Sustainability and pallets: Making change for the long haul
Corrugated cardboard is far lighter than wood, plus it simultaneously saves money, reduces carbon footprints and advances zero-waste goals. Read More
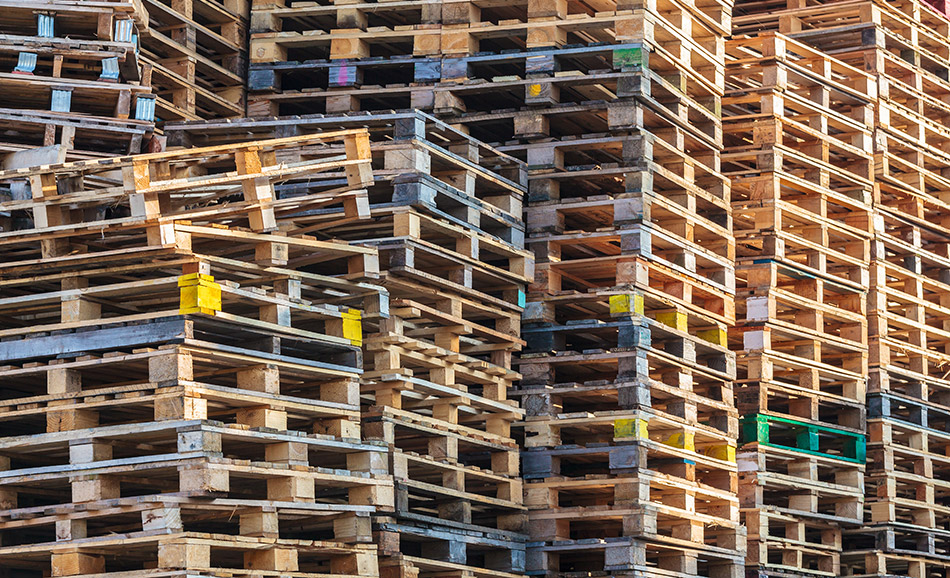
Maybe it’s time for corporate sustainability to get a bit more boring. Rightfully so, bold commitments by leading companies to 100 percent renewable energy or zero waste garner headlines. But the durability (or perhaps the sustainability) of sustainability comes from business practices that reduce environmental impacts while saving money.
Sometimes these measures are not especially sexy.
Consider the lowly shipping pallet. Millions of times a day, companies receive and send goods loaded on pallets. Overwhelmingly, these pallets are made of wood and weigh about 50 pounds. Logisticians know that space + weight = cost; sustainability experts know that space + weight = emissions.
What we have, therefore, is an opportunity for durable, sustainable change. Each year an estimated 10 billion loaded wood pallets are shipped just in the United States. In pallet weight alone, swapping out wood for corrugated pallets could reduce the amount of annual U.S. trucking weight by as much as 400 billion pounds, thereby reducing carbon dioxide emissions (CO2e) by millions of metric tons annually.
As sustainability leaders such as IKEA have demonstrated, companies can direct suppliers to ship on lightweight, recyclable corrugated cardboard pallets. Doing so will save money, protect employees, reduce carbon footprints and advance zero waste goals.
Pulling their weight
Before 2009, IKEA used almost exclusively wood pallets. Today, more than 98 percent of its global inbound and outbound shipments are on corrugated pallets, cutting CO2e by more than 550,000 metric tons since 2012. Based on public and company reports, we estimate that IKEA has saved billions of dollars through its global “Handling Material — No Wood” program, largely by shipping an estimated 1.44 billion fewer pounds each year, eliminating wood pallet disposal and realizing corrugated recycling revenue.
From 1991 to 2010, General Motors required suppliers to ship to its facilities on corrugated pallets. The program ended in the United States (but continued in Mexico) when a multinational wood pallet company convinced GM to switch to extra-heavy (70-pound) wood pallets. It seems that GM did not pay close attention to the impact the change would have on emissions — it was a different time — and/or failed to calculate the true enterprise cost of switching back to wood pallets.
Fortunately, the precedent- and game-changing numbers remain intact: 62 GM facilities achieved “zero waste” status during this time frame. GM also reported more than $2 billion in recycling revenue; revenue that surely has dropped off since the program’s termination.
Most important, as GM proved for 19 years, America’s companies (and universities, hospitals and government agencies) have a choice when it comes to what pallets are delivered to their facilities. In many cases, turning the switch to corrugated requires little more than a letter to suppliers, or adding a few words to a supplier protocol or similar guidelines.
The case against corrugated
Leading U.S. retailers have argued that corrugated pallets are not sufficiently strong. It is true that corrugated pallet quality can vary and some applications are not suitable, but those issues are easily handled in spec-writing. The fact that IKEA ships and receives substantial loads on 36 million corrugated pallets per year — spanning five continents — belies the “sturdiness” argument.
Others cite the costs that come with changes to materials handling and racking practices. This is often true, and IKEA can attest that making such changes was a prudent investment.
Companies often point to per-pallet cost comparisons of wood versus corrugated, but a more complete analysis would factor in fuel savings, space optimization, recycling revenue, reduced injuries, operational efficiencies, less product damage, disposal costs and perhaps even carbon value.
Finally, major retailers fairly point out that they reuse wood pallets for shipments downstream. But that does not change the fact that it requires one truck to deliver 1,800 corrugated pallets to their point of use, but 4.5 trucks to deliver the same number of wood pallets; that it takes one truck to move 400 wood pallets away from the store post-use versus tossing corrugated pallets into the bailer; and that pallets remain one of the largest components of landfill waste.
Who needs retail?
A disappointing but honest appraisal is that even leading sustainability retailers such as Whole Foods are committed to systems that force Seventh Generation, General Mills and other sustainability leading suppliers to ship on wood pallets — and that’s unlikely to change anytime soon. But beyond retailers, sustainably minded companies can look upstream to advance carbon reduction and zero-waste initiatives.
Could Tesla revive the GM supplier directive? Could General Mills direct that the tens of millions of empty corrugated cereal boxes delivered to its factories each year be shipped on corrugated pallets? Could Seventh Generation ask that empty plastic containers come on corrugated pallets?
And, maybe even easier, could sectors such as hospitality and medical facilities that rarely ship downstream save money and reduce upstream footprints by similarly requesting that suppliers use lightweight, recyclable pallets?
Change is hard. It’s also the essence of corporate sustainability. Leading companies literally are changing the world through responsible sourcing, clean energy use, process efficiencies and many other innovations in business practices that yield social, environmental and economic benefit. There is still much low-hanging fruit to be harvested, and the lowly pallet is still hanging on the tree, ready to be picked.
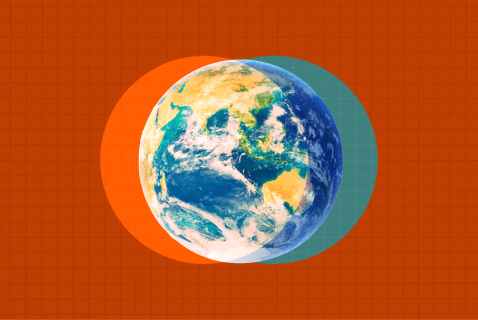