This Aussie startup backed by Lululemon has grand plans for the plastics used in fashion
Samsara Eco says it's the first to infinitely recycle nylon 6 using enzymes, a move toward its ambition to erase the need for virgin fossil fuels in plastics and fashion. Read More
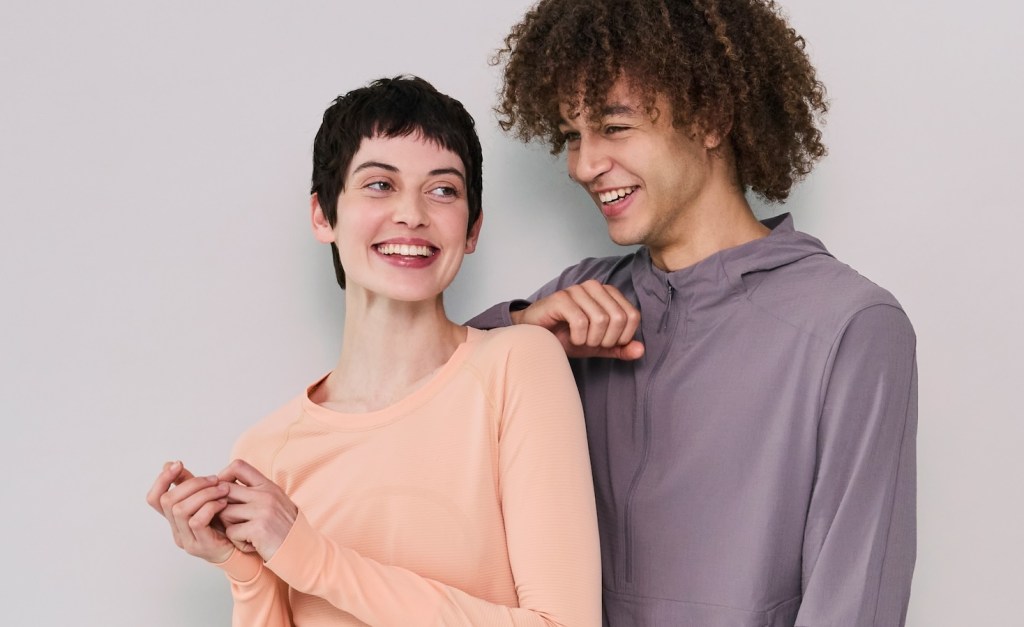
Australian startup Samsara Eco is the first to use enzymes to recycle the nylon popular in intimate apparel into raw materials for new fibers. The company Dec. 10 announced an advancement to “infinitely” recycle nylon 6 textiles, popular in hosiery, as well as other apparel and cars.
It applies technology that can transform the plastics industry and eliminate virgin petroleum from supply chains, according to founder and CEO Paul Riley. Samsara Eco’s special promise is to recycle tricky mixed and colored materials, including in synthetic fabrics.
“Our ambition is to be able to resolve all of those polymers that go into those garments, provide true circularity, provide them for recycling, and hopefully we never have to see fossil fuels in plastics again,” Riley said.
Fiber-to-fiber recycling is a $1.5 billion opportunity in the U.S. alone, according to a May report by Fashion for Good, “Sorting for Circularity.”
Samsara Eco has raised some $165 million in funding, including a series A round in June. The seven investors included Lululemon and Hitachi Ventures. Main Sequence, the venture fund of Australia’s national science agency, the Commonwealth Scientific and Industrial Research Organisation (CSIRO), has been a major supporter.
The news builds on Samsara Eco’s efforts to recycle hard plastics and polyester textiles, transforming an annual 1.5 million metric tons of plastic by 2030.
Earlier work with Lululemon
“Samsara is a valued partner of ours and it’s great to see the momentum they continue to make in nylon,” said Rebekka Schultz, Lululemon’s global sustainability and impact communications manager.
The activewear giant has partnered with the startup on recycling a different type of nylon, also known as polyamide. In February, that resulted in a long-sleeve “Swiftly” model shirt made of 90 percent nylon 6,6, a different type of nylon, recycled from textiles.
Samsara Eco in August partnered with Nilit of Israel to build in Southeast Asia the first factory to recycle nylon 6,6 from textile waste, due to open in 2026. Nilit’s products include Sensil nylon, a Spandex alternative made from nylon 6,6.
Samsara Eco is also building a $25 million research and development plant near Canberra, Australia, due to open next year.
How Samsara Eco stands apart
Samsara Eco of Sydney launched in 2021 to commercialize a technology developing at the Australian National University. Researchers used machine learning to rapidly develop enzymes to “eat” plastics, breaking down their polymer chains.
“What excited us the most was that it was an opportunity to address multiple polymers,” Riley said. Legacy mechanical recycling, by contrast, can only handle one material at a time. Samsara Eco, on the other hand, plans to use waste from one process to feed another.
Its custom enzymes “eat” one polymer at a time and “spit out” any other material. Recycling the polyester in a nylon-polyester blend, for example, would leave nylon behind. But the company could deploy a different enzyme to recycle that nylon. “Now, not only does that open up feedstock, and eliminate waste from your process, (but) it provides true circularity,” Riley said.
“So we’re looking at infinite recycling, true circularity across fashion and packaging, and that’s an important thing to note that there is no difference in our molecule to a fossil fuel molecule.”
The competitive landscape
That echoes the pitch of textile-to-textile recycling startup Carbios of France, which has raised $77 million. It revealed Oct. 29 what it called the first biorecycled white polyester T-shirt. Carbios hopes its custom enzymes will eventually recycle nylon at scale, too.
Samsara Eco retains an advantage of a pre-processing step it patented that transforms dense plastic into a state the enzyme can break down in minutes, not days, Riley said.
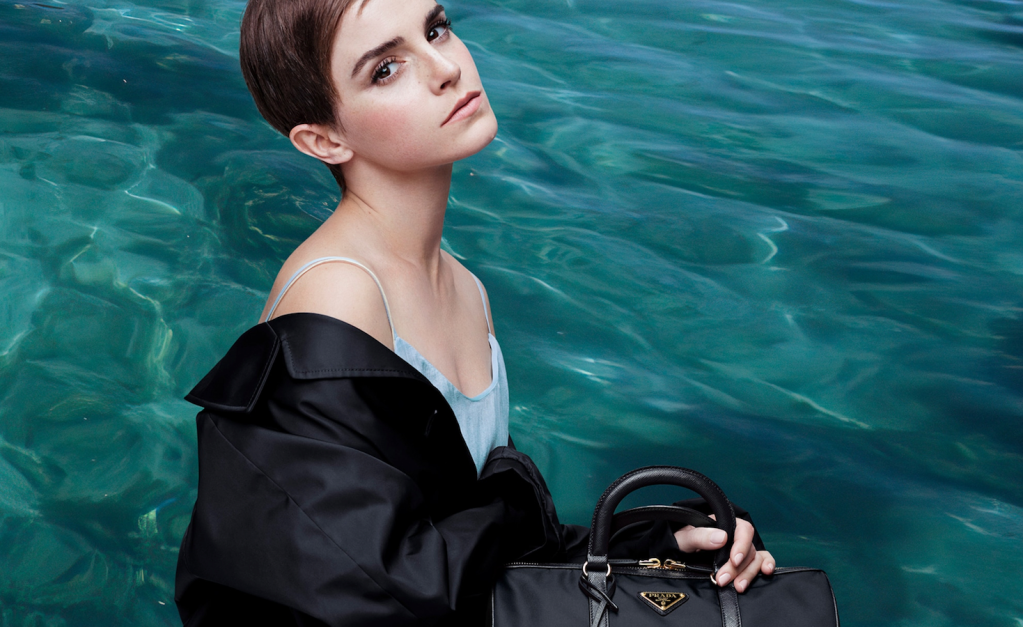
Other companies have been recycling nylon 6 chemically, without enzymes, for more than a decade. Among them, Aquafil of Italy has recycled nylon 6 fishing nets, carpets and fabrics into its Econyl nylon since 2011. Some Prada accessories, Speedo swimsuits, Burberry outerwear and Levi’s denim all feature Econyl.
Patagonia, The North Face and Uniqlo use nylon 6 recycled chemically from fishing nets by Tokyo-based Toray.
And in January, BASF and Inditex announced a pilot to recycle nylon 6 from textiles. The material, loopamid, appears in a jacket by Zara, which Inditex owns.
However, Samsara Eco’s process has a lower greenhouse gas and materials footprint than existing recycling technologies, according to Riley. Mechanical recycling, by contrast, downcycles products that eventually go to landfill. And chemical recycling, typically used for nylon, fails to be circular as well, he said.
“We’re not creating some high pressure, high heat process, like pyrolysis,” Riley said. “We’re not creating oils. We’re not creating any other funky products and trying to have offsets to beef up our LCA [lifecycle analysis]. It just turns back into the original product and taps straight back into the supply chain.”
Building recycling systems
Advocates of building circular systems for fashion agree that for innovative materials to gain a toehold against virgin ones, they must collaborate with players across the industry.
Samsara Eco tacks another advantage in terms of feedstock, according to Riley. It plans to source synthetic textiles from an enormous volume available from textile manufacturing partners in Southeast Asia.
The company is also “talking closely with polymerization partners in Europe and in North America as well across better packaging and fashion,” he added.
“Each of the technologies scaling today require partnerships with up- and downstream processors that are at the appropriate level of commercialization,” said Sarah Coulter, Accelerating Circularity’s U.S. program director.
“The opportunity in athletic apparel and automotive is huge, and Samsara is poised to capture a significant part of the market,” she added.
Samsara Eco is also a recycling partner in the “Building Markets” trials of Accelerating Circularity, a project exploring how to mainstream textile-to-textile recycling. The New York City nonprofit brings together various players in the apparel industry to advance circular practices.
Polyester recycling has become a crowded space, so breaking into nylons is the next logical market, according to Marcian Lee, an analyst in materials and manufacturing at Lux Research in Singapore. That makes sense because although nylon is only 5 percent of the fiber market, it’s higher value, he added. “This would be good for chemical recycling, but the small volumes also mean that it will be that much harder to collect nylon textile waste for recycling.”
[Connect with the circular fashion community and gain insights to accelerate the shift to a circular economy at Circularity, April 29-May 1, Denver, CO.]
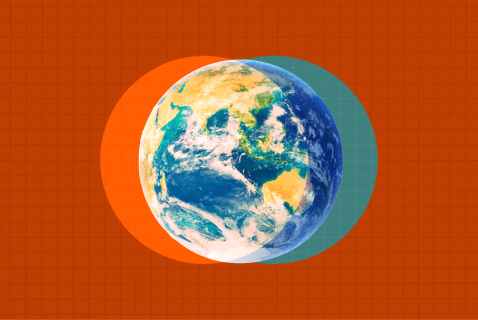