How Chicago's quirkiest companies sprouted a circular economy
For those in the business of mushrooms, kombucha and aquaponic farms, culture and engagement drive pollution prevention. Read More
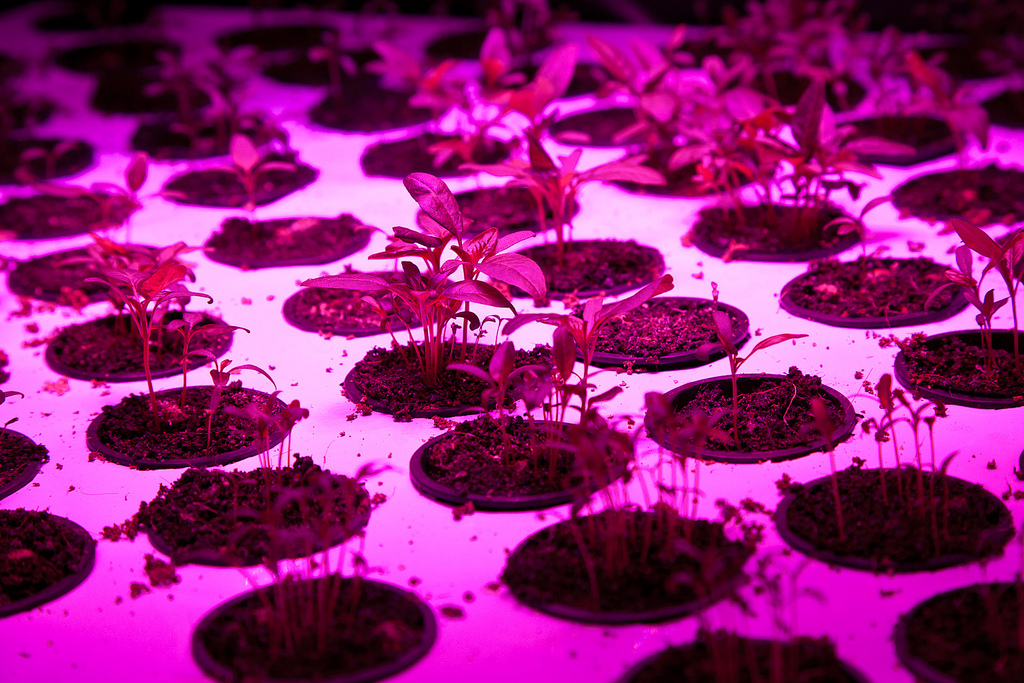
Efforts to reduce pollution in the production processes — especially at factory scale — often focus on technological or management solutions. But another side of pollution prevention warrants attention: Culture.
The culture of a facility can facilitate effective and innovative pollution prevention efforts. Of course, culture must be supported by skills and abilities, the capacity to enact change.
I have become keenly aware of the power of culture and capacity-building in my work with the organizations and businesses at the Plant, a community of food businesses operating in a repurposed meat-packing facility on Chicago’s south side.
Tenants at the Plant leverage a mix of food production skills, construction know-how and cultural norms — such as a preference for reuse or recycling — to create a food system that minimizes many standard environmental impacts.
The facility is a building, a business community and living laboratory all in one. The 94,000-square-foot edifice is a former meat-packing plant, closed and left vacant in the mid-2000s. In 2010, the building was acquired by Bubbly Dynamics, a team of building refurbishment and DIY experts led by John Edel, who envisioned the building as both vertical farm and food business incubator.
Within months, Edel and his crew had several spaces in the building cleaned up and ready for aquaponic farms, mushroom cultivation and kombucha brewing — all the while keeping close track of scrap material and other building features that might be repurposed in the future.
At the same time, Edel and several friends in the agriculture and environmental communities founded Plant Chicago, a nonprofit organization intended to drive indoor farming innovation and educational activities at the Plant. The Bubbly Dynamics and Plant Chicago teams drafted a blueprint for the types of farms and businesses to be operated within the Plant, including innovative ways to exchange traditional waste materials among them:

Production at the Plant
Fast forward to 2015. The Plant is home to a growing list of tenant businesses and thriving volunteer, education and farmer’s market programming led by the nonprofit.
Among the tenants are Pleasant House, a pie shop and bakery capable of supplying a full-time restaurant and three farmers markets per week; Arize Kombucha, which distributes over 500 gallons of fermented tea per month to Chicago grocery stores; Fruiting Mushrooms, an indoor mushroom farm on its way to producing 500 pounds of oyster mushrooms per week; and Patchwork Farms and Bike a Bee, two outdoor operations that supply vegetables to CSA subscribers and local honey to farmers market customers.
The nonprofit runs an indoor aquaponics farm that supplies vegetables for their weekly farmstand and an educational experience for over 1,000 tourists every month.
Research conducted by Plant Chicago summer interns showed that building refurbishment and tenant production activities yield over 40,000 pounds of material per month — 40 percent as finished products and 60 percent as byproducts.
These byproducts traditionally would be termed as “waste,” but that term is taboo among the Plant community. Over 90 percent of the byproducts are reused, repurposed, composted or recycled.
No material is off limits for reuse or reprocessing in a place where lunchtime conversation often revolves around commodity values and compost technology and where the visitor lobby features mushrooms growing on waste coffee grounds.
Pollution prevention at the Plant
Given the growing scale of production and variety of impact-avoidance activities at the Plant, it’s not too early to apply a pollution prevention framework to the entire project in the same way that a large industrial food production facility might.
Although a full life-cycle accounting has yet to be conducted, a first glance at the Plant through a pollution prevention (let’s call it “P2”) lens reveals many instances of robust source reduction, carried out by a variety of tenant businesses.
The largest example is the building itself. Food businesses at the Plant are able to harness the floor drains, insulated walls and sturdy construction of the 1920s for the water and material-heavy work of food production.
On a smaller scale, Plant Chicago teamed with Bubbly Dynamics and local furniture builder to have all their farmstand tables, cabinetry and shelving made from parts salvaged from the building’s meat-rail (pig body transportation) system.
All of these activities skip over “buy new” impulses and opt for innovative repurposing instead. A non-exhaustive list of other source reduction activities at the Plant includes:

In industry, many of the best P2 opportunities arise when a company is able to empower employees at all levels to participate in the problem-solving process. Indeed, multi-level involvement is included in most process-improvement efforts, such as value stream mapping (VSM) and Kaizen events.
While Bubbly Dynamics does not currently implement such processes with its tenants, the Plant community still succeeds in continually ideating around resource-use issues and implementing real solutions.
Having worked with Plant Chicago (the nonprofit) and many of the Plant’s food-production tenants, I have observed a range of factors that drive innovation within the building. I divide these factors into two categories: culture, a set of behavioral cues that arise from conversations and shared beliefs about improving the food system; and capacity, the Plant community’s food-production, construction and engineering knowledge and skill base.
P2 culture
Culture is a powerful factor in determining business decisions and direction, especially in small businesses. The Plant is home to an entire community of small and startup businesses with owners, managers and employees that share essential concerns about how their businesses are run.
Waste generation and electricity and water use are, of course, key concerns. Such shared concerns mean it’s easier to get tenants on board with recycling and composting programs and installation of water and energy-saving technology.
But the culture of the Plant goes beyond addressing these basic sustainability issues. Business owners at the Plant are empowered by their neighbors to explore business decisions that normally might be viewed as non-traditional or risky.
Before recently launched Whiner Brewery and Four Letter Word coffee roaster even moved in to the building, they were consulting with fellow tenants on ways to reuse spent grain and yeast, carbon dioxide exhaust and coffee bean chaffe and grounds.
The Plant’s P2 culture is reinforced by a larger culture of sustainability among tenants, volunteers and visitors who occupy the building. A culture of sustainability is not simply imposed by the building management.
Rather, it is formed by a collection of factors: tenant business models, social interaction among individuals, prevalence of closed-loop vocabulary and signage throughout the building, and certain traditions and events. Many of the Plant’s tenants have a business model and marketing approach that hinges on material reuse and local reliance.
Pleasant House promotes its sourcing of Illinois-grown organic wheat. Arize Kombucha is known for collecting its empty bottles for reuse. Furthermore, Plant Chicago guides hundreds of visitors through the building every month, and hosts community events with an explicit goal of promoting a “circular economy.”
The trend of bicycle-based transportation is a great example of shared and supportive culture. In a world of cheap fuels, transporting product by bicycle doesn’t normally qualify as “economical,” but it wins praise and recognition among customers, and tenants are able to share best practices such as bike trailer design and construction.
At least four of the Plant’s 12 businesses — Nick Greens, Patchwork Farms, Urban Canopy and Bike a Bee — transport some, or in the case of Bike a Bee, all of their product by bicycle. Many others at the Plant commute by bicycle. Edel himself bikes a 20-mile round trip every workday — rain, shine or snow — and in 2014 the nonprofit was a winner in the Chicago Bike Commuter Challenge.
P2 Skills
Given the variety of environmental, mechanical and chemical processes that operate on a daily basis at the Plant, and the fact that many businesses operate in a scrappy, startup manner, there is a great need for what I call “do-it-yourself courage and know-how.”
The courage to try new things comes from the Plant’s culture, but the DIY successes come from actual skills, held or acquired by individuals.
Bubbly Dynamics, the building owner/operator, brings a host of skills that drive creative reuse within the building. Their construction, metalworking and woodworking skills have enabled projects such as the creation of bathrooms from the building’s old smokehouses and the refurbishment of chillers left behind from the meatpacking days.
The skills collectively held at the Plant — between indoor and outdoor farmers, bakers, brewers, engineers and artists — are behind such cool projects as the algae bioreactor that runs on wastewater from the shrimp farm and the old commercial refrigerator repurposed into a mushroom fruiting chamber.

The Plant’s source reduction and operational innovations are “people-powered” in a variety of ways.
Some, such as emissions-reducing bicycle transport, are literally driven by human energy. Others, such as the repurposing of building features and waste-products, are powered by do-it-yourself courage and know-how.
This combination of capacity and culture has transformed the Plant into a model P2 community of practice.
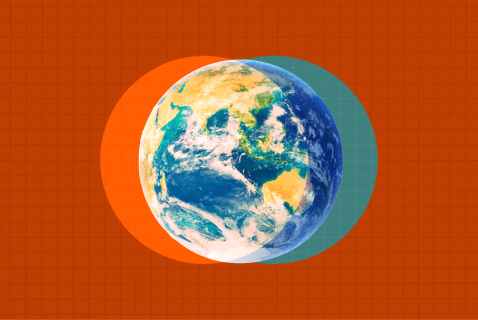