Four Greenhouses that Point to the Future of Urban Building
The world has come a long way from some of the hippie dreams of the 1970s, although the far-out ideas for creating sustainable spaces to live and work in are rapidly becoming reality. Read More
This summer I was lucky enough to teach courses in bio-inspired design at Schumacher College in Devon, England, and the Omega Institute in Rhinebeck, New York. At both institutions I saw what I think is the future of urban building, although it will not, I am quite sure, look anything like what I observed and discussed at these quiet, idyllic places.
This future will have, I believe, a large element of the past within it. Green ideas that were the stuff of hippie dreams 40 years ago have been given two gifts from Father Time: new relevance in the centers of capital, thanks to the urgency of climate change, and new feasibility in the centers of design, thanks to our advances in technology and industry.
The humble greenhouse appears to represent some of these trends, and why not? It is a building meant to support life in a context broader than a single, human species.
1. The Omega Center’s Eco-Machine
Take, for example, the Omega Center for Sustainable Living (OCSL). This is the first building in the United States to meet both the Living Building Challenge criteria and U.S. Green Building Council LEED Platinum standards. The 6,250 square foot building is a zero-net energy building, and actually feeds energy back into the grid over the course of a year. Solar panel arrays and a geothermal heat exchange system make this possible for a building that is used as a classroom during the milder times of the year.
The building and its constructed wetlands and dispersal fields process all the wastewater from the 195 acre Omega campus and return it to the local aquifer. No chemicals are used to treat the waste; plants and a special recipe of fungi, algae and bacteria in the soil and in tanks do the work.
This so-called Eco-Machine, designed by John Todd Ecological Design, brings blackwater to potable levels in seven sequential steps over the course of 36 hours. These stations include a beautiful 4500 square foot greenhouse full of flowering tropical plants growing in tanks. Most of the water flow is gravity powered. Any energy used is supplied by solar power. The plant processes as much as 38,000 gallons per day and has a design capacity of 52,000 gallons per day.
It has been a long journey from the days of John Todd’s New Alchemy Institute in Falmouth, Massachusetts in the 1970’s, but the OCSL is a very gratifying sight indeed.
So why do I think this small wastewater treatment plant masquerading as a beautiful building (by BNIM Architects of Kansas City, Missouri) heralds future trends in urban construction?
First: Closed loops. The loop that the OCSL closes is the hydrological cycle. Omega takes water from the local aquifer, borrows it for toilets, sinks and showers and then cleans it back up before returning it to its natural, underground holding tank. If we are to save our resources and energy, we will have to close all of these material cycles or loops.
Second: Making buildings work harder. In the future they will have to multi-task like the rest of us and go beyond shelter and interior climate control. They will actually have to improve conditions around them, including things like providing more oxygen, or storing heat, or educating people. The OCSL design only hints at some of this, but I believe that such enhanced functionality will be in this future and will be integrated increasingly into building design.
Third: the building / nature interface. If we are to close natural material cycles and solve challenges beyond the walls of individual buildings, as I believe we must, then we must inevitably come to this third trend: truly integrating the built environment into existing natural systems.
We can’t afford not to take advantage of the free services that these systems provide, and can’t afford, any longer, to screw them up.
Next page: Bringing greenhouse principles to greening the Sahara
This integration will mean that our buildings will have to increasingly start functioning like natural things, rather than awkwardly embedded objects. If you need to filter water out of the soil using your building’s foundation, say, then I would bet that your design sketches will start looking like membranes and you will be talking to a biologist as well as a soils engineer.
At OCSL the working guts of the treatment plant are literally spread all over the ground, and the sophistication of joining a building with the land will only become more refined as we progress from bio-utilization to bio-inspired design.
2. Schumacher College: Applying Greenhouse Principles to the Sahara
At Schumacher College I had the privilege of speaking with fellow teacher Michael Pawlyn, architect, head of Exploration Architecture and an advocate of a biomimetic approach to restorative design. He is an advocate of what he calls the “radical resource efficiency” that can often be achieved by transforming our current linear resource streams into closed loop systems. He further believes that our current fossil fuel system will have to change to one directly based on the sun (see his TEDSalon London 2010 talk for more).
Pawlyn is the conceiver of the Sahara Forest Project. The Sahara Project takes the functionality of the greenhouse and gives it the audacious ambition of restoring an entire region. Seawater will be pumped through greenhouse buildings to desalinate the water. This freshwater will then be used to grow food crops or seedlings for desert revegetation within the protection of the greenhouse.
Simultaneously, newly desalinated water will be converted to steam in giant boilers by concentrated solar arrays and used to spin turbines for energy. The solar arrays will be used to shade plants that would not ordinarily survive in the harsh sun, and the waste heat will be used in the distillation process.
Carbon neutral energy, fresh food and water, and a new ecosystem grown in one of the harshest environments in the world: this is a good example of closing material loops and making our buildings work harder, even beyond their own walls. One of the design team’s revelations came when they realized that the first prototype seawater greenhouse, by changing the ambient humidity and discharging excess water, had transformed the desert landscape around it, “like a green inkblot,” according to Pawlyn.
Jordan has recently announced its support for the project, and will provide a 200,000 square meter plot in Aqaba near the Red Sea, with an additional 2 million square meters for future expansion. The project is backed by the Ballona Foundation and Norwegian authorities. The developers will conduct a feasibility study in 2011, and plan to build a pilot test and demonstration center in 2012, which will be scaled up to production levels by 2015.
The Seawater Greenhouse is the brainchild of team member Charlie Paton, and is an elegantly simple design that turns a building into a giant still. Water is let through the space, evaporated in grills and then condensed and collected. In the process it leaves its previously dissolved minerals behind. The freshwater is now where it is needed and is piped immediately to the waiting plants. The plants are then used to leverage soil conservation and microclimate engineering and, it is hoped, these small steps will add up to a change in a regional ecosystem.
Next page: The Eden Project, the Biggest of them All
Here, the building is clearly working to solve challenges beyond its walls. As to those minerals, in this brave new world of closed loops no resources get truly left behind: plans include the use of the calcium carbonate and salts for building blocks and the phosphates for fertilizer. Indeed, an entire spectrum of minerals is in seawater, so the designers will continue to study precipitation rates and recovery methods.
3. The Eden Project: The Largest of Them All
While at Schumacher I visited another, now famous, greenhouse at the Eden Project in Cornwall. One of the most-visited sites in England, this former chinaclay quarry contains the world’s largest greenhouse, one of two that shelter tropical and Mediterranean plant communities.
Pawlyn was also involved in the design of these buildings in the firm Nicholas Grimshaw and credits the natural world for much of the design inspiration; soap bubbles for a shifting shape at the foundation and radiolarians for efficient tessellation, for example. The buildings, therefore, edge slightly closer to that building/nature interface, but perhaps only in form.
These domes are covered with ETFE (ethylene tetrafluoraethylene) which has been made into a three-layer sandwich with air blown between. ETFE is 1% the weight of glass, and this efficiency created a cascade of savings on steel and other members such that engineers calculated that the roof weighed less than the air it contained.
My colleague at the California College of the Arts, Jay Baldwin, was the backyard inventor of the first “pillow dome” in the 1969, and yes, we have come a long way from those pioneering days of clamping vinyl bags onto tube-framed geodesic domes.
While these three greenhouse designs work harder and close material loops successfully, the world awaits the progeny that will integrate their qualities with living and working spaces for humans. It also awaits a functional material integration of the built and the living worlds.
4. U.C. Berkeley: Making Plants the Mechanical Sensors of a System
A view of that frontier is in my backyard at U.C. Berkeley, and can be found in a nondescript and traditional research greenhouse and lab of the Department of Plant and Microbial Biology.
Here Professor Lewis Feldman is working with Professor Kameshwar Poolla and graduate student George Hines of the Department of Mechanical Engineering to bridge the gap between the environmental conditions in the greenhouse and the mechanical controls regulating the greenhouse environment.
Call it a partnership, if you will; the idea is to make the plants the sensors that fine-tune the mechanical system that supports them. Current arrangements might rely on soil moisture, or regular schedules, or other indicators of heat, light and air, but they are all somewhat removed from the critical indicator, real-time stress, as it is experienced by the plant.
The researchers have grown flats of a genetically engineered mustard, Arabidopsis, and subjected them to heat stress in order to test how well the plants themselves might be used as sensors, or bioreporters, of their specific environmental conditions. For this effort plants have been “engineered” to produce a protein that fluoresces when the plant is exposed to stressful temperatures.
A leaf of each plant is attached to a meter that measures the fluorescence emitted from fluorescing protein in the plant. This protein is produced in the plant when the gene encoding this protein is joined to a promoter.
Promoters are the molecular “on/off switch” of genes, and different promoters turn on (or off) depending upon their exposure to particular environmental conditions. The activity of the genes, therefore, makes a great indicator of the state of stress in a plant. Once useful promoters are identified they are joined to the gene which makes the protein that fluoresces and then this new gene is inserted into the test plants. These plants are then grown through several generations to confirm a reliable genotype and then used in the testing.
Results have been promising and the researchers will now turn their attention to developing a superior indicator, and identifying a range of promoters for stresses other than heat. In more engineering terms, they will try to develop sensors for every state of interest to the building system.
The long-term implications are significant for crop yields specifically, and for designing living buildings in general. As the researchers write, knowing the genetic pathways that control a plant’s flowering time would allow the control of stress-promoter expression levels that correspond to optimal yields. This knowledge would further allow the use of the plant itself to set those conditions in the building.
The highest-level goal of the project is “…closing the loop around the greenhouse environmental setpoints through observation of biological processes, in order to optimize the grower’s objective.” Substitute the word “designer” for “grower” and you will see my point.
Designers: get to work!
Top photo, of the Eden Project domes at night, CC-licensed by Mark Vallins.
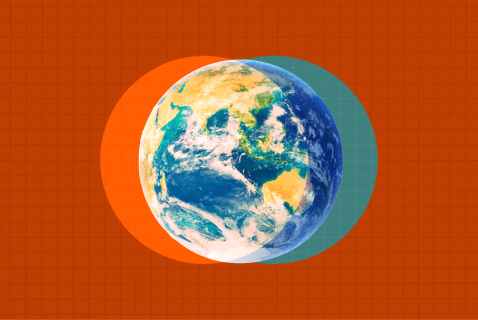