Prius Envy and the Greening of Wal-Mart: A Blind Spot for the Human Cost
The corporate rush to environmental stewardship has pushed related workplace safety and health issues to the sidelines. Yet a recent report critical of Toyota highlights the danger of viewing environmental concerns without considering the human toll. Read More
Can it be that our green heroes Leonardo DiCaprio and Brad Pitt care about the cachet of owning a Prius but not about the abused workers making these feel-good cars?
A report from the National Labor Committee released earlier this month alleging abusive working conditions in Japanese Toyota Prius plants provides a much needed jolt to the environmental and business communities about the danger of viewing environmental concerns as separate from human concerns.
Supervisory workers in Japanese Pruis assembly plants are overworked to the point of exhaustion, and sometimes, death, the report said. One-third of assembly line workers are poorly paid temp workers. Its parts supply chain is “riddled with sweatshop abuse,” including trafficking of tens of thousands of foreign guest workers, sometimes working 16-hour shifts. The report tweaks celebrities for endorsing the Prius without considering the human capital aspects behind the way they are produced.
The urgency with which environmental groups, Al Gore, and the media have touted climate change as the defining issue of our time has resulted in related workplace safety and health issues getting brushed aside. Toyota, along with GM and Ford were also cited in an extensively researched story from the Wall Street-oriented magazine Bloomberg Markets in December of 2006. The story linked slave labor conditions to production of pig iron used to produce steel that ends up in their vehicles. That’s right — slave labor in the 21st century.
But it’s not just Leo and Brad: There is culpability here for all of us, but I want to focus on corporations and environmental groups.
Corporations are still largely reactive on social issues. For more than a decade, labor and social responsibility advocates highlighted abusive working conditions of global suppliers providing goods for Gap, Nike, Wal-Mart and other corporate icons. Despite evidence that similar conditions existed in other industrial sectors, Corporate America continued to basically turn a deaf ear. National Labor Committee research touched off allegations back in 1996 that Kathie Lee Gifford’s clothing line sold at Wal-Mart was made under sweatshop conditions, resulting in worldwide front-page headlines, the involvement of then-Labor Secretary Robert Reich and a presidential commission to improve supply chain working conditions.
Other sectors such as electronics largely ignored this loud warning signal until they too were implicated following activist research in 2004. Suddenly, a few months later, the electronics industry got religion and developed a common code of conduct for their supply chain that is only now being seriously implemented.
The largest and most well funded U.S. environmental groups focus too narrowly on the environmental implications of broad social issues. It’s hard to find substantive concern about worker safety in the agendas of the Natural Resources Defense Council or Environmental Defense Fund (EDF), two heavyweight groups helping Wal-Mart fulfill its green agenda. They should be concerned about worker exposure to cadmium leading to kidney failure at Chinese battery factories serving the U.S. market, or lead solder inhaled by workers in Thailand who make components for computers or video games. Protecting the health of supply chain workers should be a prominent part of their agenda.
Yes, it’s great that Wal-Mart has made a raft of commitments to reduce waste and increase energy efficiency, but many of those promises have worker safety implications the environmental groups and company seem willing to ignore. The strategy involves using the size and influence of Wal-Mart’s buying power to green its supply chain. It sounds good until you factor in the business realities.
EDF says it will “focus on creating a Green Company Program to improve environmental performance at the 30,000 Chinese factories that supply Wal-Mart and on building a purchasing system that rewards suppliers with environmentally preferable products.” But who is going to pay for this and what’s the incentive to act?
Domestic and foreign Wal-Mart suppliers often act out of fear, not goodwill. Fast Company has profiled domestic suppliers like Vlasic pickles and Huffy bicycles, both of which suffered from the company’s relentless low pricing demands. It’s a considerably more difficult expectation that thousands of suppliers in China will go solar or clean up wastewater discharged while making low-priced goods for U.S. consumers. It’s hard to imagine these suppliers greening through some kind of reward system without a fundamental transformation of the low pricing model.
How will EDF and Wal-Mart coax suppliers into paying for clean up when they are already being squeezed by the company’s buyers to produce goods at rock bottom rates that perpetuate abusive working conditions? In January, CEO Lee Scott discussed greening the company’s supply chain and said the company “will favor — and in some cases, even pay more — for suppliers that meet our standards and share our commitment to quality and sustainability.”
This implies the capital costs of cleaning up will be borne by suppliers. If that is all the company can offer, it is not going to work. Wal-Mart often expects suppliers to cut prices annually or risk losing contracts, according to Fast Company magazine. What if a factory owner in China can bear the cost to retrofit factories but Wal-Mart decides to pull the contract and source from Vietnam the next year because labor is cheaper?
The take-no-prisoners business model comes up smack against the laudable desire to clean up factories. Alexandra Harney’s new book, “The China Price,” profiles an unusual factory owner in China who refuses to let Wal-Mart executives into his facility because he feels they are only interested in getting the lowest price.
Is it too much to expect Wal-Mart to deal with labor and green issues at once? U.S. industry was able to deal with these issues simultaneously when production was domestic; companies have the same responsibility to ensure that the conditions under which their goods are made in a global supply chain are in compliance with labor and environmental laws. It is appalling that U.S. companies have pursued the global outsourcing of labor without insisting that our hard-won rules of workplace safety and fairness be applied to suppliers. And we all play a role: Mainstream investors demanding perpetually high earnings and consumers demanding low prices place huge pressures on companies trying to play by the rules.
So before we wax poetic about solar panels in the way we have for the Prius, remember that solar production involves some nasty stuff. The Washington Post recently reported that a supplier to solar panel provider Suntech Power dumps poisonous silicon tetrachloride, a byproduct of polysilicon manufacturing, onto fields in Henan Province in China rather than recycling it. Residents report that nearby crops are failing and air emissions from the facility make it hard to breathe.
Memo to self-styled green venture capitalists: Could we please see the line items in your budget for ensuring worker health and safety when your solar start-up scales up and moves production to Asia? Is management staff paying attention? How often are factories inspected? Are you willing to invest in safety for the human beings in your supply chain?
The bottom line: For CSR and the green technology juggernaut to have real credibility, companies must insist on best environmental practices in the rush to new energy solutions, equal consideration for the well-being of workers by enforcing best labor practices, and public disclosure of progress on both fronts.
Conrad MacKerron is director of the corporate social responsibility program at As You Sow Foundation, which uses dialogue and shareholder advocacy to promote better social and environmental policies at publicly traded companies. He is author of “Business in the Rainforests: Corporations, Deforestation and Sustainability” and a former Washington Bureau chief for Chemical Week.
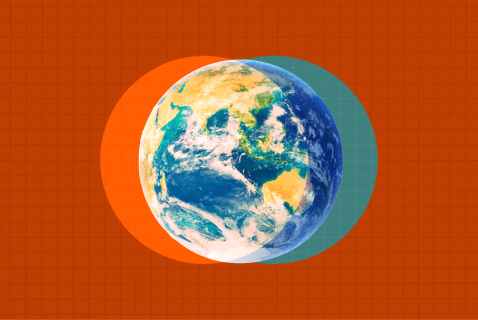