Obayashi's living laboratory for green building
Tokyo's Technical Research Institute holds one of the highest possible Platinum ratings for existing building operation. Now, it's going for net zero. Read More
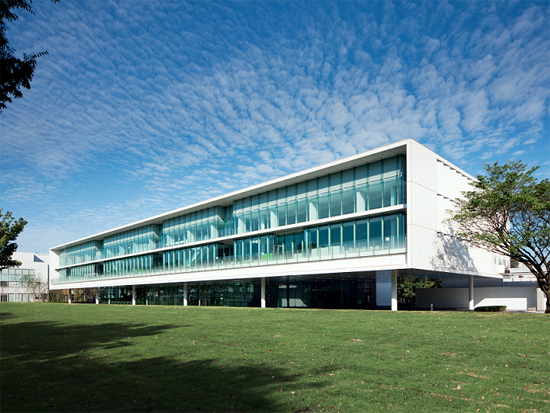
Tokyo’s Technical Research Institute managed by global construction firm Obayashi isn’t just home to one of the highest rated green buildings in the world, it serves as the company’s living laboratory for smart, sustainable architecture.
The core facility on the campus known as the Techno Station recently earned the highest LEED Platinum rating in Japan for Existing Buildings: Operations & Maintenance (EBOM), with a score of 95 points out of a possible 100. It also holds the third-highest score under LEED-EBOM v2009 in the world. The institute also received one of the highest certifications under the Comprehensive Assessment for Built Environment Efficiency (CASBEE).
“Obayashi Corporation felt that it was important to evaluate the building based on its actual operational performance in addition to its predicted performance,” the company said in a statement.
That’s because, eventually, Obayashi hopes not just to make this building net zero — generating as much power as it consumes — but to make it energy-positive.
“In order to make net zero happen, we need to use our energy more efficiently, both by saving energy and decreasing the amount of energy usage,” said Hajime Onojima, general manager, Environmental Solutions Department, Technology Division, Obayashi, in response to questions submitted via email by GreenBiz.
“As an example of a part of the effort, we are replacing the light bulbs with LED, and improving the lighting control. We also need to increase the energy generation amount, so we will be adding renewable energy sources on site. The renewable energy will be solar power; solar panels will be added next to the Techno Station building, by the end of this March.”
An ongoing collaboration
The ongoing performance of the Technical Research Institute is being tracked closely by a team including environmental contractor Webcor Builders (Obayashi’s subsidiary) and high-performance building advisors Environmental Building Strategies (EBS) Consultants. EBS was responsible for assessing the buildings performance using an ASHRAE Level II energy audit and for providing a cost/benefit analysis for energy efficiency upgrades. In addition, it developed a process to help Obayashi continue optimizing the building’s performance. One tool EBS uses to pull this off is a cloud-hosted collaboration tool from iLiv Technologies that helps the organizations manage across projects across several times zones.
“We use this tool as a way of communicating a lot of information, and project-managing the entire LEED process,” said Jacob Arlein, EBS partner and director of certification services.
The iLiv software carries a per-project, per-month subscription fee. A small project with 100 events and up to 1 gigabyte of data storage starts at $62.50 annually, according to the calculation tool on iLiv’s Web site. The cost of supporting this Obayashi project has not been disclosed.
The three-story building has a total floor space of slightly less than 60,000 square feet. The research department there is testing innovations centered on four areas for possible use in Obayashi’s global construction projects:
- Production Technology (construction materials, robots and finishes)
- Structural Technology (earthquake countermeasures, disaster prevention approaches)
- Environmental Technology (systems for heat, sound and air, soil purification and so on)
- Ground/Foundation Technology (building foundations, and work on ground/bedrock designs)
“The Techno Station was planned as an integration of the technologies developed by us, such as achievement of the highest level of energy saving, adoption of the world’s first active base isolation system, and the one-room type workplace aiming for the improvement of intellectual property,” Onojima said.
What’s inside
Some of the systems and design features that the Technical Research Institute is using — and that will be rolled out in Obayashi’s projects globally as appropriate — include:
- Peri-buffer systems that establish a thermal buffer zone around windows, to reduce air-conditioning zones in low-occupancy building areas
- Ambient lighting and climate controls that use sensors, so that they only operate when employees are present
- Slanted roof panels that make for better natural daylight and ventilation
- Solar arrays that generate enough power to support night-time workspace lighting
- Hybrid heat pumps that use geothermal energy
- A rainwater harvesting system that is used to flush toilets and urinals, helping reduce indoor water usage by up to 70 percent
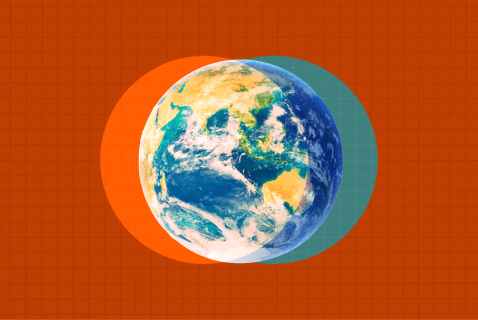