Foxconn Suicides Lead to Scrutiny of Supply Chain Management at Tech Firms
The company, a contract manufacturer for a number of electronics companies including Apple and HP, faces questions about its labor practices in the aftermath of suicides by workers. Read More
Since January, at least ten employees of Foxconn, the giant contract electronics manufacturer whose facility in Longhua, China employs some 300,000 workers, have committed suicide, most of them by jumping from the roof of the four-story dormitories in which they lived. Foxconn manufactures products for such U.S.-based computer companies as HP, Dell, and Apple.
Statistically, the number of suicides at Foxconn is not unusual for young people in China, although the frequency of suicides this year is alarming. An estimated 90 percent of Foxconn’s workers, who typically work 12-hour shifts and share living quarters with up to ten co-workers, are between 18 and 24 years old.
Of course, the precise causes of the suicides of Foxconn’s workers are unknown. As Dan Viederman, Executive Director of Verite, a U.S.-based non-governmental organization (NGO), told SocialFunds.com, “It would be inappropriate at this point to blame the suicides solely on working conditions.”
Verite conducts workplace audits to ensure that people worldwide work under safe, fair, and legal working conditions. In China since 1998, Verite also trains the staff of multinationals on how to improve working conditions, trains workers on their rights and responsibilities, and links with Chinese NGOs to help them build their capacity, according to Viederman.
Viederman continued, “When we talk about working conditions in China, it’s hard to generalize, which is why we focus on advocating that all businesses in China take the approach of knowing what the workers in their companies face.”
“There is a need throughout China for businesses and governments to more effectively understand the struggles and challenges that are affecting workers, and to take steps to allow those workers a greater voice in advocating for themselves and responding to conditions that they face,” he added.
Uncertainty regarding the precise reasons for the suicides at Foxconn, however, has not kept the company from coming under scrutiny for its labor practices. Last month, nine Chinese social scientists published an open letter to Foxconn which stated that the deaths “force us to question the future of the ‘factory of the world’ and the new generation of migrant workers.”
In addition, Students & Scholars Against Cooperate Misbehavior (SACOM) staged a protest last month at Foxconn’s headquarters in Hong Kong. Noting that Foxconn produces iPhones for Apple, SACOM announced that it will hold a Global Day of Remembrance for Victims of Foxconn on June 8, the date on which Apple is scheduled to launch its 4th generation of iPhones.
Responding to the suicides at Foxconn, Steve Jobs, Apple’s CEO, said at the D: All Things Digital conference this week, “We are on top of this. We look at everything at these companies. I can tell you a few things that we know. And we are all over this. Foxconn is not a sweatshop.”
Stating that the suicide rate at Foxconn “is under what the U.S. rate is, but it’s still troubling,” Jobs continued, “We’re over there trying to understand this. It’s a difficult situation.”
Also coming under scrutiny in the aftermath of the suicides are the supply chain management practices of the major U.S.-based electronics companies that contract with Foxconn to manufacture their products. As Meggin Thwing Eastman stated in a RiskMetrics blog post, “No one knows why these problems are coming to a head right now. But that doesn’t mean that these tragedies were entirely unpredictable. The historical record shows that some of the world’s most admired companies have effectively built poor labor practices into their business models. Now external pressure may force a change.”
The blog post referred to RiskMetrics’ evaluation of Foxconn’s environmental, social, and governance (ESG) performance, and noted that the company profiles of Foxconn customers “also flag the firm’s ongoing working-conditions problems. Among other issues, workers reported working 10-12 hours every day with only four scheduled days off per month, and many only got one.”
According to RiskMetrics, of the 23 electronic component manufacturers in the Electronic Equipment and Instruments sector, Foxconn scored the lowest.
SocialFunds.com spoke with Eastman, RiskMetrics’ lead ESG researcher for communications and technology, about the supply chain practices of Apple and other electronics companies.
“If you make something that’s really specialized, it’s difficult to turn over the manufacturing process quickly,” Eastman said. “The computer companies are hamstrung, and have to work together on this.”
On the RiskMetrics blog, Eastman stated, “Even if Apple wanted to purchase iPhones from some other firm, there’s no way to shift production without a huge interruption in the flow of finished products. In a market that churns as fast as consumer electronics, this is simply not an option.”
“And so massive integrated suppliers may have the upper hand in their bargaining with brand-name original equipment manufacturing (OEM) companies,” she continued. “Even OEMs with extensive supply chain labor rights programs can’t necessarily demand improvements in working conditions.”
Eastman told SocialFunds.com, “HP is probably best at responding when a problem presents. But it’s not a perfect system. Apple has policies in place and does decent reporting on supply chain compliance, but it often falls short on execution.”
Eastman referred to protests last year at a factory owned by Wintek, where iPad screens are produced for Apple. More than 60 workers were hospitalized after exposure to n-hexane, a chemical used for cleaning display screens, and at least one worker died.
“There were massive employee protests over working conditions after many people got sick,” Eastman said, “But protestors had raised the issue with Apple many months earlier. There wasn’t much response from Apple until after the public protests, and even then not as much as you’d expect.”
“Apple did not respond to questions from reporters on the issue,” Eastman continued. “The company often refers to its supplier code of conduct, and leaves it there.”
Noting that the Electronic Industry Citizenship Coalition (EICC), which was formed in 2004 to improve social, economic, and environmental conditions in the global electronics supply chain, has started to look into the Foxconn situation, Eastman said, “It’s interesting because Foxconn is a member, and is bound to implement the EICC code.”
The EICC’s Electronic Industry Code of Conduct seeks to implement a single supply chain social responsibility code of conduct in the electronic sector supply chain.
While calling for caution in coming to conclusions about the causes of the worker suicides at Foxconn, Viederman of Verite said, “To the extent that it forces us to step back and take a look at how we are interacting with vulnerable people in Chinese supply chains, then we have an obligation to do so.”
[Editor’s Note: This article originally appeared on SocialFunds.com, and is reprinted with permission.]
Factory photo CC-licensed by Flickr user Gualterio Pulvirenti.
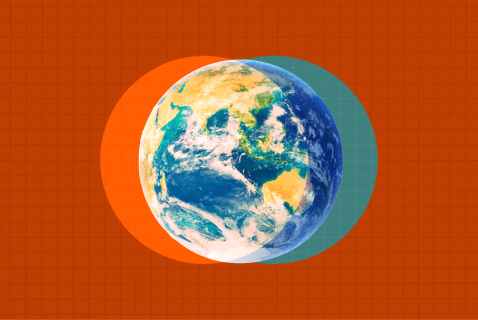