The perfect pair? Custom-fit jeans startup challenges fast fashion mindset
Instead of buying off the rack, consumers receive a bespoke pair customized for their body. Aside from eliminating inventory waste, the hope is customers will keep the durable apparel longer. Read More
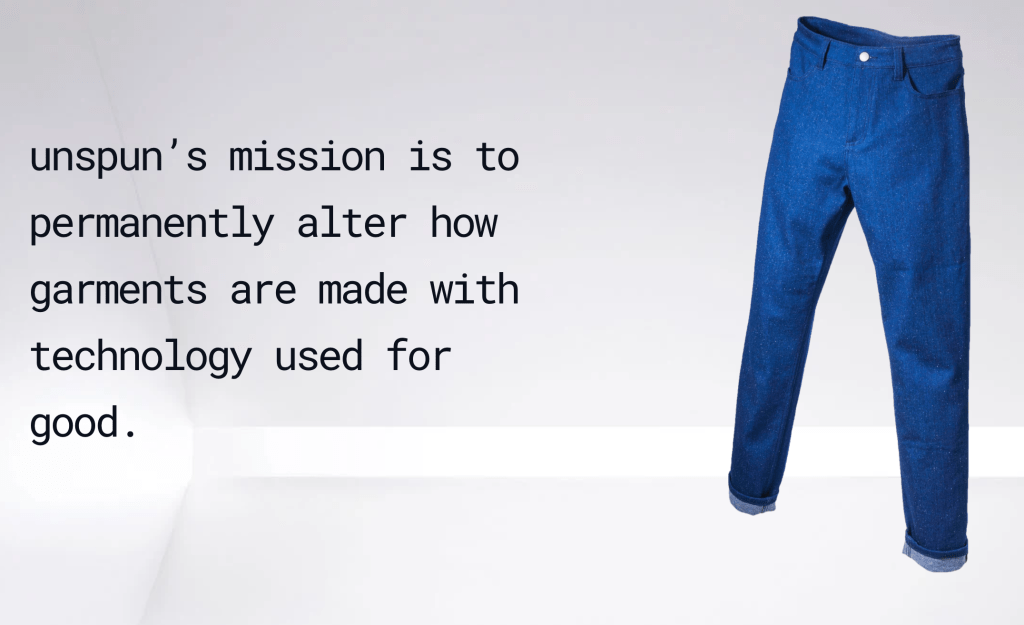
Canceled orders, excess stock, disrupted supply chains: The pandemic has laid bare some fundamental challenges with the way our clothes are designed, ordered, manufactured and sold — or landfilled, incinerated or sold on secondary markets. These impacts have been compounded by COVID-19, but the inefficient and resource-intensive apparel industry needed a redesign well before the pandemic.
One company working to do things differently is San Francisco-based startup unspun. Founded in 2017, unspun is a denim company that specializes in customized, automated and on-demand manufacturing, designing out inventory altogether. Rather than walking into a shop full of jeans in set cuts and sizes, customers instead get a 3D scan of their body — at home using a phone app and the iPhone’s built-in infrared camera or in-person at an unspun facility, currently only in San Francisco or Hong Kong. The scan is used to manufacture a customized, bespoke pair of jeans within a couple of weeks.
It’s not cheap — a pair of custom-fitted unspun jeans will set you back $200 — but like all disruptive technologies it has the potential to become more affordable over time. And while the denim might be pricey, the products’ physical quality and emotional durability encourage customers to keep their garments for longer, a tenet of circularity. Plus, if you factor in the externalized environmental cost of denim production — which unspun does — one could argue they’re a bargain (although that’s not a case I care to make during a recession).
I caught up with unspun co-founder Beth Esponnette this week to talk about her company’s role in designing a better approach to the fashion industry. The following conversation has been edited for length and clarity.
Lauren Phipps: What problem is unspun solving?
Beth Esponnette: The fashion industry has been pushed to the point of efficiency. It’s stuck. There’s a huge mismatch between what the apparel industry makes and what people buy at the end of the day. Especially now with COVID, there’s a huge problem with excess inventory. Margins are so important, and there’s not a lot of R&D budget — it’s not even 1 percent of [apparel] companies’ budgets that go to R&D — and big brands are risk-averse. They’re used to doing things the same way and incrementally improving them, but using a very siloed supply chain.
We produce clothing after someone’s purchased it — build it on-demand versus waiting for someone to show up.
Phipps: What kind of technology do you use to make custom garments for every customer?
Esponnette: There are two main pieces of tech that we’ve been focused on: the software that turns body scans into perfect fitting patterns, and hardware that takes yarn and starts to build the three-dimensional product.
Our software takes in body scan information — and not just measurements. It requires the full point cloud of someone’s body: 30,000 to 100,000 points in space, depending on the scan quality. What’s great is that you don’t lose all of the information when taking measurements around someone’s body. We build the pattern all digitally, and before we do anything physical with it, we go back and fit it on our digital avatar a few times before it’s perfect. It’s almost like we’re getting to do multiple fittings with them, and that gives us a huge advantage.
It’s automated, so once you’ve written the software it doesn’t cost anything for the program to run it and create a pattern. We’ve gotten rid of the hours of work that a tailor would be spending building a pattern.
The idea is that there’s no sewing machine or manual labor. We’re also experimenting with weaving in three dimensions and building the whole [garment] from yarn. The fit is so difficult on woven products, so if you can make something to someone’s actual dimensions and it’s a woven, then you’ve really tackled that big problem. We started with the hardware in 2017 and still haven’t commercialized on it — but hopefully we will in the next six months.
Phipps: You’re asking a lot for people to change the way they purchase. How do you get consumers to think differently about the way they buy clothes?
Esponnette: I’m excited where consumer mindsets are going. They’re starting to slow down and think about their impact in the world. The average is 84 garments purchased per year per American; it’s insane that we buy more than one product per week. I think consumers will be willing to spend a bigger chunk of their income on fewer products that will last longer and that they’re excited about. We’re starting to see that change.
When we talk to customers, it starts with the product: fit, options, etc. If you build something after they purchase it, it can be perfect for them. It can be everything they want and customized to their body. Then the conversation often goes into other excitement. We don’t have sizes, which is more inclusive. We don’t have inventory, which decreases waste and emissions.
It’s not the reason people walk in the door: It’s about not having to shop and finding the perfect fit. But we do it for sustainability and the greater mission of reducing global carbon emissions by 1 percent, which is our main North Star.
Want to learn more about unspun and the future of fashion? Esponnette will speak about the potential of custom, on-demand manufactured apparel this month at Circularity 20. Listen in (for free!) at 10 a.m. PDT Aug. 25 and register here for the event.
This article is adapted from GreenBiz’s weekly newsletter, Circular Weekly, running Fridays. Subscribe here.
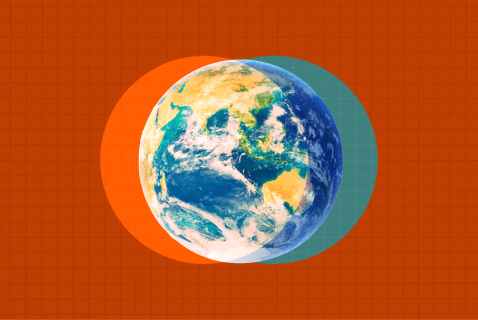