How AI and robotics are shaping the MRF of the future
Sophisticated materials recovery facilities of the future won’t be cheap. Will they have payoff for recyclers and their customers? Read More
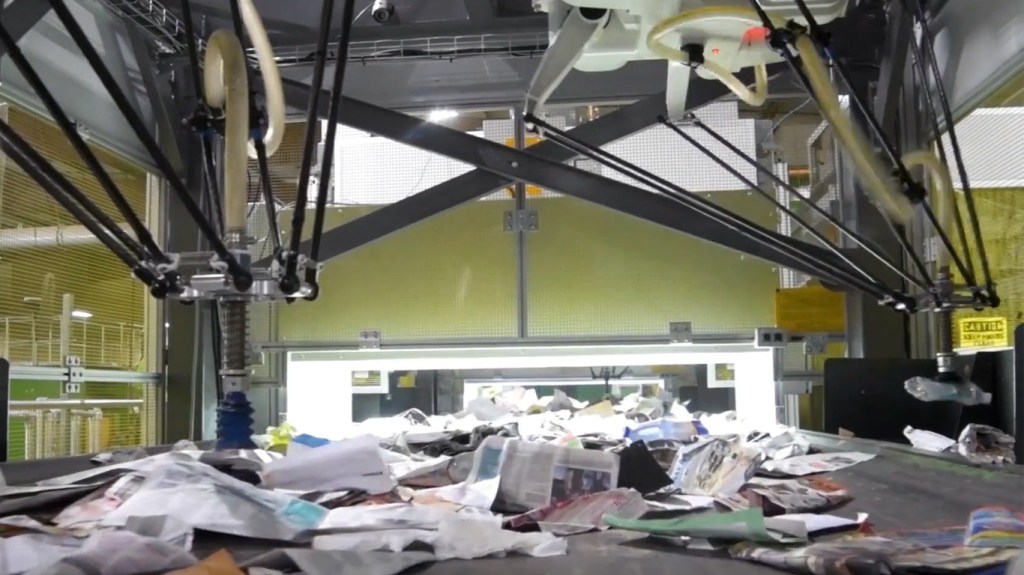
The Cortex technology from AMP Robotics is being put to work at MRFs
Recycling has taken hard hits in recent years, laying a rough road for businesses driving to up their sustainability goals. Cheap fossil fuel dulled recyclables’ competitive edge over virgin plastics. China’s import ban and then COVID-19 caused further market disruptions — on top of traditional industry pain points: labor shortages; fast employee turnover; and worker safety issues.
To change the competitive dynamics, some materials recovery facilities (MRFs) and waste managers have turned to highly automated systems using artificial intelligence (AI), where machines learn from data generated by software apps to recognize and sort materials.
These robots and other smart sorters work a lot faster than humans with impeccable accuracy, and are immune to ordinarily tough conditions, according to AMP Robotics, TOMRA Recycling and other tech developers focused on using AI to help change the economics of recycling. Better yet, the sorters keep on learning over time, adding to the repertoire of what they can pull accurately.
But these sophisticated MRFs of the future won’t be cheap. Will they have payoff for recyclers and their customers?
TOMRA Recycling is among the early AI pioneers and believers. The Norwegian company’s machine learning technology creates a mathematical model, based on information obtained about a large amount of material samples.
The model is applied to data generated by a camera, which identifies materials on the belt, enabling machines to make sorting decisions. Ultimately, air valves on a blower system are prompted to open and close to eject unwanted materials and let everything else pass through.
Depending on factors such as material type, the system can knock out three or four tons of output an hour, said Daniel Bender, technical manager of TOMRA Recycling.
TOMRA’s maching learning creats a mathematical model that is applied to data generated by a camera, identifying materials on a sorting belt. Image courtesy of TOMRA
“We added a method to learn from samples what to sort, and with precision to lead to a very high-purity stream. We are also obtaining information to be able to add more materials,” Bender said.
TOMRA has started with plastic. It is testing other materials, but the company declined to specify the type.
The company is also working on another innovation: laser sensors. By assessing how much laser light is absorbed or reflected, MRFs will be able to identify specific materials by color.
More sensors will evolve over time, unleashing more information, Bender projected. He cited as an example X-rays, which would help identify more than materials’ outer shell reveals.
“What shows high potential is the combination of different sensors observing the waste stream and fusing the information. That could enable the ability to tackle the most difficult sorting tasks common in the recycling industry,” he said.
Smarter recycling robots
Colorado-based AMP Robotics has its own spin on machine learning similar to TOMRA’s, but the AI platform communicates with robots — not a blower system.
Known as Cortex, the robot arm picks twice as fast as humans and with 99 percent accuracy, said Matanya Horowitz, founder and CEO of AMP Robotics.
Add to this skill set the fact that robots can go all day and not get tired or distracted. They don’t mind the gruelingly repetitive nature of the work. They aren’t fazed by dust, hot or cold temperatures and are equally immune to COVID-19 and injury.
The Cortex technology is being put to work mainly at MRFs but is also clocking hours at electronic waste processing plants, construction and demo facilities, and at reclaimers.
The robots have been busy. The entire fleet, deployed in North America and Japan, recently made over 1 billion picks in 12 months.
“We spent a lot of time, blood, sweat and tears to build powerful technology that can be deployed in different domains. We think this ability to adapt to many streams, along with high accuracy, is what distinguishes us,” Horowitz said.
While AMP’s system is broad in application, it also can be quite specific. It can sort by brand, and even down to one product, such as a carton of organic skim milk made by Horizon.
Horowitz explained: “It captures SKU numbers (associated with merchandise). So if brands want to recover their materials, our system can provide that functionality.”
Here’s what in it for brands
But will brands buy in? Apparently, Keurig Dr Pepper is interested. It has partnered with AMP and recyclers to recover its coffee pods to see if they could be funneled back into the circular economy.
As AMP focuses on expanding the materials its system can sort, it’s also added a business model: a robotics lease plan for companies that want to forgo large expenditures. Neither AMP or TOMRA would disclose pricing information.
In its effort to advance a circular economy, Closed Loop Partners collectively has invested millions of dollars in machine learning, including monies to AMP Robotics, Balcones Resources and municipalities.
Why place such high stakes?
“AI can transform the economics of the entire system, increasing the efficiency and consistency of sorting and processing of valuable recyclables,” said Georgia Sherwin, director of communications and strategic initiatives at Closed Loop Partners.
More is to come, contend developers, because these evolving systems continually recognize new shapes, colors and other features, making machines quick learners. Couple this with the fact that they’re fast sorters too, and these MRFs of the future could make targeting more items economical, even with fairly low volumes.
Perspective from the field
RDS-Virginia runs four robots it purchase from at its Roanoke MRF, at a cost comparable to hiring eight human sorters.
Joe Benedetto, president of RDS-Virginia, eventually expects a full return on his investment of a year and a half ago.
“We have not had the constant expense of finding and training employees for a job that few people want to do. There is less cost in personal protective gear; robots don’t wear gloves or need safety equipment. And we have seen a reduction in workers comp payments and injury rates,” Benedetto said.
What he can tell his clients weighs as heavily for his and their bottom line.
“We service municipalities as well as commercial and industrial operations and other company types,” he said. “Their goal is to recycle as much as they can. We tell them confidently that we achieve higher recycling and lower residue rates at equal cost. That’s mainly because the robots have a higher productivity rate throughout the day. They just don’t get tired.”

The AI platform developed by AMP Robotics communicates with robots, which can pick items twice as fast as humans with 99 percent accuracy. Image courtesy of AMP Robotics.
Optimizing corporate recycling plans
Another company — RoadRunner Recycling — has come to light for its machine learning technology, but you won’t find its brainchild in a MRF. Its customers are the waste generators: businesses in manufacturing; light industrial; health services, among niches.
Like other AI technologies, RoadRunner’s system is based on a mathematical model from stored data, but its data is from customer invoices and market information and is used to help predict effective recycling plans. Money savings are a gigantic part of the company’s pitch, according to the company’s chief executive.
“Sustainability is top of mind for our customers, but they wrestle with the fact that waste management has historically been a tough industry to rely on to advance those goals. Recycling is expensive and hard. The point of forecasting is to help our customers implement programs that are achievable while saving them money,” said RoadRunner CEO Graham Rihn.
On average, customers save 16 percent in waste and recycling expenditures and increase diversion from landfill threefold, he said.
A customized forecaster, based on business type and region, is key.
“How do you use data to inform what’s achievable in Philadelphia at a hotel versus at a freight company in the Midwest? Our forecaster tells us this hotel in Washington, D.C. should be able to recycle these materials, and it will save money,” Rihn said.
RoadRunner, which also implements recycling programs, recently received $28.6 million for expansions. Some of that money will support the ongoing buildout of its machine learning technology.
What’s really powerful, developers said, is that with their tools, recyclers are not constrained to human knowledge in order to keep growing.
Rihn used his platform to exemplify: “We do not have to make decisions thousands of times a month about what goes in our forecasts. We are creating insight through data. And since that insight is in the software, it will scale.”
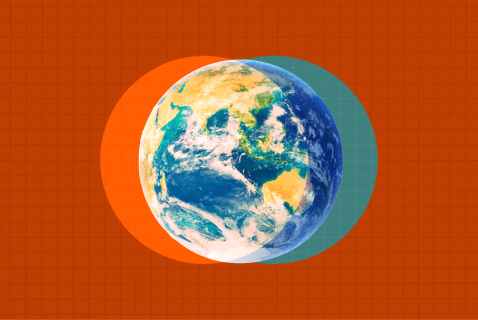