How to Work with Your Vendors to Go on a Packaging Diet
Even if you're conscientious about the three R's when it comes to packaging, odds are your vendors are still shipping you excess materials. These three steps can help you ship smarter and greener. Read More
Packaging — especially wasteful packaging — has become a bright spot on the radar for companies and individuals that are working on reducing their environmental impacts. But even the most proactive companies are finding that the problem can’t simply be addressed in-house.
In my work in the IT department, I am constantly frustrated with the wasteful product packaging we receive from our IT equipment vendors. And the complaints are widespread, as in these examples I’ve gotten from our customers.
“Software licenses were sent in a large box bubble wrapped inside a cardboard envelope!” Steve, an IT Service Provider, told me. “Surely in this digital age something like this could be communicated electronically?”
The amount of materials is one of the biggest challenges, according to Stephan, who operates a large data center. “Plastic bubble wrap, empty cardboard spacers inside of cardboard boxes, surrounded by foam peanuts, and topped off with documentation that nobody will ever read or use — it’s ridiculous!”
Along those lines, the waste is so excessive that Rick, who works at a government agency, explained, “We had to hire a part time person one day a week just to dispose of this stuff in as green a manner as we can.”
Finally, Simon, a customer who works in financial services, wrote me that “A typical server arrives with about five pounds of wasteful metal and paper. The extra manufacturing and shipping costs are extremely wasteful. If we, as customers, can figure out their motivation for adding these parts and not being more conscious of their packaging then we are more likely to be successful in pushing for a change.”
That is the key point: Customers will have to be resopnsible for driving this change. And achieving significantly greener packaging is possible with a focused effort by our equipment suppliers to follow these three simple steps:
1. Eliminate unneeded items
2. Right-size the remaining packaging
3. Sustain with green packaging that is reused or recycled.
Letting the Bottom Line Go To Waste
Simon’s comment — that extra manufacturing and shipping costs are extremely wasteful — is perceptive. If tracked in the Enterprise Resource Planning (ERP) system, the impact of packaging waste to the equipment provider’s bottom line should become painfully obvious.
But all too often, the packaging costs are buried and invisible making change difficult to initiate. The good news is that, once they’re engaged, many IT equipment providers utilize Six Sigma or other process-engineering practices that are perfect for resolving this packaging problem.
Green Packaging Best Practices
These three steps are good starting-off points for working with your suppliers to cut down on waste, save on costs, and simply eliminate the hassle of dealing with wasteful packaging.
1. Eliminate unneeded items from the shipment
Suppliers should deliver all items virtually wherever possible (documentation, shipment info, licensing, etc). Progress in eliminating paper documentation from IT vendors is inconsistent at best, but customer demands for electronic paperwork will make progress possible.
Another way to reduce waste is for vendors to allow their customers to exclude any items that will be simply be discarded. Not shipping components like cabling, grounding straps, and power cords that may be duplicates or unnecessary will also reduce waste.
2. Right-size packaging
Oftentimes each component is in its own package, which causes packaging to expand dramatically. Consolidating items and shipments will reduce total amount of packaging.
Some suppliers already provide services to assemble pieces or consolidate orders, but to be most effective, the vendor should offer consolidation for a small number of units.
Many packaging engineers are confident that all the packaging is needed to protect products from damage. They correctly assert that a damaged product is also a type of waste that should be avoided.
Yet there is still an opportunity — even if it is just educating the people who are packing items to put items in the correct type of packaging and the smallest size package as possible.
Simple changes can make a big difference: When you’re assembling products in a rack, the rack itself provides protection and the standard packaging may be excessive. And sending packages in static electricity protection bags (those omnipresent pink bags!) are redundant if you’re also using a static-protecting box (or vice versa).
3. Sustain packaging
The first step to more sustainable packaging is simple: You must eliminate all packaging that cannot be recycled. After that, making boxes and other packaging materials easier to break down will support recycling by reducing labor.
Because processes to change packaging are often immature, it’s important for companies to work together with other technology vendors and recycling service providers to establish new recycling methods.
For example, pallets used for shipping are not typically recycled, yet are sturdy enough to be reused often. Some technology providers provide packaging pick-up, but it is difficult for customers to sort and segregate each vendor’s packaging.
Finally, in the midst of this economic downturn, increasing the amount of recycled product used in packaging helps to create a viable market for recycled materials. Cardboard is one of the easiest materials to recycle, but the market for recovered cardboard has plummeted in the wake of the recession, so companies are actually throwing it away rather than recycling it. Signaling that there is a demand for recycled cardboard will go a long way toward boosting that market.
Another area to explore is packaging that may be reused. Most of the packaging is cardboard-based, which has good recycling opportunities, but another approach is to use packaging that can be reused. A study commissioned by LINPAC Allibert, a U.K-based manufacturer of reusable packaging products, found that a plastic crate that is reused has a much smaller carbon footprint than a cardboard crate that gets recycled.
Next Steps
At my day job, I have partnered with the IT Director to work with our vendors. One of my colleagues suggested that perhaps a dramatic act is required to get the vendor’s attention: Maybe we need to start packing this excessive waste up and ship it back to the manufacturers just to make a point.
Making an abstract concept concrete is always an effective tack to take, so we plan to take pictures of the excessive waste as we receive orders and share those with the vendors. For any readers out there who are IT vendors, we realize that many of you are interested in improving packaging, and some have started dealing seriously with this issue; we would be thrilled to hear the results of your efforts and plans.
In addition to the individual follow-up with our vendors, we are also working with industry organizations to consolidate customer feedback, recommend best practices and share with IT vendors. Mark Thiele, founder and president of Data Center Pulse, a non-profit focused on data center best practices, has agreed to help champion this with IT DC vendors.
Join with me to share your stories and recommendations on how to improve packaging. Working together, we can achieve greener packaging.
Claudia Girrbach is a Senior Director in the IT department at Gap Inc., as well as a member of the company’s EcoCouncil and Employee Engagement Team. She also authors the blog Going Green – Tips for Business.
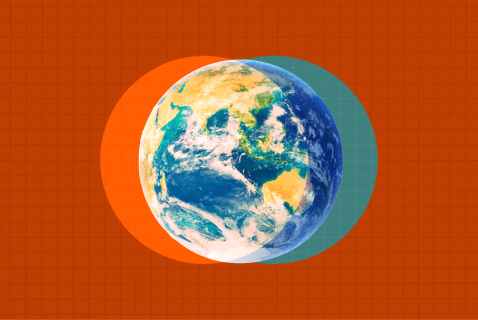