Extended Producer Responsibility and the E-Waste Problem
A growing number of companies are taking on greater levels of responsibility for the environmental impacts of their products -- from point of manufacturing through to end of the life recycling. E-waste recycling is taking off, but obstacles remain to its widespread practice in North America. Read More
A growing number of companies are taking on greater levels of responsibility for the environmental impacts of their products — from point of manufacturing through to end of the life recycling. E-waste recycling is taking off, but obstacles remain to its widespread practice in North America.
The practice of Extended Producer Responsibility (EPR) is picking up steam, most notably in the information technology industry. A growing number of companies are taking on greater levels of responsibility for the environmental impacts of their products — from point of manufacturing through to end of the life recycling. E-waste recycling is taking off, but obstacles remain to its widespread practice in North America.
The E-Waste Problem
Personal electronics and information technology companies are driven by the powerful incentive of market demand to produce newer consumer products and newer equipment , which in turn has made e-waste the fastest growing category of waste in many countries.
It is estimated that in the US alone as many as 40 million personal computers become obsolete every year. But PCs are just one product. If all sources of e-waste are considered, the total global amount could be as high as 50 million tons a year, according to the U.N.
Less than 20 percent of the e-waste in markets is marked for recycling; the rest ends up in landfills (including dumping sites in developing world nations where environmental controls may be less stringent), or left in storage. Of the goods that do make it to the recycling process, 80 percent get shipped to developing countries such as China, India and several in Africa, where much of the waste is scavenged by the poor who make a living by extracting valuable metals and components for cash.
The environmental problems resulting from e-waste disposal are three fold. First, e-waste takes up a significant amount of space in already crowded landfills and persists for centuries. Second, simply discarding e-waste is a tremendous waste of resources that can be reused.
Finally, discarded computers, mobile phones, routers and other equipment contain numerous toxic materials such as lead, mercury, cadmium, chromium, brominated flame retardants and polychlorinated biphenyls — to name a few. These materials can impact the health of both developed and developing populations.
Emergence of E-Waste Recycling
Aside from the environmental and health benefits of diverting consumer electronics from waste streams, the potential business benefits of EPR are significant. A growing number of companies are beginning to realize the benefits of fostering stronger bonds with their increasingly environmentally-conscious customers, as well as reducing manufacturing and waste management costs.
PC maker Dell promotes refurbishing and reusing its products as an alternative to recycling them. The benefits are twofold: the lifecycle of refurbished products is longer, and the day that Dell must manage the collection, sorting and recycling of them at their end of life, is pushed out. Dell also forged a partnership with Goodwill to collect and either resell or recycle used machines.
Sony and other producers also offer consumers credit toward a new purchase if they return a used product to the company. Douglas Smith says Sony’s approach to recycling consumer product is focused on cultivating internal benefits and was grown from its existing practice of recycling the waste product it collected during manufacturing. He says Sony was also a leader in using a glass-to-lead smelting process in order to recycle glass used in CRT televisions, as well as launching a program for recycling nickel cadmium batteries.
“For consumers, we want to make recycling our products as easy as buying them,” says Sony’s Smith.
Hewlett-Packard began recycling its LaserJet print cartridges in 1991 and its inkjet print cartridges in 1997. Consumers return the cartridges via post, using labels printed from the HP web site. HP announced in late January, 2008 that it has developed a manufacturing process that turn used cartridges into new ones. HP used more than 5 million pounds of recycled plastic in its inkjet cartridges in 2007, and is committed to using twice as much in 2008.
E-waste recycling isn’t limited to electronics companies. A growing number of businesses are being developed around e-waste and some are even incorporating into their sustainability strategy, such as mining company, Teck Cominco.
Teck Cominco launched its e-waste program in 2006. The Vancouver based mining company now accepts old computer which it incinerates, using state of the art, clean technology. After incineration, the company gathers any precious metals that may have been contained.
Alternatives to E-Waste Recycling
According to John Dickerson, vice president of business development for AER Worldwide, an international recycler of electronics, recycling consumer electronics recycling is still a net cost for many companies because the volume of goods being recycled is still low.
Dickerson says the costs associated with recycling consumer electronics break out to three main categories.
The first and most expensive cost involves developing systems for collecting goods to be recycled; then the costs of deconstruction of the products, in which components such as circuit boards and plastic covers are removed and stockpiled. The third cost is destruction; the removal of all traces of a brand name or logo from these components.
The purpose of EPR is to stimulate better waste management, product design and marketing systems by shifting the cost of waste back onto those with control over product design. Therefore e-waste recycling isn’t the only path to achieving a high level of EPR and less expensive alternatives do exist. According to IBM, companies can still take product responsibility by:
- Developing products that can be upgraded to extend product life;
- Develop products that can be reused or disposed of safely at the end of product life;
- Develop and manufacture products that use recycled materials where technically and economically justifiable;
- Develop products that provide improvements in energy efficiency;
- Develop products that minimize resource use and environmental impacts through the use of environmentally preferred materials and finishes;
- Re-use factory waste for new products; and
- Use less packaging, or recyclable packaging.
“We are all trying to design products that are easier to recycle, and we are reducing the number of grades of plastic that are in the products, to make the plastic more of a commodity,” says David Thompson, director of the corporate environmental department for Panasonic America, because it could not garner the participation of enough host communities or recyclers.
State of EPR in North America
In North America, the challenges of funding, developing and ingraining EPR into a corporate structure are daunting. The absence of adequate legislation may be the largest roadblock to more widespread adoption of the concept. Legislation only exists in a handful states and according to Dickerson, is patchy and inconsistent from region to region.
Canada has a voluntary packaging law which was developed 18 years ago and several provinces have “take back” programs not only for paint, beverage containers, tires, old or unused medications, toxic household products among others.
When compared to the European model, these measures are simply not strong enough to significantly reduce e-waste or encourage widespread adoption of EPR principles.
In Europe, where legislation has already been established, e-waste recycling is more commonplace. The waste electronic and electrical equipment (WEEE) directive was passed in 2006 to force manufacturers of electronics to mitigate these risks by taking back and recycling used product in order to divert it from landfills, illegal dumps and unsafe disassembly practices.
Thus far, WEEE appears to be working. London’s Environment Agency completed a study that shows landfills in England and Wales in 2006 received 60 percent less hazardous waste than in 2004, while recycling and re-use increased 64 percent over 2004, according to E-Scrap News.
According to Sims Group chief executive Jeremy Sutcliffe, following the WEEE model may be the key to widespread adoption of EPR in North America and Australia.
“Our existing and newly acquired knowledge in the important areas of WEEE goods recycling and asset management will be critical in assisting governments and manufacturers in Australia and North America to introduce appropriate legislation and solutions for the ever-increasing problem of ‘end of life’ electronic and electrical manufactured goods.” Said Sutcliffe.
According to Dickerson, if more legislation requiring producer responsibility comes into effect than volumes of e-waste recycling should increase and associated costs should go down, making financial payback to producers possible and EPR a more common practice in North America.
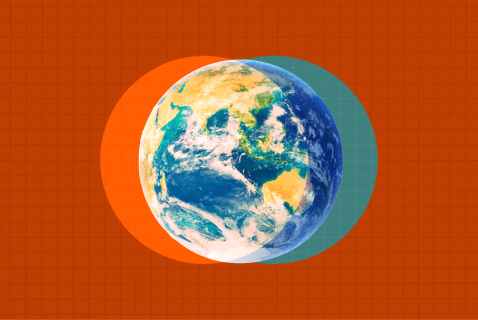