How Toyota uses gentani to optimize performance and cut waste
Toyota's environmental affairs lead explains how the company continues to find ways to do more with less. Read More
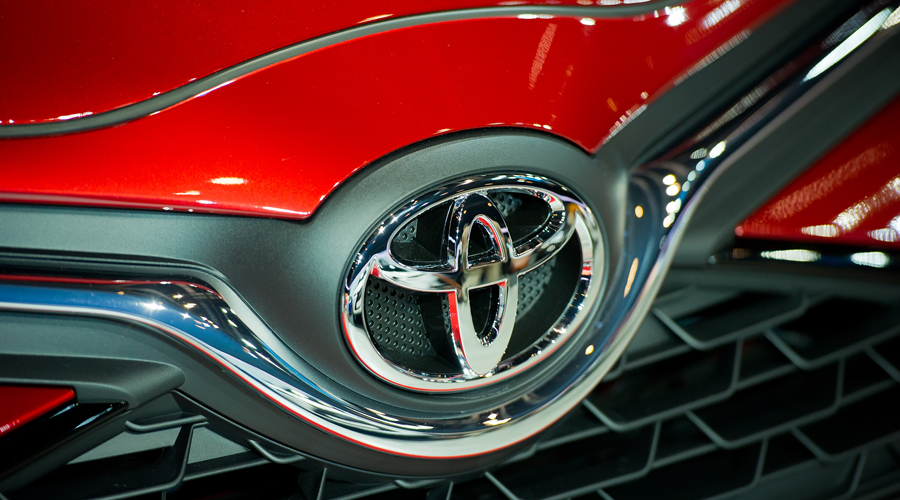
Steve Hope is clearly a man who loves his job. Working inside the Japanese vehicle manufacturer Toyota in Europe since the early 1990s, he is proud of what he and his team have achieved in seriously driving out waste and cost from production processes. “We’ve been challenging the way we operate our plants for many years and struggled away quietly.”
Now, he’s ready to tell the world just how radical its resource efficiency has been. Take the U.K. plant, for example. Between 1993 and 2013, it reduced its energy usage per vehicle by more than 70 percent. In the same period, it also reduced water use per vehicle by more than 75 percent, and waste produced per vehicle by nearly 70 percent. It’s incredibly impressive.

I caught up with Steve at the latest 2degrees Live summit, which showcased the very best examples of company’s getting to grips with energy, waste and water, and he explained how Toyota continues to find ways of pushing the envelope despite a lack of limitless resources to improve its processes.
Tom Idle: You’ve been tackling resource efficiency for years, not least driven by the famous Toyota production system. Are you happy with current progress?
Steve Hope: Well, it’s only in the last five or six years that we have started to speak about our progress; the previous 15 we didn’t.
Toyota is conservative with a small “c”; we like to talk about what we’ve done, as opposed to what we might do in the future, so that we avoid greenwash. Our numbers are impressive — and it’s not just because of variations in production volume.
Idle: So, data is not really a problem for you guys, is it? You’ve been tracking performance for years now.
Hope: We’ve been tracking data, but that often isn’t enough in itself. My old team in Toyota Motor Manufacturing U.K. [Steve is now based in Brussels as part of the strategic management team] developed a SCADA system all by themselves, rather than just taking one off the shelf in order to better understand the need and use of data. They are able to pinpoint, with great accuracy, who is using what amount of energy at what time and break it down into minute-by-minute intervals. There is a lot of granularity in that dataset.
However, when you look at an individual processes, there is always scope to go deeper. Today in 2 Degrees live we have heard a lot about food refrigeration systems. You can only tell whether it is working optimally by really drilling down into the parameters that have been set for it in the first place. Were the right numbers used? Minus 18 degrees is said to be the optimal temperature for a food freezer. But why minus 18? Is this the minimum use of energy to achieve the requirement?
We have a name for this type of parameter inside Toyota. We call it gentani — to understand the real minimum resource that you need to carry out a process.
Idle: So, is this about knowing what “good” looks like?
Hope: Yes. Take this bottle of water on the table in front of us. If we were to take that water from ambient temperature to 100 degrees to make it boil, that volume of water would need a certain amount of energy to take it through that process — anything additional energy you put into that bottle of water to raise the temperature from your supply is waste. When you know what your minimum is — that is the true target. It is a different approach to simple benchmarking.
Idle: And how far have you traveled on this journey towards understanding the gentani of your processes?
Hope: I’m not going to big it up and say we are the best in the world. It is only in the last five or six years that we have really started to embed this type of thinking in something like energy, as opposed to other processes like cutting steel out of a steel roll.
We have adapted a philosophy that is used our production technologies into the world of the environment using the Toyota production system.

Idle: Is there a limit to achieving incremental efficiencies? Are there clear points where serious investment is needed?
Hope: Yes. And we try to identify those opportunity points — many of which will only present themselves on a cyclical basis.
Model changes might be one of those points, where we change from car A to car B. It is at that time you might be able to change some process technologies more easily. However, if you are running equipment that is part of the infrastructure of the plant’s heating and ventilation, for example, you have a long lifetime on that equipment and it may not be possible to just “junk-out” that equipment and install new technology. You would have to consider it at the point of natural economic refurbishment.
LED lighting is a perfect case in point. Can we justify within our investment criteria throwing away all of the lights in an assembly shop and putting new lights up, bearing in mind the majority of cost is labour and access? No.
But if we plan it in for next year when we are going to maintain those lights anyway, we might then find an opportunity.
No company has a huge amount of resources to limitlessly invest in this sort of technology change — we have to compete with resources with every other division. So, we try to match and balance things up.
Idle: A lot of your success comes from bringing people internally along the journey with you. How do you do that?
Hope: It’s no good giving the line worker in an assembly shop the responsibility of thinking where we’re going to be in 2050; we need him to do his specific activity, and do it well.
The CEO’s KPIs are not the same for the member on the shop floor — even if we break it down. To oversimplify, it could be his job to turn the lights off at the end of production, and he should therefore be measured against whether he turns the light off or not.
You also have to change the metrics sometimes because the top-line metric is not something the bottom line person can affect. If you’re not involved in making the contract, for example, you can’t really affect the unit cost — all you can affect is the number of kilowatt hours of energy you use.
There is a lot of psychology going on. You can’t tell people to do something, you need to educate and encourage them. You are not in a command and control position.
Toyota may seem to be leaders or role model; that is very nice. But actually there is still a lot to do. It will be a blend of continuous improvement — what we call kaizen — and disruption that will come at intervals. Some changes in technology will be driven by a balanced consideration of quality, durability, customer demand, cost, legislation and the life cycle of the equipment already installed.
Idle: Would those disruptions ever occur for purely environmental reasons?
Hope: It has happened in the past. We were using solvent-borne technologies and now we are using water-borne.
Idle: So, what’s keeping you occupied right now?
Hope: Well, from a plant perspective, they are keeping their noses to the grindstone. They are looking for opportunities for further kaizen and efficiency gain and these opportunities for step-change.
But from a European strategic level — we are not just looking at manufacturing, but also our products from the full life cycle perspective. For example, we are now considering where we will be in 2020. In 2016 we will commence our sixth 5-year action plan that runs to the end of the decade.
Idle: Can we expect anything radical from the next five-year plan?
Hope: It’s impossible to say because we are still considering the details.
Idle: Well, will it need to be radical to take you where you need to get to?
Hope: It needs to be a balance. To take people along with you, you have to create a vision. But the vision also has to have certain levels of attainability within it.
In 1993, we said we wanted to go zero waste to landfill at the U.K. Plant. We gave ourselves five years to do it and whilst we believed it was attainable, we had no clear idea how we were going to get there. It was something we brought out of the air, mainly because of societies’ need to reduce landfill and the forthcoming tax. We wanted to find both a challenge and a way to insulate ourselves against future rising costs. Despite this tough challenge, through the great efforts of our U.K. members we were able to achieve the target two years early.
It’s going to be the same for the next five-year action plan. We’re at position A and position B is over there. Are we going directly towards B? We don’t truly know. But as long as the vector is taking us in the right direction, we will make that step and move forward. And, generally speaking, that is a good way — within Toyota at least — to simultaneously both promote the idea that anybody within the organization is able to contribute through kaizen and promote innovation.
You can see a more detailed exploration of the Toyota story here, as Steve presents at the 2degrees Live summit:
This article originally appeared at 2 Degrees Network.
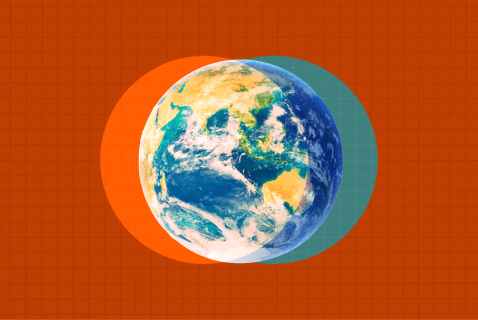