Olin Corporation Gets Big Return on Wastewater Scrubbing Operation
By modifying some of its processes, Olin Corporation’s Niagara Falls plant eliminated a 16,500-gallon-per-day waste discharge. As project manager Tom Muka explains, the old system was just money down the drain. By Emily Rabin Read More
Olin Corporation’s Niagara Falls plant is a chlor-alkali manufacturing facility that produces chlorine gas. By modifying some of its processes, Olin was able to recover and recycle a significant amount of its waste stream, eliminating a 16,500-gallon-per-day waste discharge. Tom Muka, technical manager for project implementation, told GreenBiz.com that old system was just money down the drain.
Emily Rabin: First of all, what’s a chlor-alkali manufacturing facility?
Tom Muka: Chlor-alkali manufacturing involves the production of chlorine and alkali, typically as caustic soda (NaOH) via the electrolysis of sodium-chloride brine. Chlorine and caustic are industrial chemicals used as raw materials by a variety of industrial and consumer-product industries.
There are three major chlor-alkali technologies currently available. The Niagara facility uses a process known as membrane-cell technology, which produces high-purity caustic and chlorine without the use of mercury or asbestos.
ER: What are some of the potential environmental impacts of a chlor-alkali plant?
TM: A potentially significant environmental impact involves disposal of non-condensable chlorine-processing gases. Most of the chlorine gas is liquefied for shipment to customers, but a portion, a gaseous mixture of chlorine and various inert gases, cannot be converted to product. These gases are commonly known as “tailgas.”
ER: Prior to the new recycling system, what was the plant’s approach to the disposal of tailgas?
TM: Tailgas used to be considered a waste product that had to be neutralized by mixing or scrubbing the gases with a caustic solution, treated, and then discharged as sodium-chloride brine into the effluent stream that is headed for the city’s wastewater-treatment facility.
ER: What was the primary motivation for coming up with the new system?
TM: Tailgas contains chlorine, which can be recovered and sold. The old system also required the use of treatment chemicals and the consumption of other valuable materials — such as caustic soda and hydrochloric acid — that could otherwise have been sold as products. So disposing of the tailgas represented a significant loss of valuable product. In addition, the previous disposal system was costly to operate and generated a significant waste stream that was ultimately discharged to the City of Niagara Falls POTW (Public Owned Treatment Works). In a nutshell, we were “losing” about 1% of our total chlorine production and paying a high price to dispose of it.
ER: How was the new system developed?
TM: The Hypo Recycle Process was developed and engineered based on an understanding of the Niagara facility’s chlorine system and how it could be changed. We did engineering studies to evaluate process modifications. In addition, extensive sampling and analysis was done to ensure that recycle and recovery would not adversely effect existing product quality or process operations.
ER: What were some of the challenges the Niagara Falls plant faced in implementing the new system?
TM: Project funding is always a challenge. The total cost of the project was $6.5 million. The project scope was extensive, requiring a significant capital expenditure and additional operating commitments by Olin management. In addition, the proposed Hypo Recycle Process was new and, as yet, unproven, but sound economic and engineering principles ultimately led to project approval by the Olin board of directors. Whenever you do something new, there is the risk that it may not work as planned. In this case, Olin carefully assessed risk versus benefit, and, in retrospect, made a sound decision to proceed.
Constructing and starting the new Hypo Recycle Process was also a significant challenge. Overall, more than 60 Olin personnel participated in coordinating, designing, constructing, commissioning, and operating the new facility. In addition, detailed design and construction of the new installation was accomplished using local engineering and construction firms. At the time, it was the largest capital project undertaken by the Olin Niagara organization.
ER: What are the benefits of the new recycling system?
TM: Certain chlorine tailgas streams continue to be scrubbed with caustic, but instead of discharging the scrubbing solution, we now recover it as feedstock to produce sodium hypochlorite (bleach). Other chlorine tailgas streams are scrubbed in a separate, new system; material from this system is treated and recycled back into the manufacturing process. In this manner, 100% of tailgas value is recovered, either as raw bleach or recovered brine. Nothing is wasted.
The new system also saves salable chlorine product that was previously consumed by the disposal process. As a result, the Niagara facility realizes cost savings in excess of $1 million per year.
ER: How does the company measure the success of its environmental initiatives?
TM: Olin measures success by demonstrated results. Has the initiative achieved what it set out to do, in terms of both environmental objectives and cost-performance standards? Has the initiative supported Olin’s commitments to environmental objectives such as zero discharge? Based on these criteria, the Hypo Recycle Process has been and continues to be a success.
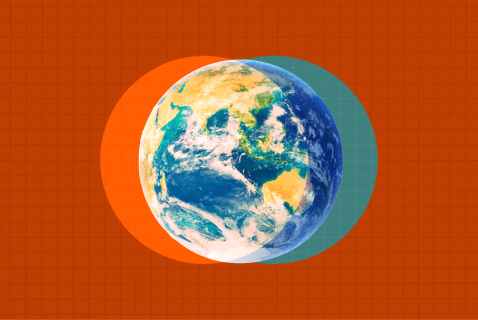