The pipe dream of sustainable plastics
What would need to happen for plastic building products to be considered truly sustainable? Read More
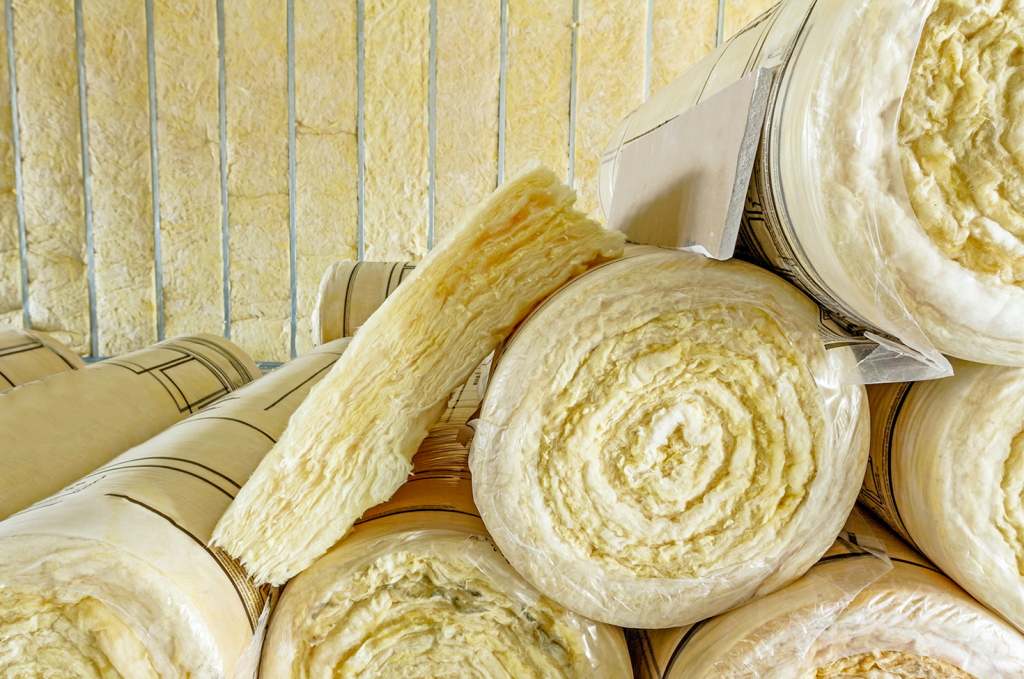
Package of thermal insulation material
This article was originally published on Environmental Health News. Read it here.
You’ve probably been hearing a lot lately about the negative environmental and human health impacts of plastics. And for good reason — its global production is expected to more than triple between now and 2050.
According to industry projections, we will create more plastics in the next 25 years than have been produced in the history of the world so far.
While plastics touch nearly every aspect of the market, they are especially ubiquitous in our buildings. The building and construction industry is the second largest use sector for plastics after packaging. Plastic production relies on a variety of hazardous chemicals and contributes to greenhouse gas emissions at every stage of the lifecycle. And while there is a lot of talk about recycling, the truth is that virtually no plastic building products are recycled into equal use materials today.
Given this info, we believe the best way to avoid hazardous chemicals and support a circular economy in the building industry is to avoid plastic building materials altogether.
But we also believe in the power of the market to drive innovation. So, let’s consider what would need to happen for plastic building products to be considered truly sustainable. Can the plastics industry do better?
What would be defined as a sustainable plastic?
Healthy Building Network recently developed two case studies for the international Organization for Economic Co-operation and Development (OECD) as part of the Inter-Organization Program for the Sound Management of Chemicals (IOMC). The studies created a framework for evaluating what a truly sustainable plastic product would look like. While they use flooring and insulation as examples, the framework can be applied to any durable plastic product.
These goals are lofty, and currently no existing plastic building materials meet these criteria. However, they provide a pathway towards truly sustainable products.
To be considered a sustainable plastic, a product would have to enhance human and environmental health and safety across the entire product life cycle. It would have to be managed within a sustainable materials management system, and would have to meet the following goals:
- Must be inherently low hazard.
- Hazardous substances are eliminated.
- Transparency exists in terms of content and emissions at every step of the supply chain.
- Full hazard assessments are available on all chemicals.
- Must have a confirmed commercial afterlife.
- Products are designed for durability, reclamation, reuse, and recycling.
- Infrastructure exists to support reclamation, reuse, and recycling.
- Materials can undergo multiple cycles of recycling.
- Must generate no waste.
- Manufacturing scrap is eliminated at every step of the production process.
- Scrap from installation is eliminated.
- Must use rapidly renewable resources or waste-derived materials.
How do contemporary plastics perform against these proposed goals?
The OECD case studies detail chemical considerations for flooring and insulation plastic product types at all life-cycle stages.
For the flooring category, Healthy Building Network reviewed vinyl sheet and tile (polyvinyl chloride, PVC), wood plastic composite (WPC), and polyethylene terephthalate (PET or non-PVC resilient) products. In one example analysis from the case study, Healthy Building Network looked at the goal of “must be inherently low hazard” specifically during product manufacturing. PVC and WPC products require the use of additives that can be hazardous. PET flooring inherently does not require the use of most additives but can contain a residual chemical of concern.
For the insulation category, Healthy Building Network reviewed expanded polystyrene (EPS), extruded polystyrene (XPS), polyisocyanurate (polyiso) and spray polyurethane foam (SPF). In one example analysis from the case study, Healthy Building Network looked at the goal of “must have a commercial afterlife.”
Currently, nearly all insulation materials are landfilled. SPF and polyiso are thermoset materials, meaning that they cannot be melted down and remade into new materials. However, both XPS and EPS are technically recyclable as thermoplastic materials, although we lack the technology and infrastructure today to do it at scale. This means that XPS and EPS could, theoretically, have a commercial afterlife, while SPF and polyiso could not.
Opportunities for improvement
The analysis highlights opportunities to avoid hazardous chemical impacts, for example, through product design, material choices, manufacturing processes and implementation of policy instruments that could reduce the negative impacts of the product throughout the life cycle. It also explores trade-offs that exist between material choices.
For a flooring example, a product designed to use adhesive to install is typically thinner than one that uses a click tile system to install. These thinner products use less material per square foot and therefore have less chemical impacts associated with manufacturing and less waste at the end of life. However, adhesives may add hazardous substances to the product installation stage. By moving from a click tile product to a glue down product, chemical exposure burdens shift from manufacturing and end of life to the installation stage and use phase.
For an insulation example, a product that is designed to chemically react at the build site, such as spray polyurethane foam (SPF), can allow the insulation to form an air-sealed custom fit. However, SPF is not recyclable, and adherence of that insulation to surrounding materials may also make those materials more difficult to reclaim or recycle. Moving from XPS, EPS or polyiso to SPF may reduce the ability of other surrounding materials to “have a commercial afterlife” in the pursuit of an added performance feature.
Building awareness around these trade-offs enables stakeholders to make informed choices.
Back to reality
Now, back to reality after crafting the characteristics of a theoretical sustainable plastic. The bottom line is that no truly sustainable plastics exist today, and we are a long way off from that day. Today, project teams need to prioritize which sustainability goals are most important and how to deal with real and significant gaps in understanding and/or data.
The case studies compared only product types made of plastic, but in reality, project teams have a wider variety of materials to choose from in any given product category. In project design, the biggest leaps towards more sustainable products from a chemicals perspective often requires consideration of vastly different materials versus making incremental improvements in chemistry for a particular product type. For example, this could mean moving from vinyl to linoleum flooring versus attempting to select the least bad vinyl option.
Healthy Building Network’s Product Guidance considers the most commonly used product types within a product category and ranks those product types relative to one another from a chemical hazard perspective. Product types made of plant-based materials or minerals tend to rank higher than plastic products. You can apply the same sustainability goals proposed in this article to non-plastic products.
Check out the full flooring and insulation case studies for examples of how to use these goals to consider and choose the variety of plastic product types you will inevitably specify for your next project. Alternatively, challenge yourself to skip the plastics whenever possible. Even selecting one non-plastic product makes a meaningful difference and is cause for celebration.
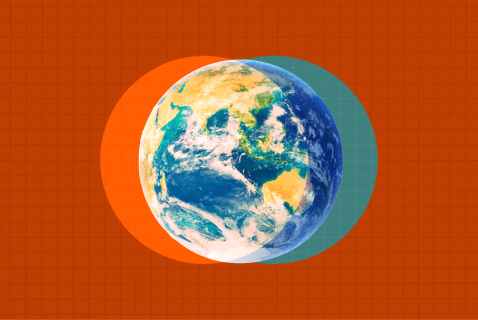