Xerox Saved $2 Billion Through Eco-Design and Manufacturing
The Xerox Corporation has announced that its efforts to design environmentally friendly products and manufacturing processes over the past ten years have resulted in more than $2 billion of costs saved or avoided, and the equivalent of 1.8 million printers and copiers reused or recycled. Read More
The Xerox Corporation has announced that its efforts to design environmentally friendly products and manufacturing processes over the past ten years have resulted in more than $2 billion of costs saved or avoided, and the equivalent of 1.8 million printers and copiers reused or recycled.
“In 1991 we pledged to be an environmentally responsible corporate citizen, and designing for the environment became fundamental to the way we do business,” said Jack C. Azar, Xerox vice president of environment, health & safety. “Since then our product development process has started with environmental as well as performance goals – and we’ve constantly kept innovating to ensure components are designed to be used for more than one product lifetime.”
Xerox said it calculates that the company, its customers, and the communities where it operates have realized significant benefits from Xerox’s pursuit of waste-free products from waste-free factories. Xerox pioneered remanufacturing for printers and copiers, a process by which returned products and parts are upgraded and rebuilt to as-new appearance and performance. The company has also introduced more that 200 Energy-Star qualified products since 1993.
Xerox estimates that its reuse and recycling initiatives have kept 1.2 billion pounds of electronic waste out of landfills. The company said that it has reused or recycled more than 90% of the 7 million cartridges and toner containers returned by customers in 2000 alone, preventing 14 million pounds from reaching landfills.
Xerox has also taken steps to eliminate hazardous materials from its products. The company has stopped using brominated flame retardants and mercury-containing switches and relays, and is phasing out all use of mercury, which is currently found in a few user displays and scanner lamps. A phase-out schedule for lead is under way.
The company said that, although it feels that its 10-year experience demonstrates that remanufacturing can help electronics producers meet environmental goals without compromising product performance, the industry continues to be challenged by barriers to recycling and remanufacturing.
“Despite a decade of proof, there are still buyers who believe that products with recycled-part content are not as good as those built with all-new parts,” Azar said. “Ironically some of the most inflexible purchasers are state governments — the very entities that are concerned with landfill issues.”
“Market forces will ultimately determine the success of environmentally friendly practices such as reuse, which is the form of recycling that delivers the most environmental value. Smart public purchasing policies and practices will avoid constructing barriers to reuse and instead focus on the quality and performance of the products regardless of recycled content,” he concluded.
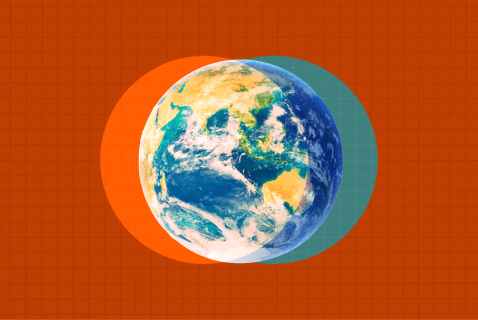