Vanderlande Industries greens the conveyor belt
For Vanderlande Industries, reducing the environmental impact of its conveyor belts and automated sorters has introduced a sea change in how it designs, sources and markets its products. Read More
For companies in the delivery industry, conveyor belts can be just as important as fuel efficiency or renewables-powered fleets.
“For distribution networks, three-quarters of CO2 emissions are generated during transportation. We address the one-quarter generated in warehouse distribution,” Gert Bossink, director of research and development for Vanderlande Industries, a provider of automated material-handling systems, told attendees at the International Cradle to Cradle conference in San Francisco last week.
Headquartered in The Netherlands, Vanderlande’s products are used in airport material handling systems — both for passenger baggage and parcels being shipped by companies such as UPS and DHL– and can be found moving products through warehouses across the world. Users include companies in the air travel, retail supply chain and parcel delivery industries
For Vanderlande Industries, reducing the environmental impact of its conveyor belts and automated sorters has introduced a sea change in how it designs, sources and markets its products. It started with customer requests from the likes of DHL, which put out a call to its vendors for more environmentally friendly products and services, Bossink said.
First came the low-hanging fruit. With a small investment, Vanderlande tested a low-friction belt, a more efficient drive and gearbox and a lighter pulley at its innovation and research center in The Netherlands. The result was the “Greenveyor,” which boasts a 50 percent energy reduction compared to incumbent Vanderlande conveyors.
But there was much more work to be done, Bossink explained. “British Airways asked us to cut PVC out of our products,” he said. That’s when Vanderlande started to realize the scope of the challenges and opportunities it faced.
There were no readily available non-PVC belts. Everything from the type of chrome used to the amount of steel in the material-handling equipment to the grease in the bearings could be improved. “We needed to look at the bigger picture,” said Bossink. “We were not aware of these problems.”
Vanderlande partnered with the Environmental Protection Encouragement Agency (EPEA) to adopt the Cradle to Cradle design process and begin reevaluating its products from the ground up.
After digging deeper into the design and materials that go into its conveyor system, Vanderlande was able to further improve on the Greenveyor. With Blueveyor, it cut energy consumption another 25 percent, making it up to 75 percent more energy efficient than incumbent conveyor systems. The Blueveyor can also cut CO2 emissions by 50 percent, depending on the type of energy powering the conveyor.
One downside: Because the Blueveyor uses a much simpler drive train and belt traction system than either the Greenveyor or older Vanderlande conveyors, it’s not backward compatible, said Bossink. That makes the Greenveyor, which can be placed on older conveyer drives, a better bet for existing Vanderlande customers who want to make a step improvement in energy consumption.
Illustration of conveyor belt provided by iKandy via Shutterstock
Both systems are currently being tested in Amsterdam Airport Schiphol’s baggage handling system. The Greenveyor has been installed at Dubrovnik Airport in Croatia and is being installed Edmonton International Airport in Canada.
Earlier this year, the company released a “Bio Belt” version of its conveyor belt, which does not contain PVC, as earlier versions do, and can be composted at the end of its 3- to 7-year life cycle, says Bossink. The Bio Belt can be retrofitted onto older Vanderlande conveyor systems or used on the Greenveyor system.
Aside from conveyor belts, sorting systems are also significant consumers of energy. Vanderlande’s Crossorter 1500 is its first inspired by the Cradle to Cradle concept and nearly all (99 percent) of its materials are designed for disassembly and recycling. It is also 80 percent more energy efficient than conventional sorters of its type, notes Bossink.
To continue its efforts toward making more sustainable products, Vanderlande is pushing its suppliers to help it reach its goals. “We challenged our suppliers,” said Bossink. “We said: ‘We’re going to do this, if you bring good solutions we’ll choose you, if your competitors bring better solutions, we’ll chose them.'”
And the redesign of the conveyor belts has rippled across the company.
As it began working to improve the design and energy use of its products, Vanderlande brought together a team of 20 engineers to brainstorm ways to improve products and processes within the firm. “The process also touched on other products in development and the designers were influenced by the ideas being shared,” Bossink said. The team found that some parts traditionally manufactured from energy-intensive steel could be made with greener materials, for example, and these discoveries could lead to lighter, more efficient products across the company’s portfolio. Said Bossink: “We began to consider the wider impact.
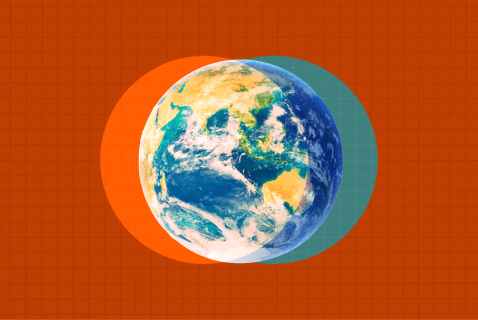