How to leverage EMS data for the greatest ROI
Sponsored: Saving on energy, water and waste spending is a priority for multi-site facilities under pressure to do more with less. Read More
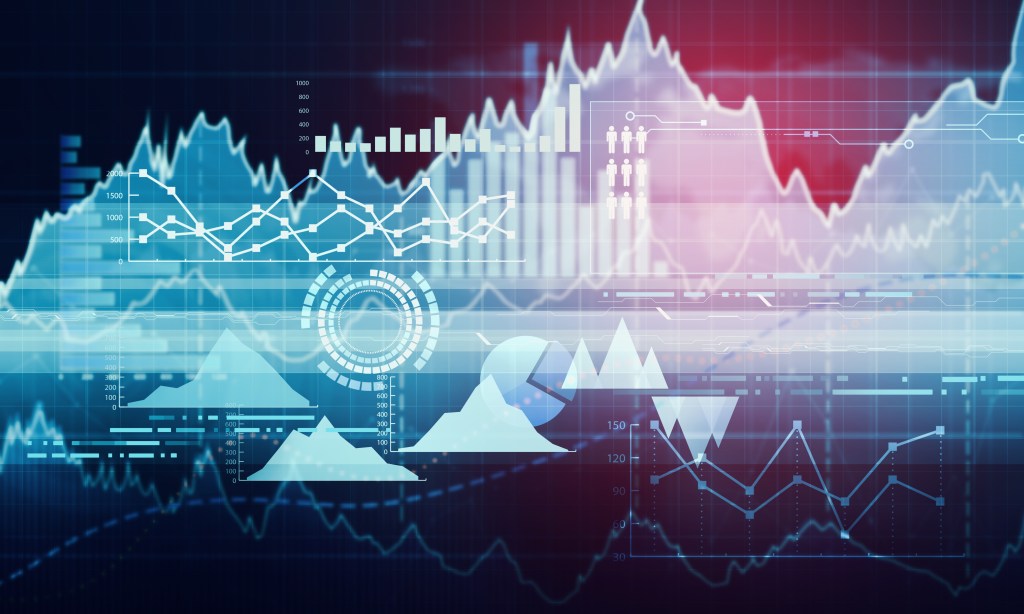
This article is sponsored by ENGIE Insight.
Despite differences in geography, size, service and customer base; multi-site facilities have this in common: They are all being pressured to see more, give more and do more with less. They face internal demands to track and save on energy, water and waste spend.
This is why innovative companies are leveraging energy management systems (EMS) as a valuable tool to manage energy-consuming assets in facilities. EMS gives companies greater visibility and control of each facility and its assets and a means to collect cost and consumption data. Whether a company has five sites or 500, without EMS, companies must blindly rely on site-level staff to ensure adherence to standard configurations, respond to alarms and oversee asset maintenance.
In addition, there is little cohesive insight into energy cost and consumption or how to improve. Overall, savings achieved by EMS are not necessarily attributed to the system itself, but to identifying and acting on the issues that EMS highlights.
Energy insight and sustainability efforts from Your EMS
During a recent webinar, ENGIE Insight conducted an informal poll of participants, asking what they felt were their top challenges in monitoring and maintaining assets at their facilities. Half answered, “Leveraging EMS data to make strategic decisions.” If your company also finds it a challenge to extract and manage the data from EMS, you are definitely not alone.
Think about the watch or fitness band you wear that tracks and provides data about your daily activity. You probably use that data to increase your steps each day, eat healthier or get more sleep. Without data, you’re basically just wearing a watch. The same concept holds true for EMS — once EMS in place, it’s essential to have a process to extract and analyze the wealth of information that the system provides in order to make critical business improvements. Leveraging this data and information can help companies reduce operating costs and provide insight to operational improvements, including:
- Increased productivity
- Equipment baseline and lifecycle reporting
- Portfolio-wide energy consumption benchmarking
Tracking data helps establish standard metrics and baselines that will help manage resources. By analyzing the asset level data from EMS, companies can reveal sites and equipment that are performing sub-optimally. Analyzing energy drift can help identify other smaller issues that may have gone unnoticed, leading to bigger expenses over time. Data points then can be compared with internal and external benchmarks, contrasted with peer sites, tested against previous configurations and used to promote an ideal sequence of operations.
One large regional, multi-site retailer adopted an integrated approach to energy management, employee engagement and sustainable business practices with the goal of reducing energy use by 20 percent. They maximized the value of their EMS and smart meters by:
- Prioritizing locations for EMS installs based on the greatest ROI, monitoring and resolving EMS alarms and inbound service calls remotely where possible
- Executing EMS re-commissioning at over 20 locations to make sure sites were properly controlled
- Installing smart meters to record electric consumption in 15-minute intervals to verify and measure the effectiveness of energy efficiency projects
This strategy yielded tremendous bottom line savings, operational efficiencies and data insights. At one recommissioned store, the project alone resulted in a 16 percent energy reduction in just one year. Other pilot projects — such as an LED retrofit and HVAC retrofit — reduced energy consumption by 60 percent and 20 percent, respectively. The data from these pilot projects led to more retrofits throughout the company and even greater savings. Overall, the company achieved a 22 percent energy reduction, five years ahead of schedule.
EMS and connected buildings
One common question is, “How do we manage it all?” The IoT revolution and smart buildings does not mean that it’s set it and forget it. Businesses need both consistency and efficiency, and this can be a challenge, especially for those that have a large portfolio and operate across multiple sites. Technology is great at identifying when there is an issue, but people need to take action to resolve it. Having a centralized approach is key to address failures, optimizing performance and proactively managing your facilities. Whether it’s internally or through a third-party service provider, businesses must have a strategy for action to be successful.
5 best practices for EMS
Through researching some of the most recognizable multi-site companies — spanning restaurant, retail, grocery, convenience store and more — the following five best practices have been identified as able to maximize the ROI of an EMS:
- Maintain and enforce documented standards: Implementing corporate-wide configurations should be a key component of an overall energy strategy when commissioning EMS. Capture the optimal configuration for your facilities — even if there are multiple versions based on the type or function of the building or its geographical location. Then gain internal support to implement and enforce the standards.
- Monitor system overrides: EMS can help optimize the balance between occupant comfort and energy savings, until a human overrides the system. To avoid these changes from adding up, first address any recurring comfort concerns. Then establish set point standards and user permission levels to authorized personnel only. Through continuous monitoring and management, ensure systems are set properly, and when manual overrides are identified, take quick action to bring the system settings back to standard levels.
- Regularly check sensors: During EMS installation sensors are initially placed, but over time, as facilities and the environment around them change, the location may need to change. Leverage sensor alerts or data to look for outliers. Ensure that sensors are not affected during remodels and site improvements. Use technology to gather sensor data in one place, then standardize and centralize it on one streamlined platform.
- Establish an alarm strategy: Alarms are a key function of EMS, but there can be hundreds each day — some are true issues, but some are what we call false or nuisance alarms. Establish an alarm strategy that encompasses your entire portfolio, including an alarm matrix that identifies which alarms are most important to you and your organization. Reconfigure systems as needed to fine-tune the alarms and alerts to notify the right people on actionable issues and not send out notifications on low-priority issues.
- Implement maintenance checkout procedure: When technicians are on site, they may have silenced an alarm or disconnected the asset from the control system, and then that asset becomes invisible to EMS. So establish a checkout procedure when anyone is onsite to verify that all standards and parameters have been implemented prior to the technician leaving the site. This dramatically can reduce recalled work orders or callbacks to fix issues that should have been resolved the first time.
The best practices addressed above constitute a comprehensive and productive monitoring program, capable of maximizing EMS ROI. It can take a significant amount of work and resources, but active management will more than pay for itself. Also consider the value that a third-party monitoring and maintenance solution can bring to your company and bottom line. For more information, we invite you to view our webinar for a deeper look into turning EMS data into savings.
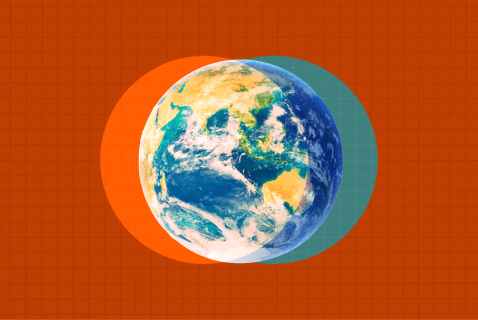