How a low-carbon cement innovator is moving toward commercialization
If Fortera’s California plant is successful, it will point a way to reduced emissions from concrete — a ubiquitous and hard-to-abate material. Read More
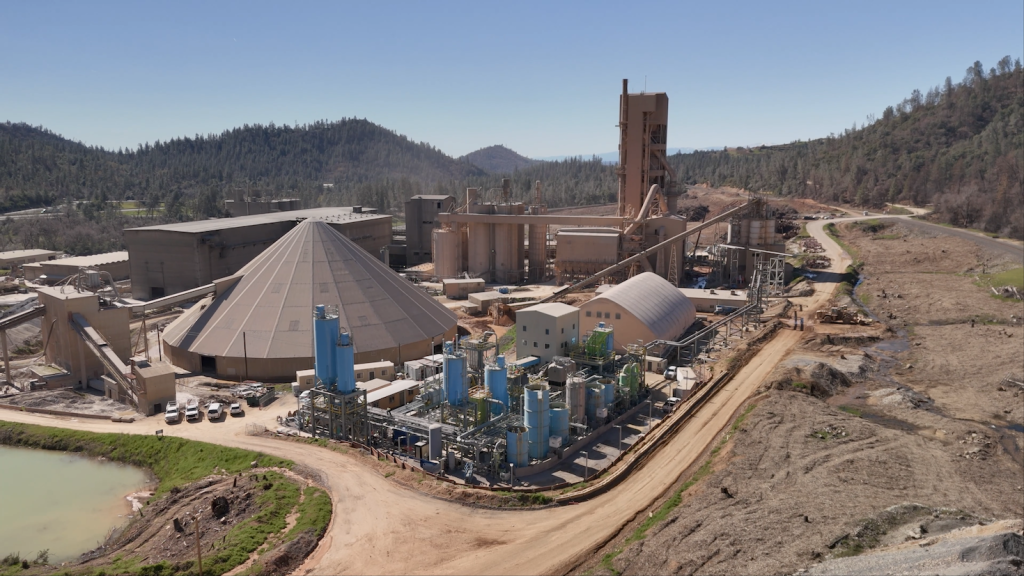
Construction is booming — new construction in North America is 10.5 percent above pre-pandemic levels. But if you’re a company with a net zero target, the emissions in your building plans are a problem.
Concrete is a major ingredient of just about every construction project, from office buildings to home foundations to highways and bridges. But concrete — particularly the cement it is made of — is responsible for 7 to 8 percent of global greenhouse gas emissions, according to the Global Cement and Concrete Association. And demand for cement will grow from 14 billion cubic meters produced yearly today to 20 billion cubic meters by 2050.
Under pressure from numerous governments and corporate customers to lower the emissions from cement-making, many of the world’s largest concrete companies have pledged to work toward decarbonizing the industry by 2050. The 2020 “Concrete Future” pledge included several major producers including CEMEX, Holcim, Taiheiyo Cement, Taiwan Cement and other members of the Global Cement and Concrete Association, which produced a Roadmap to Net Zero for the industry.
Founded in 2019, Fortera is one of a handful of low-carbon cement innovators that have made it through technology development and are poised to start commercial production. According to data collected by Crunchbase, Fortera, based in San Jose, California, is the only low carbon cement entrepreneurial company that has attracted Series C financing, securing $85 million in August from six venture firms.
The company began operating its first plant, in Redding, California, on a pilot basis in April. It’s adjacent to a cement-making factory owned by CalPortland, Fortera’s first customer and one of the largest construction materials companies in the U.S.
“The process works as anticipated, so we’ve progressed from pilot scale to commercial scale,” said Chief Manufacturing Officer Keith Krugh during an interview at VERGE in October.
The first-of-its-kind plant can capture and reuse 6,000 tons of carbon dioxide for every 15,000 tons of cement it makes, according to the company. If it succeeds in scaling up commercial production and sparking adoption, the company will have proved that low-carbon cement is viable.
The plan
There are several pathways for reducing emissions in cement-making, including carbon capture, using alternative chemistries in the clinker to replace limestone and changing the kiln heat source to renewable energy.
Fortera’s process captures the CO2 produced from heating limestone and reinserts it back into the process using a proprietary technology that converts the gas into calcium carbonate, or lime. Doing so recycles CO2 into a solid, or “cementitious” material that meets industry standards, while reducing emissions by 70 percent, the company says.
The inspiration for the technology came from nature, said CEO Ryan Gilliam. “In traditional cement-making, you take limestone, apply heat to decompose it into lime and CO2 emissions,” he said on the podcast Manufacturing Talks in September. Nature does the opposite, absorbing CO2 to use as a building block to form coral, for instance.
“So, we are doing it in industry, making a form of reactive limestone that is cementitious” by recycling the CO2 emissions from the limestone heating process as feedstock.
Fortera, which won the 2023 Net-Zero Industries Award for the U.S. from Mission Innovation, a global initiative of 23 countries and the European Union, also has memorandums of understanding with three other cement making companies interested in integrating Fortera’s ReCarb Plant with their operations.
The key to Fortera’s business model, Krugh and Gilliam said, is working within existing infrastructure to make the economics work for customers. Its ReCarb Plant operation is bolted onto a customer’s cement-making operation to capture the CO2 emissions and return them to the process. That means customers don’t have to retrofit or replace legacy factories, which represent significant sunk capital.
Fortera also makes ReAct Cement, a green cement product made via the ReCarb process that Fortera says can be blended with traditional cement or used as a replacement.
“By turning the 44 percent of CO2 that would typically have been lost to emissions back into product, we are able to manufacture Fortera product cost competitively with traditional cement,” said Krugh.
Turning one ton of feedstock into one ton of product reduces mining operations, material crushing costs and fuel in the kiln, he added. That’s crucial because construction companies have shown that they won’t pay a premium for low-carbon cement.
“It starts with having a concept that is technically feasible and provides value and that is cost-effective,” said Krugh. It helps that current federal and many state policies encourage construction companies to use lower-carbon materials in new construction.
The experiments
ReAct has been approved by the international standards organization ASTM for construction materials. And Fortera’s product has become certified for carbon credits. By using renewable energy to heat the kiln, producers can reach zero emissions, the company says.
In Redding, Fortera’s ReCarb plant captures CO2 emitted from CalPortland’s kiln during calcination — heating limestone — and reinserts and mineralizes it to produce green cement, a form of calcium carbonate. That will help CalPortland, a subsidiary of Taiheiyo Cement Corp, in Japan, reach its goal of becoming carbon neutral by 2050.
Another low carbon cement innovator, Holcim of Germany, won the Global Net Zero Industries Awards for 2023. Holcim’s project in Laegerdorf, Germany, involves the construction of a new kiln line that uses a unique second-generation oxyfuel process and a downstream compression and purification Unit, according to the Net-Zero Industries Award.
The future
Fortera already has other competitors: numerous other promising start-ups are developing low-carbon cement, including Material Evolution, Sublime Systems and Heidelberg Materials.
Fortera believes its formula will scale to gain significant adoption. “What you need to figure out with a new technology is how do you get to a capital cost and an operating cost [that becomes] something that they want to adopt,” Gilliam said.
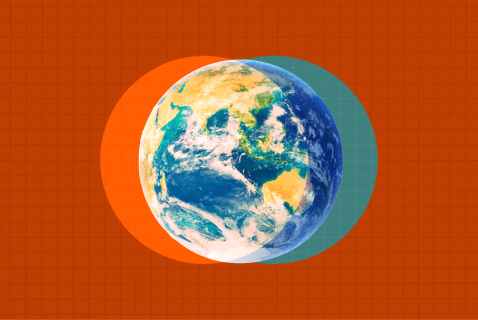