What can sustainability pros learn from Toyota's 'lean' process?
Here's how a university and an airport used the three pillars of "lean" manufacturing to cut expense, fuss and waste. Read More
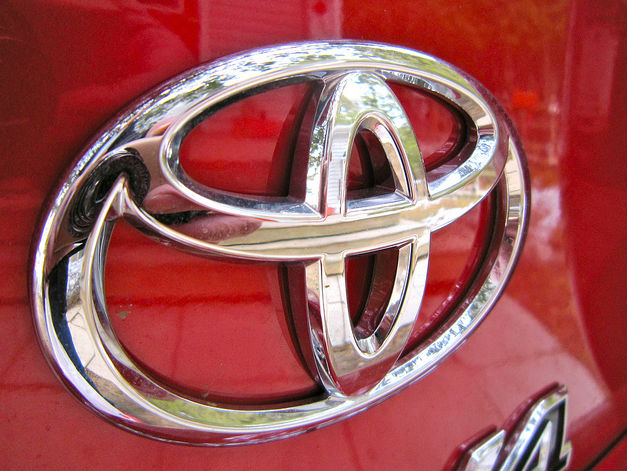
What can sustainability professionals charged with solving complex environmental-compliance issues learn from the auto-manufacturing process pioneered by Toyota Motor Corp.? Plenty, as it turns out.
Lean, the generic term for the management philosophy and practices pioneered by the Japanese automaker, lends itself to thinking about and finding solutions to complicated, multi-faceted environmental problems. Lean pushes organizations away from technocratic solutions imposed by outside technical experts in favor of finding appropriate solutions from the people inside closest to the problem. And because it involves all stakeholders from the first step, the solutions it reveals are inclusive, practical and readily implemented.
Identifying the experts already present
The three pillars of Lean — increasing value, reducing waste and respecting people — fit neatly into a sustainable perspective. Rather than search for outside solutions, Lean seeks answers within the organization. It assumes that the people actually closest to the work, whether they are working on an assembly line or cleaning up a hazardous waste site, are best suited to identify problems and devise robust solutions. In other words, your most knowledgeable experts are the people who clock in daily.
Lean places tremendous emphasis upon perceiving all factors, big and small, that affect a situation. It focuses on the macro view and requires participants to see the big picture. That’s because it’s only by seeing the whole system in which an organization operates that one can understand what its goals are, what its clients and stakeholders value and where problems and waste might hide. Anything that doesn’t support an organization’s goals, or that diminishes the value it seeks to provide, is ripe for elimination.
One of the greatest challenges faced in sustainability initiatives is convincing the rank-and-file to embrace new suggestions regarding how they should perform their job. Here, too, Lean offers a clear advantage: By engaging people in the process of problem solving, it reduces resistance to the recommended solutions. Rather, participants want to see their ideas implemented and be successful because they are their ideas. Lean is inclusive; it is not done to people, it is done by people who feel empowered to create value.
Myopia means miscommunication and missed opportunities
The San Diego International Airport, the busiest single-runway commercial airport in the U.S, is in the midst of a much-needed expansion and improvement program, while also attempting to comply with significant storm-water compliance requirements.
Development plans had lagged because the airport’s internal stakeholders lacked any shared understanding of the big picture in which they had to operate. While planners devised new buildings to meet the future passenger and cargo needs, the facility development staff focused strictly on constructing more drains and outfalls to address the airport’s flood risk. The environmental affairs and legal staff, meanwhile, struggled to address regulatory compliance issue and litigation at every storm-water discharge point. Each group was accustomed to addressing the issues strictly from its own narrow perspective.
The objective was to create an environment where everybody could understand all of the challenges. To do so, it took collaboration with all stakeholders to create a whole-systems view of their storm-water flood risk and water-quality compliance challenge. That allowed each group to break out of its silos and perceive the bigger picture — and see how various storm water and environmental issues interacted and compounded the problem.
When the stakeholders saw how they were each addressing a separate portion of the storm-water problem in isolation, they had a visceral reaction: “This is crazy!” The planners and engineers and compliance staff began to see how they were all part of the problem and the solution. That meant they had to work collaboratively to attack their common challenges.
The result: Airport officials embraced a holistic approach, requiring storm-water solutions be made a part of all future expansion projects. In addition, working across organizational boundaries, officials are developing a strategic master drainage plan linked to the airport’s master development plan that looks forward to the year 2035. Potential cost savings from using rainwater for non-potable uses could be as much as $300,000 annually, while simultaneously reducing compliance costs by hundreds of thousands of dollars annually. At the same time, these initiatives will make the airport more resilient to extreme climate events.
The wisdom of taking a walk
In another instance, an Ivy League university dramatically overhauled its solid-waste management program. At the time, the university diverted only 31 percent of its solid waste from landfills; its goal was to increase that to 40 percent by 2014. School officials didn’t want a recycling program that would sit ignored on a shelf; the new plan had to be readily acceptable to the whole university community and be implementation-ready. In addition, the program had to be aligned with the organization’s Climate Action Plan to reduce greenhouse emissions.
The team started with a Lean mindset: Everyone who touched a waste stream had something to contribute to finding a solution. That meant involving building administrators, housekeepers, students, sustainability coordinators and other players to ensure they fully understood how waste was dealt with. Instead of tackling issues during endless meetings, stakeholders worked in short, focused workshops that encouraged efficiency. Getting all stakeholders in the same room not only created a shared understanding of the problems, leading to rapid identification of areas for improvement, it also fostered a sense of collaboration by overcoming shared challenges.
To comprehend existing recycling problems, tools such as Gemba walks were applied. Gemba, a signature concept of Lean, means to go where the work is done and observe how people do their jobs. That might seem like a simple idea but it’s quite profound, as it turns out that the processes described in a manual or company handbook often have little relation to what occurs in real-life work.
Among the things discovered was that although they occupied the same campus, different schools and departments operated within stringent silos, each adhering to its own waste management process. For example, it turned out there were roughly 110 types of recycling bins and 35 types of signage on campus. Not only was that cost-inefficient, it was incredibly confusing to people who wanted to recycle. By working as a team, signage and bins were standardized and such inefficiencies were reduced, producing more uniform recycling messaging and cost-savings.
Ultimately, the university’s solid-waste management program was recreated as a campus-wide collaboration. New alliances and relations were formed: More than 15 schools and departments created a variety of cross-functional partnerships to get the work done. Teaming up with the end-users, a Solid Waste Plan was created that identified 71 problems in the current system and devised 125 ideas to address them.
Most important, because the plan was rooted in university members’ own experiences and ideas, they did not need to be convinced to embrace it. Instead, the plan sold itself, leading to its quick adoption and implementation. The university is tracking to clearly identified metrics, and is expecting to exceed its initial goals.
Three pillars to build a better everything
By focusing on increasing value, decreasing waste and respecting people, Lean is ultimately about transforming how work is done, to make it more efficient and sustainable. Whether you’re trying to build a building a better automobile or a better world, that’s a worthy goal.
Toyota image by Kate Ter Haar via Flickr.
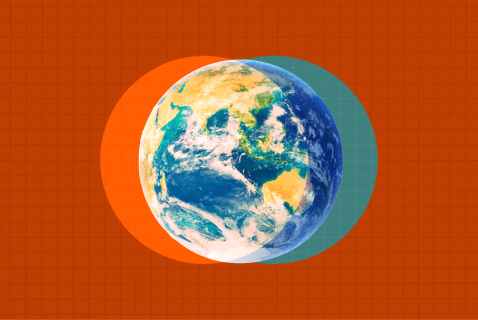