Shape means strength, from a Boeing Dreamliner to a Bone Chair
Vehicle makers cut costs — and the fuel needed to move a plane or car's mass — with software that uses biomimicry principles. Read More
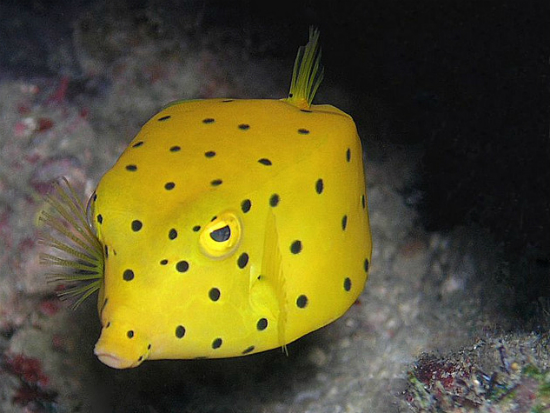
If you ride in a car or plane today, you may be the unknowing beneficiary of planet-helping biomimetic design. Designers and engineers can reduce the size or weight of many vehicle parts for greater efficiency or cost savings.
This shape optimization is a major task in engineering. Making things lighter, stronger and faster long has been a goal in manufacturing, but engineers are increasingly employing biologically inspired algorithms to design many objects around you.
The better integration of three methods has fostered this still-growing tide of bio-inspired design objects: biologically inspired algorithms for analysis and shape iteration, computer aided design and additive manufacturing.
Shape is strength
Some software programs now in use enable engineers to design as nature would, by testing many options based on performance under a wide range of stresses. Natural selection can be mimicked, and material put where the stresses are. D’Archy Wentworth Thompson noted this phenomenon in bone in “On Growth and Form” in 1917.
Put another way, shape is strength. One natural example is the tree that grows cells in the right place to resist bending. Like the I-beam, which needs little material at its waist because compressive forces equal tensile forces there, these new material-reduced parts contain matter only where it is needed based on the digital stress analysis of computer aided engineering. Additive manufacturing widens the production options for what are usually more complex shapes.
What is relatively new is the use of nature-based algorithms to produce the organic shapes. Morphogenesis is the term used to describe this iterative process of creating shapes by contextual recipes. These recipes do not just graphically represent the forms, but actually create them.
Lighter for more efficient flight
One hundred fifty components in the airframe of the Boeing Dreamliner 787, or about 10 percent of the total screened, were designed and made lighter by engineers using the OptiStruct software program, part of Altair Engineering’s CAE software suite Hyperworks. These components are throughout the frame, and it is hard to find a place where material savings were not achieved: floors, fuselage, tail and wings. Altair claims that using OptiStruct has saved 650,000 tons of material and 900,000 tons of CO2 worldwide. This kind of topology optimization also was used in the wing ribs of the Airbus 380 aircraft of the European Aeronautic Defence and Space organization.
The procedure works like this: You import a CAD drawing into the program and a design “space” is created for the object, within which various constraints and objectives are established. It might be where the object is supported, what amount and direction of force is directed at it, or how much movement or deflection you wish to allow for. When these parameters are set, the program shows you where material is not under stress and therefore not needed. You can then revise this form, given what you know about manufacturing techniques, aesthetics and so forth.
While a lighter hinge bracket or floor brace might not be the sexiest, its contribution to cumulative energy and material savings in an aircraft is significant. Little things do add up. The green results of reduced material and weight in a vehicle have been well demonstrated by the Rocky Mountain Institute and Amory Lovins in the book “Reinventing Fire.”
All sorts of design possibilities for downstream cost savings open up as a result of these basic changes in shape, size and weight. If floor braces aren’t sexy, then you may want to wait for the rollout of an Alfa Romeo sports car now in the concept phase. The automotive manufacturer used OptiStruct to optimize the double wishbone front suspension system in this car. (OK, so maybe the suspension won’t be the sexiest part of the car.)
Efficiency bred in the bone
OptiStruct is based on the growth pattern of bone, and was principally developed by Jeff Brennan, now CMO of Altair. Brennan was a master’s student at the University of Michigan studying biomedical applications under engineer Noboru Kikuchi, who wanted to know how to encourage bone growth for osteoporosis patients.
Brennan thought that the mathematical growth patterns seen in bone could be applied to static structures and got Kikuchi to help translate the mathematical principles to software. He took his idea to Altair Engineering in 1992.
CEO James Scapa saw the potential for this new way of designing products and coupled it with a pay-per-use business model to help grow a company that now employs over 2,000 people in 40 offices in 20 countries.
Another bio-based algorithm — a precursor — is Soft Kill Option software. First demonstrated in the early 1990s, SKO is a structure optimization algorithm that simulates bone mineralization by varying Young’s Modulus according to a calculated stress distribution.
Young’s Modulus is a measure of stiffness of an elastic isotrophic material where stress (force per unit area) along an axis is divided by strain (ratio of deformation over original length) for most solid bodies. It was developed by Claus Mattheck of the Karlsruhe Research Centre, author of the BID classic “Design in Nature: Learning from Trees.” Mattheck and his colleagues have been studying shape optimization of engineering components based on nature since the late 1980s.
DaimlerChrysler AG used this bio-inspired algorithm for another concept car, the Mercedes Benz bionic car (also known as the boxfish car), in 2005. The company used SKO software to design the struts of the internal car frame. Engineers of Adam Opel AG used SKO to make their automobile 30 percent lighter overall, with an engine mount that was 25 percent lighter and yet 60 percent more stable.
This program also has been used in more aesthetic pursuits. Product designer Joris Laarman of Amsterdam, Netherlands, used SKO to design his innovative Bone Chair in 2007. The chair’s organic form came from its structural requirements, and not from the whimsy of its designer. First shown at the Milan Furniture Fair, it later was acquired by New York’s Museum of Modern Art after being shown in the 2008 show “Design and the Elastic Mind.”
Such techniques are used increasingly in architecture as well, and deserve their own blog item. They have brought the typically separate tasks of design and engineering analysis closer together. Architecture professor Peter Macapia of LabDORA and the Pratt Institute in New York City explained the benefit of this type of tool in an Altair company brochure:
“… it’s not telling you how to solve for the design of the material, but rather it’s presenting a diagram of forces and telling you what it would mean using one type of material rather than another. The fact that you can constantly specify the material and update the form you’re working with is a real asset in the program.”
More innovations will come as the integration of these techniques becomes more sophisticated and user-friendly. Saving material, and the energy needed to harvest or mine, fabricate and transport it, is one of the most basic resource-saving techniques available to us, and more and more this is being brought to you by nature. This is already doing a lot of good for our planet. You just may not notice it.
Top image of yellow boxfish by Adrian Moody via Flickr.
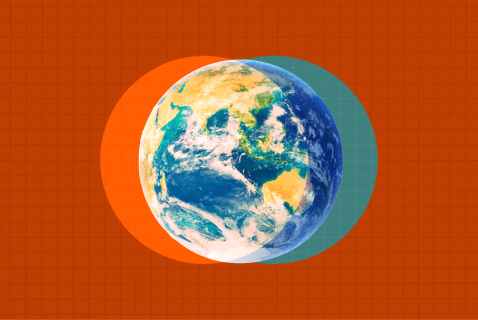