Ingersoll Rand's new plan for giving its products a second life
Its mindset is the polar opposite of the planned obsolescence strategy that drives many consumer electronics manufacturers. Read More
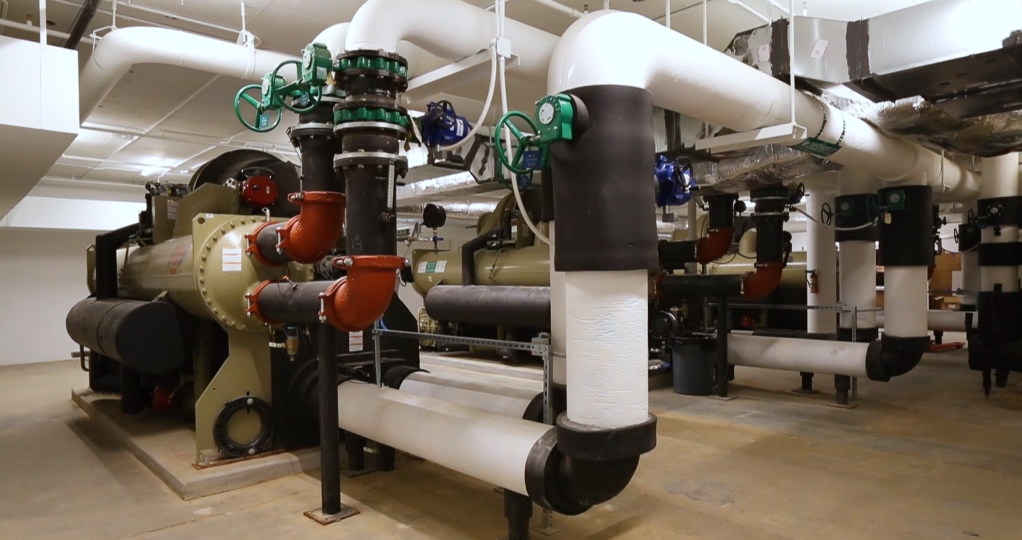
The concept of remanufacturing end-of-life equipment and mining it for valuable components and metals is nothing new to Ingersoll Rand: It has operated an aftermarket service organization in Charlotte since 1974. After all, many metals used to make its Trane heating, ventilation and air-conditioning equipment have a demonstrable value, and there are well-established processes for recovering it.
But in more recent years, the 183,000-square-foot operation, which employs about 72 people, also has become involved with activities focused on a different sort of mission: keeping older Trane equipment in the field for as long as possible by updating them with components and materials that help Ingersoll Rand accounts address their own carbon reduction and climate goals.
This wasn’t driven by a mandate to become more “circular.” Rather, the company saw value in rethinking its services to help customers meet sustainability challenges. When Ingersoll Rand revealed its 2030 sustainability goals this spring, the list included a number of unique and ambitious aspirations, including a commitment to reducing its customers’ carbon emissions by 1 gigaton by that timeframe. In case you’re wondering, that’s the equivalent of the emissions produced by Italy, France and the United Kingdom combined.
“Our teams are more focused on the idea of ‘customer for life,'” Scott Tew, executive director for the Center of Energy Efficiency and Sustainability at Ingersoll Rand, said.
This mindset, for example, guided a major project that the Ingersoll Rand remanufacturing unit completed for a historic hotel in Portland, Oregon. The property faced a major dilemma: it needed to update the compressor in its HVAC system, but physical access to the basement space in which it was located was extremely limited. It couldn’t just rip out and replace the existing equipment, which had been in service for almost five decades. “The best option was for us to go in and remove the guts,” Tew said.
This involved dispatching engineers to the site that could disassemble the relevant components and transport them back to the Charlotte site for an overhaul. The updated parts later were redelivered and reinstalled in the same footprint as the old system where they could “live” for two more decades, Tew said.
While the reverse logistics associated with the project were less than ideal — shipping the materials cross-country was time-consuming — this is a model that Ingersoll Rand will emphasize more often. It has made two major internal changes to support this strategy.
First, the company has included a requirement for all new product development that directs engineers to design for sustainability. That includes both efficiency considerations and materials choices. After all, if a system will stay on site for far longer, its makeup needs to be as safe for humans and the planet as possible.
Second, the company is part of a project being spearheaded by the United States Business Council for Sustainable Development (USBCSD) to develop materials marketplaces at both the national and regional and state level that help businesses more readily exchange and source items that are part of their industrial waste streams.
It’s becoming clearer that what might be considered “waste” by one sector or company actually could be a useful feedstock for another. In other words, creating a closed loop process might include reaching into other industries for materials, such as the how Dell uses recycled auto glass to create sturdy, waterproof laptop carrying cases. Some of Ingersoll Rand’s sites are participating in the state marketplaces created by USBCSD, Tew noted.
“All waste streams can be valuable, especially in the industrial space,” he said. “We just have to find that one other company, that someone who can look at this as a raw material.”
Stay tuned for more innovation from the Ingersoll Rand remanufacturing division, as the business reconsiders how to offer services of this nature as part of customers’ contracts.
This story was updated to clarify the way in which Dell uses recycled auto glass to create laptop carrying cases.
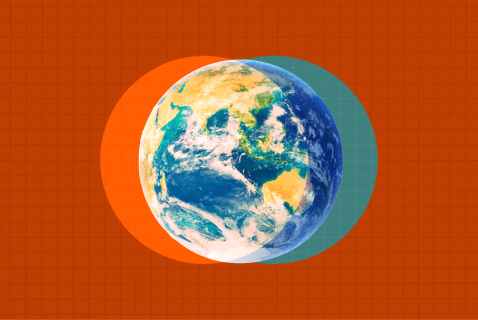