The Power of One: Union Pacific
Mike Iden has spent a lot of time at Union Pacific working on making locomotives more efficient as well as reducing their emissions, including developing new low-emission engines and redesigning containers to reduce drag. Read More
“The Power of One” is a series of stories about people who have helped their companies become more sustainable. (See earlier stories on UL Environment and eBay.) They can’t do it alone, of course. But by coming up with a good idea, enlisting the help of others and making persuasive arguments, one person can change a company and, sometimes, more. Today’s story is about an invention that is making its way from one man’s garage onto the tracks of America’s biggest railroad, the Union Pacific.
Mike Iden is all about saving energy, whether he’s on the job — as the general director of car and locomotive engineering for the Union Pacific railroad — or on his own.
He’s the kind of guy who, when he’s driving his car, slows down long before he reaches a red light and starts up slowly afterward because he knows that sudden stops and starts waste fuel.
“You’re driving like you’re running a train,” his wife sometimes tells him.
“Thank you, dear,” he replies.
Saving fuel is a big deal at the Union Pacific, whose trains have been carrying freight across the western Union States since Lincoln was president. During the first nine of months of 2010, the company spent $1.8 billion on fuel; that’s about 20 percent of its costs. What’s more, because freight railroads compete mostly with trucks, they like to boast about their fuel efficiency. “Freight trains are almost four times more fuel-efficient than over-the-road trucks and have less impact on greenhouse gas emissions,” the Union Pacific says.
I met Mike Iden last spring when I visited Union Pacific in Omaha to report a story for FORTUNE. (See Union Pacific railroad builds the U.S. economy at fortune.com.) Mike, who is 60, has been in the railroad industry for more than 30 years; he’s got a B.S. in mechanical engineering from the Milwaukee School of Engineering and a business degree from Northwestern. He’s spent a lot of time at the UP working on making locomotives more efficient — the company owns about 8,000 of them — as well as reducing their emissions.
Mike is especially proud of his role in inventing and developing what’s called the “Genset” locomotive. That’s a breakthrough innovation for the UP — a multi-engine, ultra-low emitting diesel locomotive that’s used in railroad yards in cities like Los Angeles, Houston and Dallas where pollution is a problem.
But he got my attention when he told me about another innovation that he’s developing — the one that began in his garage. It began when he wondered if anything could be done to reduce the aerodynamic drag that is created by “double stack” containers, one on top of the other, that sit right behind the locomotive. Here’s a photo of the “double stack” containers behind a locomotive.

His first idea was to clamp a nose cone to the top container, so it would move more easily through the air. That didn’t work well. “Even though there was a reduction in drag which would get you some fuel savings, it wasn’t a lot,” he says.
Plan B was a concept that he now calls the “aero wedge.” His idea was to lock an empty wedge-shaped container to the bottom container. To test it, he built a scale model out of wood that he bought at Home Depot. Here’s a look at the model, seen in Mike’s driveway:

By this time, Mike had enlisted a key ally, an executive named Wayne Kennedy who works in a group known as “continuous improvement.” Kennedy’s team had tested the nose cone idea that didn’t work out; they also had a relationship with engineering professors at Brigham Young University, whose grad students were eager to work on real-world projects. The Union Pacific again turned to BYU, where grad students tested aero wedge using computer simulations, and then put a 1/129th scale model through a wind tunnel there.
The fuel savings appeared to be meaningful, but a new problem arose. Says Mike: “The first questions that people in the company had was, why would we give up a revenue box on the train?” It turns out, though, that there’s often at least one empty container on a train, so if the cars could be arranged properly, the wedge would not displace a full container.
The next step was testing the wedge on a real train. Wayne Kennedy came up with $20,000 from his budget. UP employees located a scrap container at a repair shop and turned it into the wedge. Then they shipped it to a testing center in Pueblo, Colorado, run by the American Association of Railroads, which put the wedge behind a locomotive on a seven-mile test track, below.

The UP hasn’t decided yet whether to deploy the wedge, but it’s looking good. The company has to estimate whether the costs of building and deploying wedges will be more than offset by the fuel savings, now and in the future. It’s possible that the company would decide to license the idea to other railroads, too.
Either way, though, there’s something to be learned from Mike’s approach. He started with an idea, tinkered, collaborated, got help from a university and then took the project to an industry-run testing center. And he’s not done yet; recently he flew from Omaha to a Chicago on a regional jet and began noticed the design of the plane’s wings. “I’m working on a change to the configuration that I think could make it better,” he says.
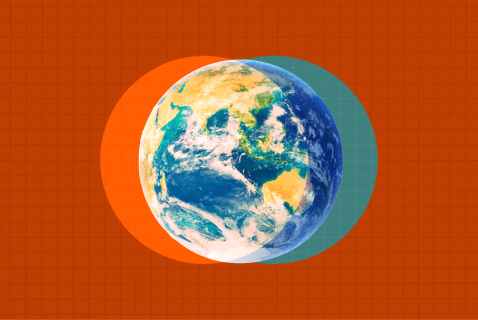