Using Recycled Shipping Containers as Building Blocks for Green Construction
Builders have crafted a full-scale model home from recycled shipping containers for the West Coast Green tradeshow and hope their work will help fuel a market for commercial construction that uses refurbished steel cargo cubes. Read More
Amid neck-craning stacks of shipping containers at an Alameda depot, a building crew has worked for the past two weeks to fashion an eco-friendly, two-story structure from five recycled and refurbished steel cubes that had been used to haul cargo.
The project by SG Blocks LLC and the design firm called the Lawrence Group will bring an 1,800-square-foot, two-bedroom, two-bath home to San Jose, where the structure dubbed Harbinger House will be the centerpiece on the tradeshow floor of the West Coast Green conference that runs from September 24 to 27.
The builders hope the project will hold not only the promise of more business for their nearly 2-year-old firm, but also help fuel an emerging market for commercial construction using recycled shipping containers.
{related_content}
Reclaimed shipping containers have been used for housing and workspace for decades, mostly abroad and often in areas where building materials are scarce. Building with containers is gaining popular currency as a timesaving, more affordable, eco-conscious building alternative to traditional construction, particularly in Europe and the United Kingdom. Earlier this summer, Travelodge opened a 120-room hotel in the greater London area built from 86 containers.
In the U.S., construction with shipping containers, called intermodal steel building units or ISBUs, has largely been residential — a situation that gives rise to ambitions for a commercial market.
“The showhouse is very cool,” said Bruce Russell, the managing partner for SG Blocks, which has worked on single-family and multiple-unit residential projects and completed its first office building last fall. “But I think the real impact we’re going to have is in the commercial segment. That’s really where the system is going to shine.”
The company’s first non-residential project, which was also the first of its kind in the United States, was a 4,322-square-foot, two-story office building for the U.S. Army. The 249th Engineer Company Operations Building at Fort Bragg, N.C., was made from 12 former shipping containers that are known in the trade as Hi-Cubes — containers measuring 9.5 feet high, 8 feet wide and 40 feet long.
![]() |
The construction project took 101 days to complete and came in at about $150 per square foot. That was about two-thirds of the time it would have taken to complete a building using traditional methods and well under the Army’s $750,000 budget for the job, according to the Army Corps of Engineers.
The construction project marked “the first time that I’m aware of that somebody designed a building using containers as building blocks to create structures that inside and out look just like any other building,” said Nathaniel Hermann, a resident engineer for the Army Corps of Engineers at Fort Bragg. Hermann enlisted SG Blocks for project and worked closely with the firm to achieve the results.
Russell and the other co-founders of SG Blocks, director of business development David Cross and structural engineer Steve Armstrong, said that’s a key point of their business. “The container does not have to drive the design,” Russell said.
The firm obtains used shipping containers, which are certified as being structurally sound as well as precise as to dimensions, and modifies them so that they are further strengthened, refurbished as needed and made architect-and-contractor ready. Preparation of the containers can be done off site to facilitate modular construction with final assembly occurring at the ultimate destination. Advance work for the showhouse was done at a depot of ConGlobal Industries Inc., a strategic partner and the container supplier for SG Blocks.
It takes an estimated 8,000 kWh of energy to melt a four-ton shipping container, about 6,500 kWh to make a ton of steel of virgin material and almost 1,800 kWh to recycle a ton of steel from 100 percent scrap, but 400 to 800 kWh to convert a shipping container into an SG Blocks building unit, according to the company and its representatives. In terms of supply, proponents of container construction estimate that there are 16 to 22 million containers in active circulation with 1 million new units becoming available each year and some 700,000 being retired. SG Blocks has its own term for recycling the containers it acquires.
“We call this Value-Cycling — making a superior building product using a minimum amount of energy,” said Russell, pointing at one of the components for the showhouse. “This was an international unit of trade and now it’s an international unit of building.”
He and other proponents of construction with containers note that the steel shipping cubes are built and maintained to withstand heavy vertical, transverse and longitudinal loads that are measured in multiple tons. With heavy gauge CorTen steel framing and sides made of 14-gauge corrugated walls that are continuously welded, the containers are also waterproof, designed to withstand severe weather at sea and on land, and are termite resistant.
“Anybody who thinks there is a code compliance issue with this stuff — they’re looking for problems,” said Hermann. “This is nothing more than a box that’s really pretty strong and that you can get economically.”
Other issues regarding construction with containers can involve aesthetics, and builders who use the steel cubes often must contend with perceptions about appearance regardless of whether designs favor an industrial high-tech look or a more traditional profile.
Members of the SG Blocks team said that communities on the whole have been supportive of their work.
However, the firm had a problem with one project. A plan to provide recycled containers for 308 units of temporary housing for the community of Whistler in British Columbia for the 2010 Winter Olympics fell through earlier this month after the company obtained some but not all of the financing for the project, leaving a reported shortfall of about $3 million. “It’s just perplexing to us,” said Russell. “We loved the project.”
![]() |
Other SG Blocks projects include work on a building for the Jacksonville Port Authority in Florida, a structure planned for a Southwestern university and a senior living community in California.
The showhouse built for West Coast Green will go on tour and is expected eventually to be available for sale. The model, which is being trucked to the site on six trailers for assembly, will include upgraded energy efficient fixtures and appliances and green design treatments from vendors for residential and commercial building.
Russell estimated the cost to build and outfit the structure at about $140 per square foot because of the amenities included for the tradeshow. He said the same house would cost about $200 a square foot if conventionally built in California or a comparable market.
West Coast Green expands its focus this year to include commercial applications and is devoting about 25 percent of its programs to the subject, said program director Karen Jackson.
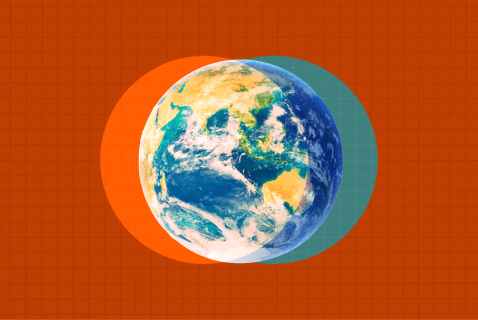