Dell cuts e-waste with recycled carbon fiber
Building on its closed-loop recycling, later this year the computer maker will recycle excess carbon fiber and scrap raw materials into new products. Read More
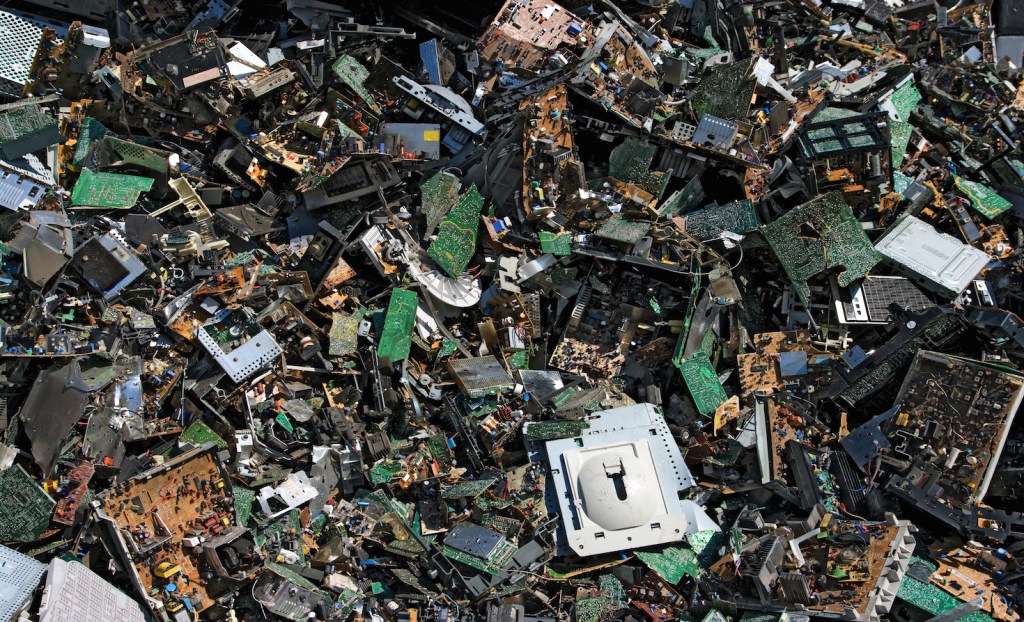
In the electronics industry, rapid technology innovation and ever-shortening product lifespans are contributing to staggering flows of e-waste.
In 2014, global e-waste amounted to nearly 42 million tons, according to a report by the United Nations University. That’s enough discarded televisions, computers, cellphones and other gadgets to equal the weight of 115 Empire State Buildings.
And the total amount of global e-waste could hit 50 million tons by 2017, the report warned.
All of this has profound negative environmental and human health impacts. Toxic chemicals accumulate in soil, water and food, and harmful fumes pollute the air.
In the global South — as I witnessed first hand on a trip to Nairobi last year — children in slums can be found chewing on circuit boards and wires from discarded electronics. The global South generates even more e-waste than wealthier regions of the world.
At the same time, around $55 billion worth of valuable materials embedded in this e-waste is being wasted, the U.N. report said.
The overall electronics industry has been slow to address the dual threat and opportunity that e-waste presents, but tech giant Dell is making some of the first inroads to a more “circular” supply chain. The company recently announced progress against its circular economy initiatives, including the expansion of its closed-loop recycled plastic supply chain and the introduction of reclaimed carbon fiber source materials into some of its products.
Making new computers from old
In 2013, as part of its 2020 Legacy of Good Plan, Dell established two objectives tied to cutting down on e-waste: using 50 million pounds of recycled materials and recovering 2 billion pounds of e-waste by 2020.
The company has made notable progress toward these goals — since 2013, it has incorporated into products more than 21 million pounds of recycled plastics from sources including water bottles and CD cases, and has recovered 1.2 billion pounds of e-waste.
But the company wanted to secure its own waste stream to free it from the volatile global plastics market, which can fluctuate depending on the price of oil and other mounting competition for recycled plastics.
That’s why in 2014, Dell launched its closed-loop recycled plastics supply chain, which has since recycled more than 4 million pounds of plastics into new products. Certified by UL Environment as the first closed-loop supply chain, the program entails collecting, recycling and using e-waste to make new Dell products.
“We have a long history of making recycling convenient and easy for our customers, recognizing that products do ultimately reach a point where the user goes and purchases a new one and doesn’t know what to do with the old one,” Scott O’Connell, director of Environmental Affairs at Dell, told GreenBiz.
To this end, Dell offers several takeback and recycling programs, O’Connell said. The company has recycling programs in 78 countries and offers asset recovery in 44.
One such initiative, Dell’s Reconnect Program, allows people to drop off any brand of used electronics to more than 2,000 Goodwill locations in the U.S. If the gadget can be refurbished, Goodwill sells it. If not, the end-of-life product is sent to Dell’s recycling partner, Wistron, for asset recovery in the U.S. Metals like tin, gold and tungsten are re-sold in the commodities market. Plastics are sorted and shipped to China, turned into pellets and mixed with virgin plastics for use in new Dell products.
Currently, these plastics are being used in more than 30 flat panel monitor models and three Dell OptiPlex desktops available globally.
“As those products with recycled content come back again years from now, we can continue to re-harvest those plastics and keep the circular economy flowing,” O’Connell said.
Recycled carbon fiber shrinks waste and emissions
Building on its closed-loop recycling operations, Dell earlier this month announced a partnership with supplier SABIC to recycle excess carbon fiber and scrap raw materials into new Dell products beginning in late 2015.
When the program first launches, certain Latitude and Alienware products will contain recycled carbon fiber, with plans to expand across these two product portfolios in 2016, O’Connell said.
The partnership with SABIC is expected to prevent some 820,000 pounds of carbon fiber from ending up in landfills by 2016. And the recycled carbon fiber materials have an 11 percent smaller carbon footprint than simply using virgin carbon fiber, Dell claims.
“This is another another aspect of us looking at opportunities to conserve waste and materials and put them back into use,” O’Connell said. “Carbon fiber is one of these types of plastics you’re seeing more use of in different industries because of its strength and light properties.”
Challenges to the circular supply chain
Transitioning from a “take-make-dispose” linear supply chain to a circular one can be, well, dizzying. Dell has had to overcome two chief challenges in making the move, O’Connell said.
One challenge was getting the engineering right.
“When dealing with plastics, getting the properties equivalent or better to virgin materials isn’t easy,” O’Connell said. “But this is a challenge we’ve been able to overcome with engineering know-how.”
Another challenge pertains to establishing a reliable closed-loop supply chain.
“We had to make sure that we had sufficient volume of product coming in to be able to yield enough plastics to put into a mainstream Dell product,” O’Connell said.
Dell manufactures these products on a global scale, which required a lot of upfront work to make sure the supply chain could remain viable.
The end of ‘waste’
Given the current dominance of the linear economy, it might sound radical to claim that waste should not merely be limited, but eliminated as a concept altogether.
But it’s also logical, considering that we can’t sustain limitless consumption on a finite planet. Over time, landfills will overflow and it will become increasingly difficult and expensive for businesses to source virgin materials.
The virtues of a “circular” economy — defined by WRAP as “an alternative to a traditional linear economy in which we keep resources in use for as long as possible, extract the maximum value from them whilst in use, then recover and regenerate products and materials at the end of each service life” — speak for themselves.
It can reduce waste, drive greater resource productivity, avert negative environmental impacts and better address the current and future resource security and scarcity issues.
For now, Dell is leading the charge toward a more circular electronics industry. Stay tuned to see if others will follow.
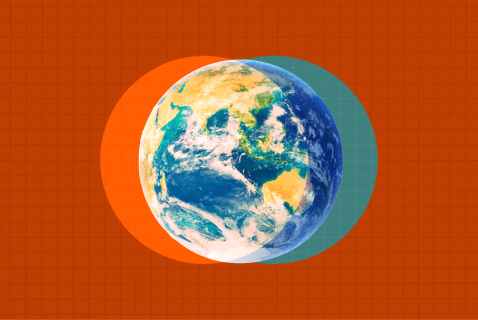