Once is Not Enough: Continual Improvement is Essential to Sustainability
Improvement is a major ingredient in the process of attaining sustainability and has to be part of what every employee does every day — day in and day out, says Robert Pojasek, who offers advice on how to set those targets. Read More
Improvement is a major ingredient in the process of attaining sustainability. Organizations use a variety of different programs to drive this improvement. These programs go under the names of lean, six sigma, TQM and CQI. However, more than half of all improvement programs fail during the first three years of use. What organizations fail to realize is that there has to be a commitment to continual improvement embedded within the fabric of how the organization is managed. Improvement cannot come just from a program operating as its own separate silo. Improvement has to be part of what every employee does every day — day in and day out.
A sustainability management system makes improvement part of the way an organization is operated. A commitment is made to continual improvement, and monitoring and measurement are used to make sure that the improvement is being accounted for. In the management system world, this improvement is called continual improvement. The management system “police” explain that this is different from what the quality management folks call continuous improvement. When they hear these rants, the quality management folks just shrug their shoulders and say, “Get a life!” Continual improvement is recognized as the most effective way for organizations to improve efficiency and improve quality.
Lean practitioners have adopted a Japanese approach to continuous improvement. It is called kaizen. This term signifies a daily activity, the purpose of which, when done correctly, eliminates overly hard work and helps people find and eliminate waste in their activities. People at all levels of an organization can participate in kaizen. This practice involves a small group in improving their own work environment and productivity. While kaizen usually delivers small improvements, the culture of continual aligned small improvements and standardization yields large results in the form of compound productivity improvement.
![]() |
There are those who detest continual improvement because it tends to be “incremental” in nature. After all, this is not what they call “breakthrough” improvement. These continual improvement bashers are hooked on innovation and feel that sustainability depends on innovation. Sustainability peacemakers point out that incremental improvements followed by “lessons learned” and “knowledge management” can actually drive innovation. “Not so!” exclaim the incremental bashers. We told you that sustainability was not going to be easy.
Some of the lean followers have been connecting to a relatively new bushiness excellence framework designed especially for lean programs. This effort is referred to as the Shingo Model. Every organization with a lean program that has worked its way past the “low-hanging fruit” should become familiar with this program. It is an important linkage if the organization is considering a drive to sustainability.
I have had a good deal of success linking lean and six sigma programs to management systems. This can be accomplished by making lean an integral part of the formal program that addresses the sustainability goals. In addition, lean and other process improvement methods can be used for corrective actions and preventive actions. The author developed the Systems Approach to address preventive actions often referred to as pollution prevention or cleaner production. This approach is presented in the US Environmental Protection Agency’s publication, “An Organizational Guide to Pollution Prevention.” This offers a great way to make continual improvement continual.
You can begin to appreciate that even the basic components of sustainability — like the ways to address improvement — are not subject to standardization. Although some have tried, it is difficult to formulate a packaged program that will address the needs of all organizations. By addressing the five basics presented in this blog, any organization can pick and choose, even adapt, these components in a program that will work best in their organization. The management system does not need to be ISO-certified. The business excellence framework does not need to be Baldrige or Shingo compliant. And the process improvement method does not need to be formally inked to the Toyota Production System.
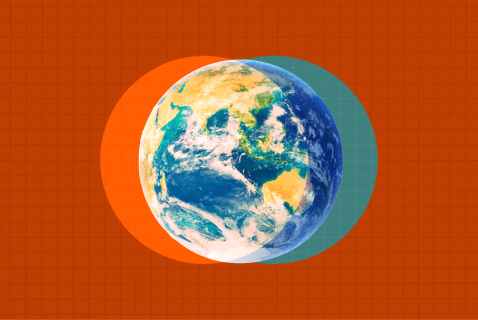