This quiet innovation is changing the world of plastic
Bunzl explores how conventional plastics are bending and adapting in a renewable direction. Read More
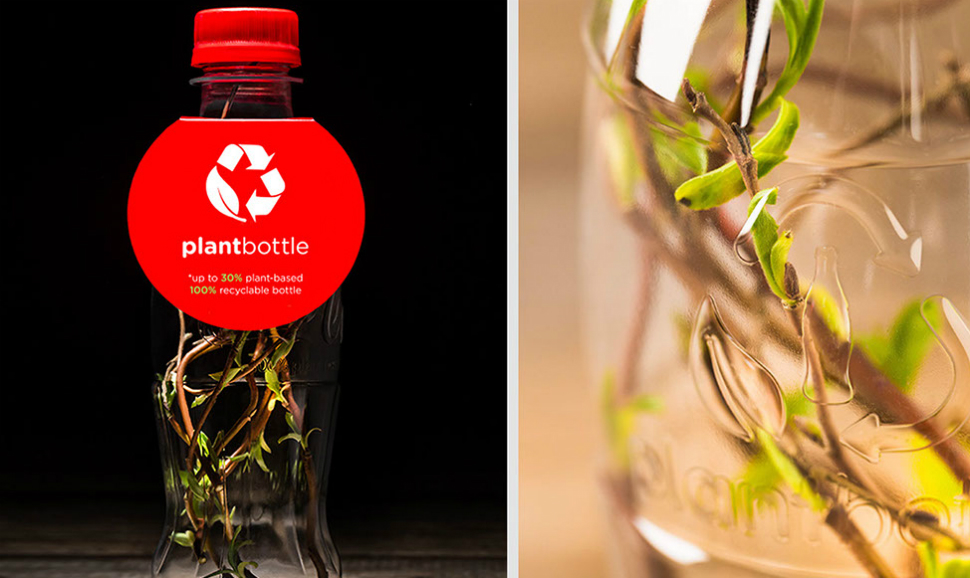
When it comes to understanding the world of environmentally friendly packaging, it is easy to become lost in the ever-expanding repertoire of biodegradable, degradable, compostable, Oxo-biodegradable, bio-derived and renewable packaging. Although these terms do mean slightly different things, they are variations on a central theme: shifting conventional, non-renewable fossil-based plastics into the renewable resource arena.
Excitingly, there is now a new, game-changing kid on the block, not only in addressing the limitations of the above material types, but also making it much easier to understand exactly what makes this material better for the environment. Although referred to as a “new kid,” this material actually has been around and used in food-based packaging for a while, but only recently has entered into the disposable packaging market.
The ‘”drop-in” bioplastic (also known as bio-based) looks like, functions and feels just like a conventional plastic. Importantly, and as the name suggests, drop-in bioplastics are like conventional plastics in that they are not biodegradable or compostable but are instead fully recyclable. If you are already confused, hang in there as this material is not as complicated as it sounds.
To understand what makes drop-in or bio-based plastics different for other “bio” plastics and an important leap forward in the evolution of plastic production, we first need to consider how plastics are made and disposed of.
How are conventional plastics made? Putting it simply, crude oil is extracted from the earth and sent to an oil refinery where it undergoes a process called distillation. This is where all the various compounds in the oil are extracted to be made into various products, including several types of plastic.
It is well understood that this process causes environmental damage and is inherently unsustainable, from the non-renewable resource that provides the raw material, to the CO2 added to the Earth’s atmosphere. and the waste created from plastics that end up littered in the world’s oceans and on land.
However, drop-in or bio-based plastics are positively changing the environmental impact of plastic production and use. These plastics are manufactured from renewable biomaterials such as corn and sugar cane. Through a process called fermentation, the starch is extracted from the crops and used to create a “drop-in” replacement polymer for the oil-based polymers used in conventional plastic production.
This process sounds like and is very similar to the way in which PLA, a compostable and biodegradable plastic material, is produced. However, there is a crucial difference. Drop-in or bio-based plastics are not compostable or biodegradable. They are, in fact, fully recyclable and have been designed to “drop-in” to the existing recycling systems without disrupting the quality or financial value of the recycling stream.
A key challenge of compostable and biodegradable plastics is that composting infrastructure is limited, making it difficult to ensure this material ends up being processed as intended at its end of life.
Drop-in or bio-based plastics have been designed with the existing waste management system in mind, making responsible disposal and end of life treatment straightforward. The Coca-Cola PlantBottle and Huhtamaki’s Future Smart disposable product range are excellent examples of drop-in or bio-based plastics in action.
A smart infographic from the Polymer Innovation Blog clearly shows the renewable material benefit of drop-in, bio based PolyEthylene (PE), including how one hectare of land can produce three tonnes of bio-based plastic. Of course, with all bio-based materials, it is very important to know where the crops used in production are grown and managed. This in itself also must be sustainable.
However, drop-in/bio-based plastics represent an important innovation in plastic production, not only from the shift to renewable feedstock, but also from viewing plastic production and use as being part of a boarder “system” with various components, from production through to disposal. This new material so far has seamlessly “dropped in,” bringing improved environmental benefit with many of us being none the wiser.
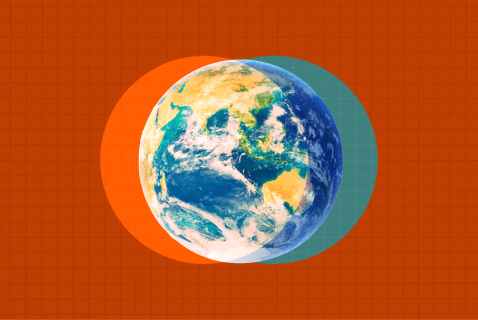