Xerox Employees Mix Innovation, Initiative to Protect the Environment
Some Xerox Corp. employees stopped using plastic spoons and forks in company cafeterias. Others found a way to turn more waste into electrical power to heat homes. And still others devised a process that reduced the amount of water used in a key manufacturing process. Read More
Some Xerox Corp. employees stopped using plastic spoons and forks in company cafeterias. Others found a way to turn more waste into electrical power to heat homes. And still others devised a process that reduced the amount of water used in a key manufacturing process.
These enterprising efforts are among the 14 projects that Xerox is recognizing tomorrow under its “Earth Awards” program, which honors employee teams throughout the world who have come up with innovative ideas to help protect the environment and improve the performance of the company’s operations.
These employee teams demonstrate that what is good for the environment is also good for business. In 2003, their projects saved Xerox $5.5 million, eliminated more than 16.5 million pounds of waste, and reduced energy consumption by more than 4.2 million kilowatt hours – enough power to light 175,000 homes for one week.
The Xerox Earth Awards began in 1990 and this year, 14 teams were selected for awards out of 46 worldwide entries. The winning teams were located in Webster, N.Y.; Wilsonville, Ore.; Mississauga, Canada; Nogales, Mexico; Dundalk, Ireland; Rampur, India; and Mitcheldean, United Kingdom. All will be honored tomorrow at a ceremony designed to coincide with Earth Day. Since the program was started, Earth Award teams have saved Xerox more than $235 million.
“These Earth Award winners are proof that even the smallest efforts to reduce waste and emissions can add up to significant savings and improved environmental performance overall,” said Jack Azar, vice president, Xerox Environment, Health and Safety. “Over the years teams have found dozens of ways to improve manufacturing processes, drive down costs and conserve natural resources all at the same time.”
Here are some of the winning projects for 2004 and how they are making a positive impact on Xerox and the environment.
— Turning waste into electrical power. Xerox has long ensured that waste toner – which includes manufactured toner “fines,” or toner not included in the final product, and post-consumer “used” toner – is not unnecessarily disposed of in landfills. Waste toner has been sent to a municipal incinerator to be burned and produce power in Niagara Falls, N.Y. In 2003, a team in Webster found a way to expand this “waste-to-energy” program to include the safe disposal of other materials such as used toner bottles and cartridges. Last year, the Webster Toner Developer Plant sent about 430 tons of toner-related waste for waste-to-energy recovery, which generated 970,000 kilowatt hours – enough power to light more than 40,000 homes for a week. As a result, the Webster facility boosted its recycling rates to over 97%.
- Reusing components of Xerox office products. This team, based in Wilsonville, felt they could find a way to reuse the metal circuit board stencils in Xerox office products. A circuit board stencil controls the operational functionality of the machines, and previous recycling methods of these stencils were not viewed as maximizing cost savings. The team devised a system to reuse the stencils either whole or in part. If the used stencils cannot be incorporated into new designs, the metal is recycled into stock for new ones. Xerox benefits by being able to purchase new stencils at a lower price. In all, the new processes save Xerox $10,000 annually and reduce environmental impact.
- Reducing water consumption in manufacturing. When Xerox manufactures emulsion aggregation toner, called EA Toner – which is grown from chemical compounds into the toner particles used to make images in printers and copiers – it uses a lot of water. An employee team in Mississauga decided to find a way to reduce the amount of water needed which in turn would reduce the amount of “wash” wastewater needing treatment before disposal to the sanitary sewer. By changing the toner “wash” process, the team reduced the number of washes per toner batch from five to three. This new process is expected to save 1.3 million gallons of water in 2004 and reduce the cost of wastewater disposal by $66,233.
- Cutting out plastic cutlery. For SUMEX (Supplies Unit Mexico), which is Xerox’s remanufacturing facility in Nogales, Mexico, recycling has long been a way of life. Last year, SUMEX managers had the idea to eliminate plastic forks, knives and spoons in order to reduce waste from the cafeteria. Each of the 300 workers on-site receives their own set of metal utensils and a ceramic coffee mug with their name printed on the side. As a result, cafeteria waste was reduced by 8,600 pounds last year. Another team in Nogales identified an opportunity to reduce waste by rebuilding used wooden pallets. The pallets recovery process saved $97,700 and reused 13,316 pallets in 2003.
- Giving new life to old equipment. Employees in Dundalk thought they could save money by changing the way they remanufactured parts from Xerox DocuTech production publishers and DocuTech production printers. Machine parts called finisher harnesses, which help connect high-speed printing equipment to the finishers that staple and collate print jobs, and parts called fuser rolls, which fix images to paper with heat during printing, were originally removed from the machines and replaced with new parts. The team identified remanufacturing opportunities and now the parts are modified and brought back to same-as-new quality. This resulted in total annual cost savings of $268,039 and an annual scrap weight reduction of over 10,000 pounds.
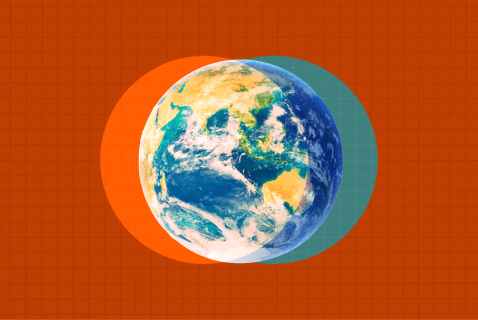