and carbon emissions — are appropriately assessed and timelines for expected returns are elongated.
9. Policy and legislation
Increasingly, legislation such as the EU’s Extended Producer Responsibility, is being developed to facilitate circular supply chains. But common standards, metrics and definitions are urgently needed to level the playing field. Businesses can advocate for these, giving policymakers the confidence to move further, faster.
Engaging with policymakers to inform legislation can also help scale circular supply chains. And alignment on cross-border policy could help remove barriers to the movement of circular inputs across regions.
To learn more about how to drive change across these nine areas in your supply chain, read the Ellen MacArthur Foundation’s white paper, “Building a circular supply chain: Achieving resilient operations with the circular economy.”
[CLARIFICATION (4/4/24): This article has been updated to more accurately describe CHEP’s Managed Recovery system.]
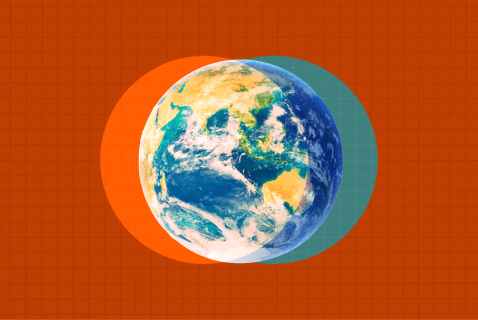