EV battery recycling is building a circular economy from scratch
Billions of dollars are sweetening early efforts by electric vehicle battery recyclers. But swings in materials prices and policy shortcomings complicate the long-term picture. Read More
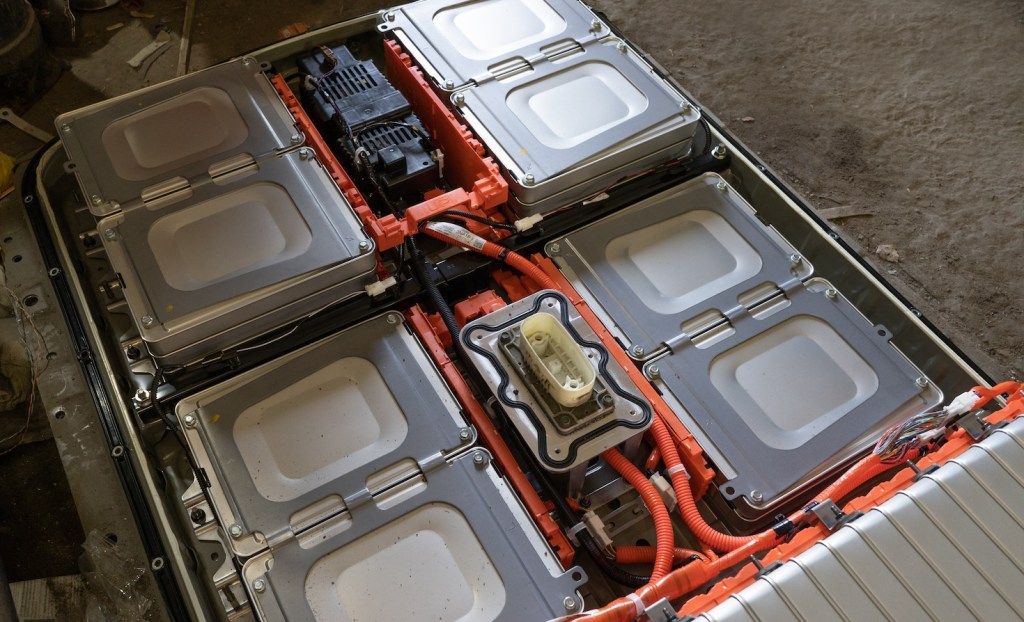
Advocates of a circular economy for electric vehicle batteries hope to see resilient supply chains, new jobs and emissions reductions emerge in the United States. That’s because the EV market is still nascent, with not enough sales so far to require mass recycling, allowing for a circular economy to be built from scratch.
“What I do love about the whole EV battery recycling conversation: how often do we start a conversation in corporate America with, ‘How are we gonna recycle this thing?’” said Brandon Tracy, a former energy and mineral policy analyst with the Congressional Research Service. “It’s a beautiful realization that we’ve screwed up in the past, not starting at the lifecycle and saying, ‘What are we gonna do here?’”
Funding for new EV battery recycling efforts is already white hot. So is the hype about a new “gold rush” for black mass. That’s the muddy sludge of lithium, cobalt, nickel and other critical minerals that lithium-ion battery recycling plants produce.
The Biden administration is offering many business incentives to offset China’s dominance in EV-related mining and manufacturing.
Scores of U.S. battery recycling plants are preparing for an anticipated flood of EV batteries as they peter out later this decade in some of the early model Nissan Leafs and Chevy Volts. The lifespan of an EV battery is anywhere from a decade to 20 years.
For now, recyclers are mostly handling production scrap from batteries alongside old smartphones and other consumer electronics.
The U.S. Department of Energy (DOE) on Sept. 20 announced $3 billion for battery recyclers and component makers that it says will create 12,000 jobs. “By positioning the U.S. at the forefront of advanced battery manufacturing, we are creating high-paying jobs and strengthening our global economic leadership and domestic energy security, all while supporting the clean energy transition,” U.S. Secretary of Energy Jennifer Granholm said in a press statement.
Private funding is also stimulating “urban mining” to extract critical minerals from used batteries instead of the earth.
Understand Double Materiality to Reduce Risk and Identify Opportunity

Among the bullish expectations:
- U.S. factories will be able to crank out enough batteries for the equivalent of 10 million EVs by 2028, according to the Environmental Defense Fund.
- The capacity of the anticipated recycling plants could process enough batteries retiring from passenger cars up to 2044, according to the International Council on Clean Transportation (ICCT).
- The existing and planned facilities would be sufficient to handle about 1.3 million end-of-life electric car batteries each year by 2030 — but only 341,000 retired batteries will be available by then, according to ABI Research.
This new economy is just warming up. “There’s a huge difference between what is announced and what will be materialized,” said Georg Bieker, a senior researcher at the International Council on Clean Transportation of Washington, D.C.
“We’re in kind of a rare moment here, where we can actually build this right from the start,” said Laura LoSciuto, who leads the Battery Circular Economy Initiative at the Rocky Mountain Institute (RMI). The effort seeks to prevent the waste, pollution and social problems that legacy transportation and manufacturing have wrought.
Sweet carrots, no stick
Despite many policy “carrots,” the U.S. wields no “stick” for companies to keep batteries out of landfills.
- Out of its $1.2 trillion for energy and transportation, the Bipartisan Infrastructure Law offers $7 billion to develop domestic battery supply chains.
- For consumers to get a clean energy tax credit of $3,750 on an EV purchase, the Inflation Reduction Act of 2022 requires the battery’s critical minerals to have been either “extracted or processed” in the U.S. or by a free trade partner, or recycled in North America. An additional $3,750 tax credit relates to battery components.
- Also on the federal level, if it became law, the TRACE Act would establish, but not require, digital IDs for battery materials.
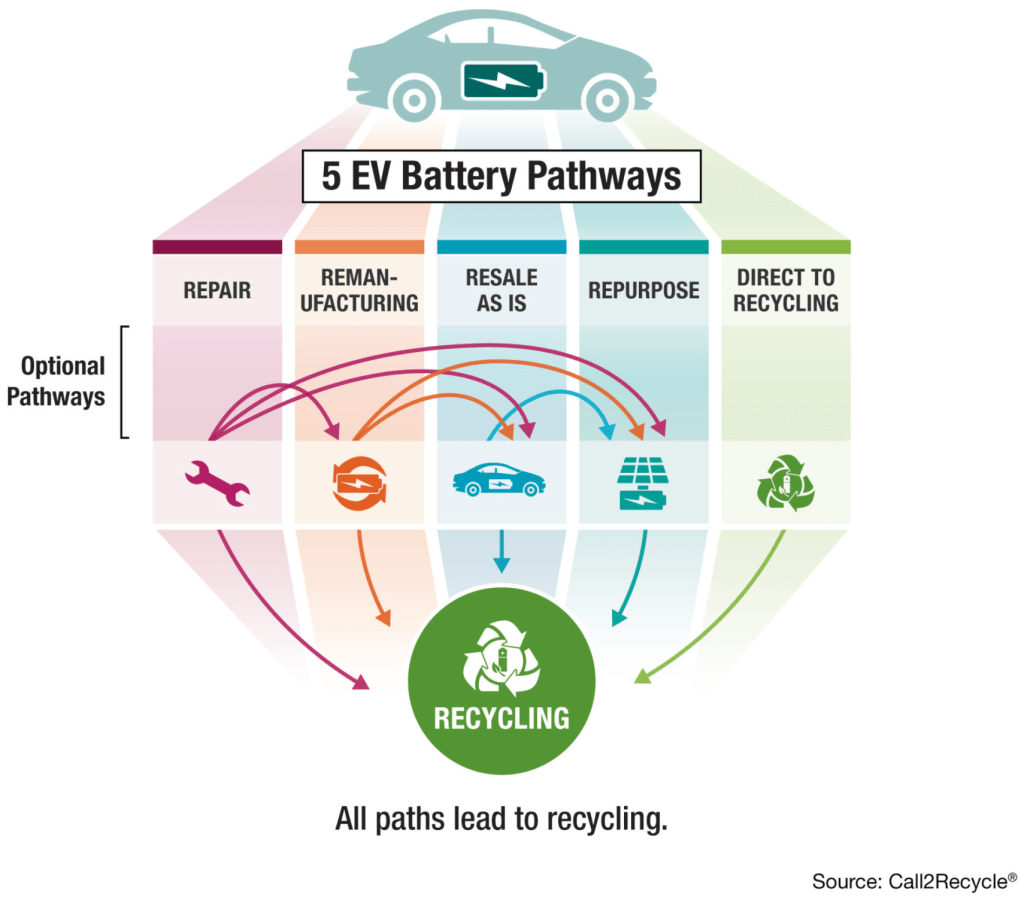
By contrast, the European Union’s extended producer responsibility (EPR) rules require battery makers to manage collection and recycling.
“A lot of automakers in the U.S. also operate within the EU, so they are having to meet these standards for at least part of their sales,” said Jessica Dunn, senior transportation analyst at the Union of Concerned Scientists.
“How do we create a market that’s working in harmony, even within the U.S.?” Battery Circular Economy Initiative’s LoSciuto said. “We don’t want a patchwork of 50 different state regulations and 50 different state systems.”
There’s so little state activity, however, that only one “patch” is filled in:
- In January, New Jersey became the first state with an extended producer responsibility law. It demands that battery makers have a plan for recycling.
- California Gov. Gavin Newsom vetoed a bill Oct. 1 that would have forced automakers to recycle EV batteries. A new version is expected to emerge.
In the U.S., battery recyclers are left to weather the ups and downs of commodity prices. Lithium is inexpensive lately and its mining may rise domestically, but cobalt, primarily exported, is relatively costly. There have been murmurs of a government price floor on critical minerals to help U.S. competition.
And while lithium-ion batteries dominate today, there’s no guarantee they won’t eventually fall out of fashion, forcing recyclers to retool.
It will take decades for this ecosystem to sharpen into focus, and then it will evolve further, experts say.
Big government grants
For now, these are boom times for battery plant builders. A “Battery Belt” is forming in Great Lakes states and the South. Lithium-rich Nevada is another hub, with recycler and refiner Redwood Materials in Carson City and a Tesla gigafactory outside Reno.
The DOE’s 25 latest grant beneficiaries across 14 states include Cirba Solutions of South Carolina, receiving $200 million. The recycler shreds batteries and sells mineral-rich black mass to refiners, processors and battery makers. Some recyclers do refining and processing as well. Ascend Elements of Massachusetts, for example, makes battery cathode active material from black mass it produces. It’s sharing $125 million from the DOE with Orbia Advance Corporation of Mexico City.
Established giants in mining and chemicals received Energy Department infusions in September, too.
Players are building partnerships to connect within and across regional hubs.
On Sept. 19, BMW Group teamed up with Redwood Materials to recycle all its U.S. vehicle batteries. Redwood also has partnerships with Ford, Volvo, Volkswagen, Toyota and Rivian. The startup has raised $2 billion plud a $2 billion DOE loan for its closed-loop bid to handle the entire battery lifecycle.
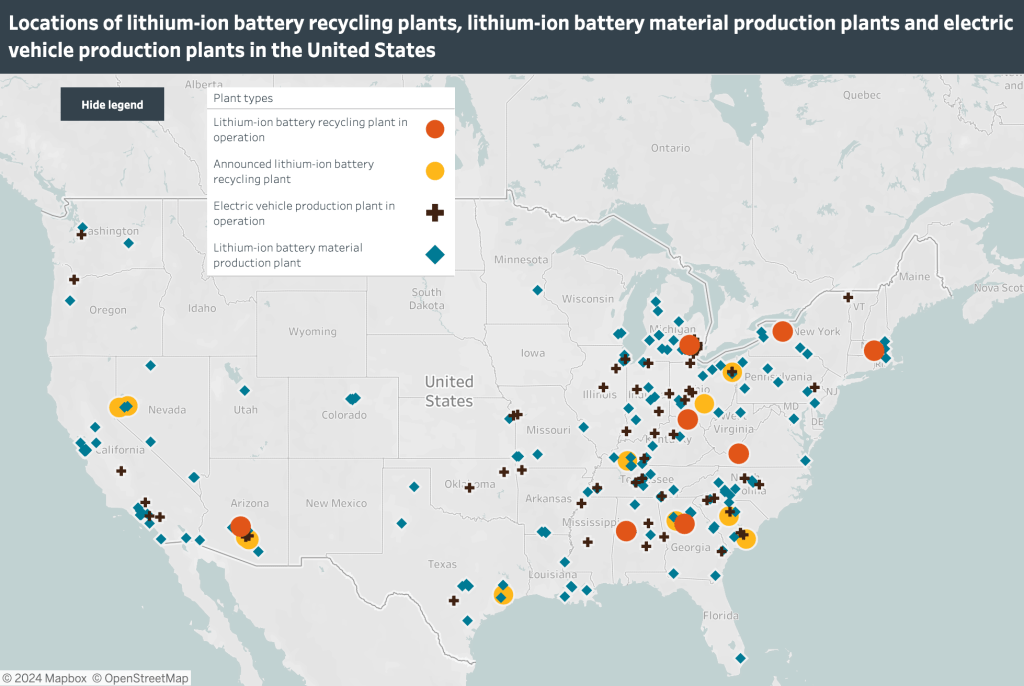
The business case
Environmental groups want to close the loop on materials and advance decarbonization. Social justice advocates want on-shoring to close opportunity gaps and prevent industrial hazards. Businesses, of course, want to make a buck.
Private investors are pouring hundreds of millions into battery-related startups with circular economy propositions. Following a previous $480 million from two DOE grants in 2022, Ascend Elements has closed $650 million in Series D financing this year.
“It’s quite a bit of capital to deploy, and we need every dollar of it,” said Roger Lin, Ascend Elements’ vice president of government affairs.
The company is laying the pipes for a million-square-foot facility in Hopkinsville, Kentucky. It is scheduled, starting in mid-2025, to pump out enough cathode materials from recycled batteries to supply 750,000 battery packs each year.
Meanwhile, industry alliances are publicly embracing circularity for EV batteries. Since it emerged from the World Economic Forum in 2017, the Brussels-based Global Battery Alliance has engaged Tesla, Volkswagen, Volvo Group and 167 other organizations.
“Supply chain concerns are certainly top of mind for auto manufacturers and their suppliers,” said Dan Bowerson, vice president of energy and environment at automaker trade group the Alliance for Automotive Innovation, in May at the Trellis Circularity 24 event in Chicago.
Recycled battery materials have a carbon footprint four times smaller than that of traditionally mined ones, according to McKinsey & Company research. In addition:
- Regional supply chains for battery minerals slash the 50,000 miles they travel on average from a mine into a battery, according to RMI.
- Retired EV batteries could provide 60 percent of cobalt, 53 percent of lithium and 53 percent of nickel globally for new vehicle batteries by 2040, according to a 2021 study by the American Chemical Society.
- By 2040, annual battery recovery and recycling revenues could reach $95 billion worldwide, according to McKinsey & Company. In addition, each ton of battery material could yield $600 in value by 2025.
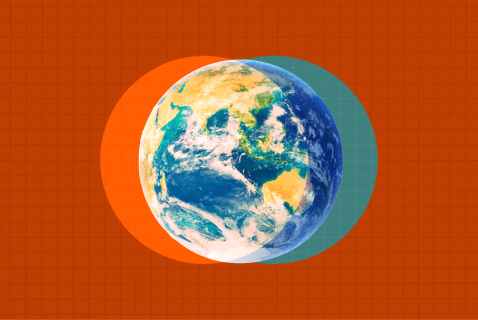